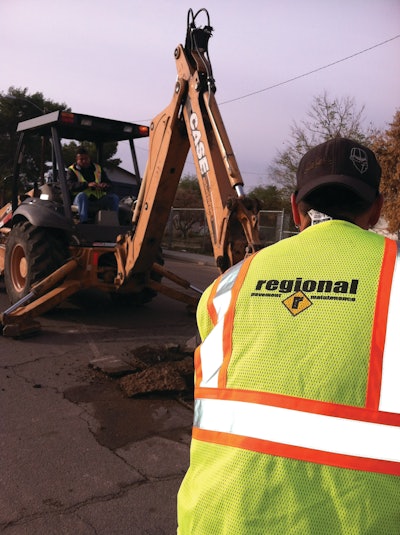
Safety may not be in the forefront of your mind every moment of everyday, but Stephen Leone, Co-Owner of Regional Pavement Maintenance of Arizona (RPM), tries to teach his employees that it should be. Leone and his partner, Joe DiGiugno, have been in business together in Arizona for the pasts 11 years, but Leone admits it wasn’t until an unfortunate accident six years ago that the company opened their eyes to the need for a strong safety message.
“Our company exploded and we grew every year through the recession,” says Leone. “The growth was much more than we expected, and when you’re growing and buying equipment, safety is something that gets pushed to the side a little bit. I don’t think anyone who gets into this business starts off having a safety policy, then all of a sudden you have your first major accident that really opens your eyes.”
RPM’s eye-opening experience happened about six years ago. They were sealcoating, hot crack sealing and striping a shopping mall parking lot, moving along and completing one section after another. Like every job before this one, RPM placed orange safety cones and yellow caution tape around the areas they were working on to alert the public to steer clear.
“A woman was driving with her eyes into the sun, didn’t see the barricade and drove right through,” says Leone. “One of our workers was blowing the parking lot with his ear protection and reflective vest on, and even though he was working in a protected area, this woman drove right over him.”
Leone has no problem discussing the incident and makes it clear the worker was not injured in vain. “An accident is sometimes an accident,” says Leone, “but in another sense there has never been an accident that couldn’t have been prevented and we try to keep that approach. You shouldn’t have to grow into a safety policy, it’s as important as any piece of equipment you buy. We now go out of our way to make sure nothing like that ever happens again.”
Safety is not a choice
The scope of safety precautions required can vary from job to job. Some companies will require you to wear hard hats, safety glasses or other protective equipment depending on what the job entails. Other sites require daily tailgate meetings and it’s up to whoever is running the site to make those choices for the contractors on the job. RPM took the option of choice out of the equation.
“It shouldn’t be the customer that requests that or the jobsite that requires those things,” says Leone, “A lot of companies will do only what is required, we just made it our policy to always do it.”
That’s why when each new employee is hired, they are immediately inundated with the message of safety. “Every new employee is given an employee manual with the safety policy,” says Leone. “We also give them work gloves, safety vests, ear plugs, safety glasses and assign them a hard hat.”
Leone says any and all safety equipment is readily available for his employees and RPM also holds daily and weekly review safety meetings for each job.
“Safety is not something that is going to be absorbed into your face every second,” says Leone. “You don’t sit at a desk and wonder if you’re using a pen properly but subliminally we’re always pushing the message of safety.”
Every few months, RPM will give all their employees a new piece of safety gear with the company logo on it. From blaze orange ballcaps with reflective tape on it, to yellow long sleeve shirts for the cold days and breathable reflective shirts for when it’s hot, the company is able to continually send their safety message in a fun way their employees can appreciate. Considering RPM employs anywhere from 44 to 64 employees, that’s a huge commitment to the reinforcing the company’s safety culture.
“We do something different every time,” says Leone. “So maybe they aren’t thinking about safety all the time, but subliminally when they look at the guy with the orange hat on or, see the new safety vests, they think about it. We try to keep in constantly in front of their face.”
These continual safety efforts seem to be paying off. Before the first incident six years ago, RPM had gone through their first 1,678 days in business without an accident. After their new policy, the company is now at 1,841 days without any accidents.
When it comes to non-compliance, it’s obvious that RPM hasn’t really had to approach that subject with their employees, but they still have penalties listed in their safety manual for any violations. The manual states that if you are caught in violation of the safety manual, you will be issued a citation. Violations include being in a company involved accident, receiving a traffic ticket in a company vehicle or damaging company equipment. If an employee is issued a citation, they are required to appear before a “Safety Review Committee” that consists of the project manager, vice-president and president of the company.
The 14 page safety manual outlines procedures employees and safety managers should follow for different types of accidents. It’s extremely detailed and you can tell they take the policy very seriously. The manual ends with this statement: “Nothing is more important than safety! Safety is everyone’s business, and safety requires teamwork. From the time that you arrive for work, you should be aware of the requirements of the project of projects for the day. Safety is something you never want to take for granted.”
RPM does not take safety for granted and was recently validated for their efforts during a recent Loss Control survey conducted by Allied Insurance. The purpose of the survey was to gather information regarding RPM’s operations and activities and to evaluate internal safety efforts and controls. The Risk Management report stated: “As a result of this survey, no recommendations for improvement were noted,” according to Scott Turner, loss control specialist at Allied Insurance.
Employees are just the beginning
Leone says a big part of safety that doesn’t seemed to be touched on very much is equipment maintenance. “You’ll see a lot of accidents that happen from equipment overheating, parts vibrating apart, etcetera, ” says Leone. “Your equipment has to be safe in order to put your workers in the safest situation possible.”
RPM hired a night mechanic to look over the equipment after every work day. “The crew will go out and if they identify a problem with a machine, they will turn in a checklist with their job sheet at the end of the day,” says Leone. “They’ll give the performance of the job and what worked. Obviously if there are any equipment issues that need to be checked, we don’t want them going out the next day with a piece of faulty equipment that may break, burn or explode.”
Raising public awareness
Some companies think that once they educate their employees about safety, their job is done. RPM knows from experience that is not the case.
“The accident that happened really wasn’t our fault,” says Leone. “If I’m just making safety an internal thing and not making the public aware of it, I’m only solving half of the problem.”
The company has created custom project awareness signs that they place around every jobsite, along with safety cones and caution tape. These signs have the name and location of the project along with project dates, the company logo and their contact phone number. The signs are designed to restrict access and alert the public of work being done.
RPM also has turned to social media to help make the public more aware of projects they are working on in different areas. Since their service area covers all of Arizona, they are able to communicate with a wide range of people about current and upcoming jobs through their Facebook page.
“When we start a new project, we make an awareness to those people about getting our workers home safely,” says Leone. “They may see the cones and the barricades but we want people to know that it’s not just a guy in a hard hat behind them. He has a family and maybe a couple of kids. He’s out there doing a service for you, so let’s get him home safely to his family.”