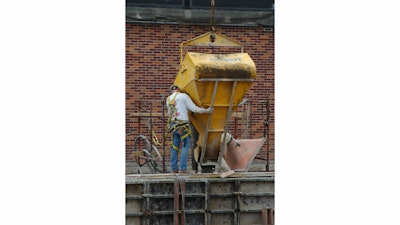
This summer, OSHA launched a week-long campaign called the National Safety Stand-down to Prevent Falls in Construction to raise awareness for all good working stiffs to wear their safety harness and tie it off to something. We wish it were so simple.
OSHA really does try, but let's face it, the odds are long that you're going to get caught. Yes, cell phone cameras may catch you in the act, but response by OSHA is still sporadic at best. Fully one third of all construction deaths are from falls. In 2012, this represented 280 people.
A few years ago, OSHA tried to push the issue higher upstream - to the architect and design level - to help the poor schlubs in the field cope with staying alive during construction. Results have been mixed. In steel erection, for example, we still see wire rope top and mid-rails strung column to column across open floor edges, using the primitive practice of welding nuts to columns as anchorages. The unions finally came on board and adopted fall protection into their Apprenticeship Programs, which actually helped industry-wide acceptance.
Meanwhile, the safety hardware vendors have worked overtime to come up with some ingenious solutions to chronic fall protection problems. These solutions are helping to answer the question: “Where can I tie-off to easily?” There are anchorages available to fit practically any application. It’s just a matter of how hard you look for them before resorting to the “way it’s been done since horse & buggy.” When all else fails, find the heaviest C Clamp on the site.
Say It In the Manual
In any case, you should have a written Safety Manual with a chapter in it titled Fall Protection Safety Policy, with the following statement: “We, the employer, will provide fall protection, and you, the employee, will faithfully wear it.” Also in this Chapter should be your fall protection produce, which specifies exactly how the fall protection will be implemented and, most importantly, who is responsible for making it happen.
The section on Best Practices for Fall Protection Program Management should specify:
• Employee Fall Protection Training
o An explanation of the company fall protection program
o How to identify the risk of a fall
o The physics of falling, weight and distance
o What to tie off to/what makes an adequate anchorage
o How to properly put on the harness
o Harness care and inspection
• FP Hardware
o Harness vs. positioning belt
o D-rings, weight distribution
o Anchorage details
o Energy absorbing lanyards
o Rigging and attachments
o Retractable reels, rope grabs
The reliability of FP hardware is very high. It rarely fails. Usually, a failure is due to carelessness, abuse, misuse, failure to inspect and/or failure to use as instructed. Welding and torch cutting need special protection.
Reality: The average harness sits on the floor or in the bottom of a job box. They are basically treated like dirt. This is an OSHA PPE technical foul.
Best Practice: Treat that harness like an article of fine clothing. If you paid $50 to $300 for a life-jacket, would you let it get kicked around? Assign it to an employee as PPE.
Other fall protection topics on your training agenda should include:
• Proper installation of fall protection systems
o Why railings are preferred
o Alternate methods, such as nets
• Supervision to ensure your fall protection systems work
o Daily inspections to prove it
Common Fall Protection Fails
Just like “Best Practices,” these are among the “Best Excuses” for evading fall protection responsibility from medical examiners’ reports:
1. I had no place to tie-off to. This means you didn't have a plan, supervision, a clue. No pre-job safety analysis.
2. My supervisor wasn’t looking. I didn’t think he’d mind; he told me to hurry it up.
3. I was just going up there for a minute to check something. Failure to plan, properly assess the work.
4. It was too hot to wear a harness. Trading one minor irritant for a life-threatening one? Very unwise.
5. It was all the way back on the truck (the shop, the office, the trailer…) Laziness. Failure to plan.
6. It didn't look that high. Myopia. Failure to plan.
7. I didn't see the edge. Failure to observe surroundings. Distractions. Inattention. Hurrying. I tripped. Clumsy
8. No one told me there was a drop-off. Reliance on others for your safety. Failure to observe surroundings.
9. The guy who was already up there didn't have one. Reliance on others for your safety is unwise.
10. I forgot. Self-explanatory; failure to plan. Get more sleep.
Summary
We are here to teach you how to work safely, not find excuses for shortcuts. There will always be trade-offs, but at least you can make an intelligent decision based on risk analysis and not guesswork. The day will not be too far off when your insurance company does their own investigation before deciding if they’re going to cover the claim. Keep that Safety Manual handy.