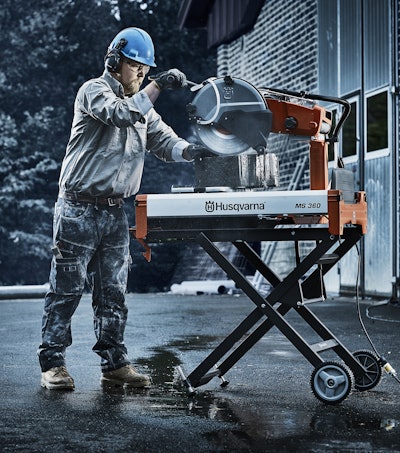
“OSHA”, “PELs”, “Silica” and “Final Ruling” are major buzz words right now in the construction industry. Since OSHA released the final ruling on crystalline silica exposure on March 24, 2016, the industry has been buzzing with questions about whether or not it is fair to contractors and other "what if" questions.
The existence of crystalline silica and the hazards it can cause to a worker’s body—lung cancer, chronic obstructive pulmonary disease and kidney disease—has been known for decades. The OSHA ruling is revising the amount of crystalline silica a worker should be exposed to. The key takeaways of the ruling include:
- The permissible exposure limit will be set at 50 micrograms per cubic meter of air, averaged over an eight hour shift.
- Employers will be required to take measures to control silica, either through using water, ventilation or providing respirators. Employers will also be required to limit the amount of time a worker can be exposed to hazardous environments, write an exposure control plan, offer medical exams to highly exposed workers and train workers on the risks and how to avoid silica dust.
- OSHA will provide help to employers.
The OSHA ruling places a lot of weight on the contractor’s shoulders, but manufactures are here to step in to help. As a manufacturer of products that cut concrete and brick, two major sources of crystalline silica, we are always trying to find the best solution for our customers—from both an efficiency standpoint and from a worker’s view. OSHA has been working on a final ruling for the past several years, and since the first ruling on silica exposure Husqvarna Construction Products along with other manufactures in the industry have been working to develop ways to suppress the silica and keep workers more safe. The OSHA ruling gives a more precise indication of just how much dust will need to be reduced with the established permissible exposure limit (PEL) and microns of silica dust per cubic yard of air. Currently, there are several ways to protect the worker from silica exposure—water, ventilation and respirators.
Equipment features
First, let’s explore suppressing dust with water. Workers cutting concrete or brick are the ones most affected by the OSHA ruling and handheld power cutters or masonry saws are used for this type of work. On handheld power cutters, a lot of manufacturers use water to reduce dust. The trick is to use just enough water to bind the dust, but not so much water as to create a lot of slurry. If workers are cutting pavers or bricks, you also do not want a lot of water saturating the piece to the point that the mortar won’t adhere properly. This is why manufacturers try to control the amount of water, for example:
Husqvarna Construction Products’ power cutters are equipped with a dust management system called DEX. DEX features a progressive water valve that is fitted with distinct end positions, making it easy to set the exact water flow for any application, which minimizes water consumption and slurry. The main benefit to contractors may be in the use of portable water tanks, such as spray bottles. Husqvarna also has a battery powered four-gallon tank, the WT 15, that provides continual pressure for water delivery. Traditional watering systems use a lot of water and portable tanks run out too soon, but the DEX system allows for much longer use with portable systems.
The recently introduced MS 360 masonry saw is also equipped with a water system. Its patented water containment system keeps water, slurry and debris controlled; resulting in a nearly dry block or brick for faster utilization. The water used is stored within the saw, so workers do not have to carry multiple pieces of equipment.
The use of vacuums to reduce dust before it spreads into the air is another popular way to remove the crystalline silica from the environment. Vacuums are one of the best solutions when workers need to operate without water – such as when grinding concrete in surface preparation applications. Vacuums are equipped with multiple filters to take care of small particulate matter and collect it for easy removal.
Training materials
Another way manufacturers can help workers is through training. Training and teaching workers how to be safer with silica and why it is important to use equipment that suppresses dust is important for their safety. Operator’s manuals that accompany equipment are useful tools for safety and training. Documentation includes information on dust levels and how specific levels have been identified.
In addition to the operator’s manual, online user guides for handheld power cutters and other equipment are excellent for tailgate training session on location. Both professional concrete cutters and masons as well as the rental customer can understand and benefit from these guides.
Contractors can also reach out to the manufacturer or their dealers who offer training and can usually accommodate individual contractors with on-site demonstrations and safety tips.
What can contractors do now?
Before the ruling is fully implemented, there are several items contractors can start doing now to help with the transition.
The first is to take a step back and start observing how you or your operators are working.
- Are you cutting dry? If so, is there a lot of airborne dust generated?
- What can you do with your current equipment to reduce dust?
- What (if any) additional new equipment may be needed to comply? This could be the addition of a portable water tank, vacuum, etc.
- Are you using any type of protective equipment – safety glasses, hearing protection, respirators?
- How long are your operators working?
By critiquing current methods and environments now, contractors can start to see where the OSHA ruling might affect a typical workday. Contractors can start taking steps to reduce the amount of dust by perhaps introducing equipment that helps protect the worker from silica exposure – by using water, ventilation and respirators. Another option would be to limit the amount of time operators are exposed to a dusty environment. If contractors start now to test some solutions for productivity, and find what works for them business, they will be ready for full implementation in 2017.
OSHA’s silica website, www.osha.gov/silica, is another resource available to learn more of the specifics on the ruling and the available assistance OSHA is providing construction businesses.
Husqvarna Construction Products and other manufacturers are here to help work together and move forward with the ruling. Through innovations in technology that help reduce silica as well as through education and on-site demonstrations, we are here to support the contractor and the construction industry.
Ed. Note: Mark Michaels is the Director of Product Management – Equipment at Husqvarna Construction Products.