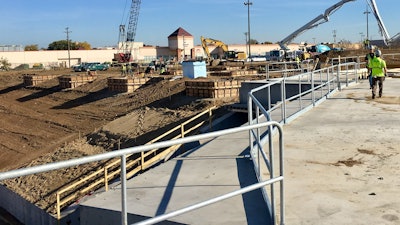
Conventional guardrail systems are constructed on the jobsite of lumber and are time-consuming to build and erect, require constant maintenance and are commonly discarded as waste at the conclusion of projects. Budgeted costs associated with constructing and maintaining this type of guardrail are significantly underestimated.
Successful contractors are constantly evaluating how they perform their work to identify cost-saving measures. M.A. Mortenson, Minneapolis, MN, like many other contractors, for years had been erecting wood guardrail systems to protect unguarded edges and openings. Where feasible, a passive guardrail fall protection system is actually preferred over personal fall protection (i.e. body harness) as it allows work to be performed more efficiently and with less opportunity for human error.
An engineered guardrail system can help reduce waste typically created with a wood guardrail system.Hilmerson Safety
Budgeting for guardrails
When preparing project budgets, a per liner foot cost is commonly applied for guardrail needs. However, taking a closer look there are many unaccounted-for costs, and risks, that contractors fail to identify. When budgeting a wood guardrail system, a truer calculated cost of $19 per linear foot should be applied when factoring-in all of the following during the project life-cycle:
- Shipping lumber to the jobsite then moving and handling it to the point of installation
- Inspecting each piece of lumber for defects and condition then measuring and cutting each piece to length
- Handling no less than four pieces of lumber for each 8-foot section of guardrail — top rail, mid-rail, toe board and upright posts.
- Continual maintenance and repair due to damage, weather deterioration or the occasional “borrowing” of lumber from a rail section. For these reasons more frequent inspections should also be conducted.
- Disposal costs of discarded lumber
- Labor associated with sorting and bundling recycled lumber for future projects
It was proposed that cost containment could be achieved by investing in the development of a sustainable guardrail solution where the ROI could be realized in just a few projects.
The need for an engineered system
The completion of a cost-benefit assessment reinforced the need to develop an engineered system to eliminate lumber waste and significantly reduce the labor associated with constructing conventional wood guardrails. A sustainable guardrail solution could be obtained by satisfying just three elements — simple, efficient and tough — all of which were not currently available in a commercially fabricated guardrail. With a robust guardrail system, a sizable impact could be made on reducing lumber and labor waste. Additionally, by applying Lean processes, a significant reduction in risk of injury could also be achieved.
Using a guardrail cart to transport the engineered guardrail system helps increase efficiency in assembly and reduce injuries associated with material handling.Hilmerson Safety Services
Lean approach reduces risk
The challenge for all contractors is to maintain a reasonable balance of productivity, quality and safety to ensure an injury-free outcome. When schedule and budget are compressed and greater emphasis is placed on production, injuries are more likely to occur. Applying the Lean approach to the design of an engineered guardrail system helps combat injury and reduce risk by:
- Use of lower consequence power tools in the form of a drill versus a pneumatic nail gun and circular saw to prepare and install components
- Unitized delivery and movement via a wheeled cart to the point of installation minimizes lifting and carrying components
- No nails or screws that present a cut or impalement hazard and wood splinters to dig out of hands
- A manufactured engineered system always conforms to the OSHA guardrail performance requirements providing for a safer condition and lower risk of violation
- The application of swing gates for secured access
- An integrated toe board provides for falling object protection all the time and debris netting is easily installed using clips
- Less time spent at a leading edge installing an engineered rail versus a wood rail
Mortenson implements engineered system
The partnership formed between Hilmerson Safety and M.A. Mortenson has allowed the engineered guardrail system to be used on several projects and go through a series of modifications to ensure it meets the needs of the end-user and returns the value demanded by Lean principles. To date, the guardrail system has been deployed on three M.A. Mortenson projects including two professional sports stadiums and a 26-story high rise building and has returned the following:
- Elimination of 80,000 linear feet of wooden guardrail
- A 60% reduction of installation and maintenance labor
- No reported injuries during installation and handling
Dan Hannan, CSP, is the Director of EHS at Hilmerson Safety. Hilmerson Safety is a full-service safety product design and manufacturing company serving the construction, manufacturing, and oil and gas industries. Since 2001, Hilmerson Safety has been working with construction industry leaders and contractors to develop safe, lean, construction grade products and solutions that add to a company’s bottom line. To view more information about the Hilmerson Safety Rail System and the Hilmerson Barrier Fence System visit https://hilmersonservices.com/ or feel free to contact the owner, Deb Hilmerson, at 952.239.0125 or email at [email protected]. A nationwide certified S/WBE Company.