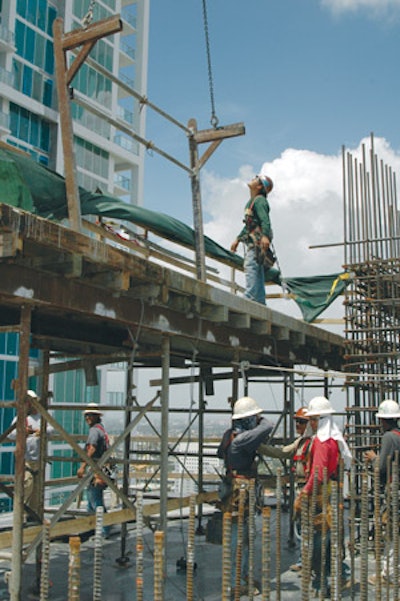
From the open-roofed 37th floor of an in-progress 67-story condominium project in downtown Miami, it's apparent why jobsite safety is so important - it's a long way down! This fast-paced work site has a lot going on - bustling workers, cranes lifting materials, formwork going up, concrete pouring down - but it's an efficient and organized work site with a noticeable safety-minded atmosphere. The stairwells and walking areas are free of unnecessary debris, handrails and guardrails help workers stay on their feet, workers at heights are wearing fall protection, everyone is wearing a hardhat, people are communicating with hand signals and safety supervisors are overseeing the project from several angles.
This atmosphere wasn't brought about simply by a set of safety rules mapped out in a three-ring binder sitting on a filing cabinet in the construction manager's office, but was created through several years of hard work after the ownership group at Form Works, Inc. of Fort Lauderdale, Fla., made a commitment to safety. Form Works president Don Marks recalls the company's previous attitude toward safety, "We always tried to get everyone to work safely, but we had the attitude that we were in a rough and dangerous business and had to accept the fact that accidents would happen and there wasn't much we could do about it."
Five years ago, the ownership group at Form Works decided they would do something about improving safety on their work sites and set out to create a sophisticated, company-wide safety program that involves participation from every employee through all levels of the company.
Taking safety to the next level
In 2003 Form Works hired its first director of safety and risk management to implement a company-wide safety program that was structured and accountable. The safety director appointed jobsite safety officers, whose sole responsibility is to oversee safety on each work site. Each jobsite safety officer works with a group of safety carpenters to install handrails and other safety features to create a safe working environment.
Form Works also adopted a drug-free workplace with in-house drug testing; increased use and enforcement of fall protection equipment in addition to gloves, glasses, and hardhats; and introduced safety awards and luncheons to recognize workers who excel at following safety procedures. The company also began to take a proactive approach to claims management when an accident did occur, reminding workers of follow-up doctor visits after an accident, investigating accidents to help prevent them in the future, and using the same law firm to manage all its cases.
A year and a half ago, Dave Iglesias came on board with Form Works as the new director of safety and risk management. Iglesias, with more than 20 years of experience in construction safety, built upon the safety program in place but applied his personal safety philosophy to take the program further. "All the things the former safety manager did I would have done, but my goal was to take it to the next level," Iglesias says. "Instead of us working safely, my philosophy was to push everyone to do safe work and for that ideal to become part of who we are."
Iglesias indoctrinated his safety philosophy into his field safety manager, John Van Riel, and his jobsite safety officers. Once Iglesias won them over, it was on to the employees. "If I can get all employees to do safe work, that's a lot of pressure off my jobsite safety staff," Iglesias explains.
Iglesias changed the safety culture among Form Works employees by showing them the company was serious about safety. New employees complete safety orientation, drug tests and equipment compliance tests to earn in-house training certification. "I need to establish the fact that people know how to do what they say they can do. And I don't mean just operate a piece of equipment; they need to know how to inspect it too, because that's part of safety requirements," Iglesias says.
Routine safety procedures include weekly safety meetings and special training topics specific to a certain site on an as-needed basis. Iglesias is bilingual, speaking fluent Spanish and English, so all safety training is offered in both languages.
Iglesias also enforces the utilization of high quality, effective safety equipment. Workers must have a double-legged lanyard and proper personal protection equipment. Employees are expected to wear their Form Works-issued safety equipment, purchased through Form Works at a deep bulk discount price. Iglesias says when employees pay for their own safety equipment they take better care of it. If an employee loses safety equipment, they're expected to replace it; if an employee brings in a worn out piece of safety equipment, Form Works replaces it.
Iglesias says the success of the safety program lies in its proactive approach to safety. "If there's a safety violation on the jobsite, instead of simply writing someone a violation slip we show them what they did wrong to help them avoid it in the future," he explains. There's also accountability in the program, and employees know Iglesias won't shy away from firing workers with a disregard for safety.
The safety changes implemented at Form Works resulted in a new safety culture throughout every level of the company. Jobsites are safer, and so are the workers. Form Works has seen considerable monetary value in the program also. "The safety changes haven't been cheap, but they have been worth it," Marks says. "Insurance costs have dropped a lot. Now we're eligible for insurance programs we weren't previously eligible for."
Marks adds the company's incurred losses have been cut to 25 percent of what they were before the emphasis on safety, helping Form Works drastically improve its experience modification rating (EMR). An average EMR is 1, with anything below 1 above average. In 2003, Form Works had an EMR of 1.8; today that number has dropped to 0.74.
An outstanding safety record has also proved a positive in winning job bids. "General contractors like subcontractors who do safe work," Marks says. "It puts a general contractor at ease to known we're going to take care of safety issues on the jobsite."
The ownership group at Form Works is pleased with the success of its safety initiative and will continue to drive their employees to do safe work. "I feel like we're in control of safety," Marks says. "There's no longer a feeling that we have to accept accidents, and beyond accidents, that control continues with handling any accidents that do happen instead of being at the hands of others. Now everyone knows that all work has to be performed safely, and that's not negotiable."
Finding its place in the industry
Form Works' leading roll in safety is just its most recent development in creating one of the leading commercial concrete construction companies in the country. When the ownership group bought out its previous owners and incorporated Form Works in 1988, they expanded its services from only formwork to offering customers a complete structural shell and everything in between, such as excavation for foundations, formwork, reinforcement labor and materials, concrete labor and materials, craning, and concrete pumping.
The expanded service offerings allowed Form Works to accomplish another goal of dramatically increasing its annual sales. By adding $3 million in sales a year for several years, it went from a company that never did more than $10 million in business to a $65 million per year outfit.
In-house business management processes, such as the addition of more project management personnel to track job records and help ensure on-time delivers for all product and materials needed, have allowed Form Works to become more efficient and profitable. One practice it has found beneficial is maintaining a slim equipment inventory. "We rent most things, so we don't own a lot of equipment. We don't want to worry about the upkeep," Marks explains. "It also gives us the flexibility to utilize the right piece of equipment on a job, instead of forcing the use of a piece of equipment we own that might not be appropriate."
Marks adds that advancements in the industry have helped Form Works become more productive on the job too. "Continuous advancement in forming systems has made our jobs easier. In general, we've seen better engineering in the products so less qualified labor is required to use them. One example is the addition of panelized slab systems," he says, "which offered a big boost in our productivity on certain jobs."
Despite the size and efficiencies in the company, Form Works still faces many of the challenges that companies of all sizes face across the country. "Getting good, qualified employees is tough. We try to find people who are willing to work hard and learn, and we can train them as we go," Marks explains.
On the immigration issue, Form Works finds itself in the same place as many other contractors. "To the best of our knowledge, we fill out proper documentation on employees, but we don't know if it's legitimate or not," Marks says. "If there was an enforcement crackdown, we have no idea how much of our workforce would be left."
Marks says his involvement with the American Society of Concrete Contractors (ASCC) and attendance at shows like the World of Concrete have given him insight into the concrete industry and new products that have helped him improve his business. He advises other contractors to stay on top of the national trends to help them expand and improve their businesses. "Contractors should be aware of what's available to them," he says. "Don't get locked into your environment, but look around to see what's out there."
Don Marks, president of ASCC Marks says the most important resource he's taken advantage of through ASCC has been his involvement with a MIX Group (Management Information eXchange), which connects six to eight contractors from different parts of the country who share in-depth business management ideas on a bi-annual basis. "We've meet for 12 years, and being able to share ideas with other companies and see how they do things is very helpful," he says. Marks adds that the ASCC's most recent membership benefit offers contractors easy access to expert opinions from contractors in all parts of the country. "With the E-mail Forum a member can e-mail a question into ASCC about some issue he's having and it gets blasted out to 120 members, people from all over the country who can respond to his request," Marks explains. For more information about ASCC, visit www.ascconline.org. |