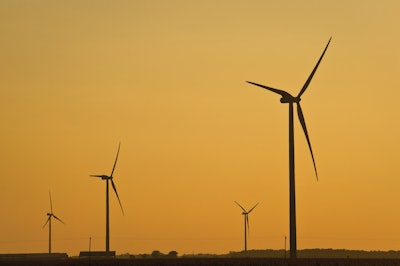
The Challenge:
Construct 15- to 20-foot-deep concrete foundations to support 152 wind turbines that are 328 feet high
The Players:
Lafarge North America
Iberdrola Renewables
Irving Concrete
The Process:
Cement supplied by Lafarge North America played a key role in the construction of the Blue Creek Wind Farm in Ohio, which is owned and operated by Iberdrola Renewables. One of the largest wind power plants in the world with 152 Gamesa G90 turbines, the facility has a generating capacity of 304 MW, providing enough clean energy to power 76,000 homes.
Lafarge provided Type I portland cement from its Paulding plant to Irving Concrete of Ohio, which built a strategically located portable ready-mix batch plant to produce approximately 122,500 cubic yards of concrete for the project. The construction of 15- to 20-foot-deep concrete foundations to support all of the 328-foot-high towers with 2-MW turbines required 30,000 tons of cement.
On average, each of these below-ground support systems used 60 truckloads of concrete (750 cubic yards), which was poured via a two-step process. A 2-foot-thick mud matte was poured first to create a solid base, and then an upper pedestal where the tower connects was poured in step two. The huge bolts that fasten to the tower were embedded into this upper section of the concrete. Quality testing was conducted at 7, 14, 21 and 28 days to ensure a solid cure.
Lafarge also supplied 20,000 tons of Type I cement for soil stabilization of approximately 44 miles of roads, which enabled access to the site under difficult soil conditions and provided a base for permanent roadways. Because the rural roads were not designed to handle the heavy construction traffic loads, they were ground down, mixed with 5 percent cement at a 12-inch treatment depth, and then allowed to harden before being surfaced with asphalt. This made for a stable base that was engineered to handle the heavy truckloads of concrete and other construction equipment needed to build the wind turbines. “The rebuilt roadways will require a lot less maintenance in the future due to their stronger and more durable base underneath,” said Tom Rapp, Major Market Manager at Lafarge.