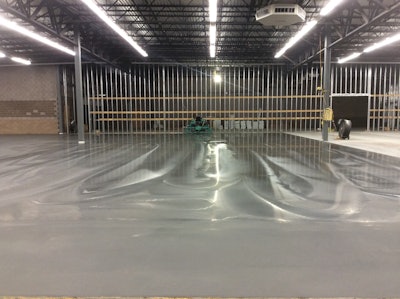
Paul Beagley started Phaze Concrete Incorporated, Hildale, Utah, in 2003 primarily to do large warehouse and “big box” floor work. Business went well and they branched out to include parking structures, specialty projects for the government, earth and utility work, and concrete polishing. They now have over 300 employees and are members of the American Concrete Institute (ACI) and the American Society of Concrete Contractors (ASCC). Over time he says his company encountered a couple verified cases of floor surfaces damaged by carbonation but there have been other projects where excessive carbonation was suspected. “The common thread in all these projects is that the work was completed during the winter months and unvented heaters were present,” he says. “In all cases the repairs were expensive.”
What is Carbonation?
The simplest answer is that carbonation results from the reaction between atmospheric carbon dioxide (CO2) with hydrating cement but not with carbon monoxide (CO). Normally the result of the reaction is a thin white film of calcium carbonate on concrete surfaces, also referred to as efflorescence. For instance, if you install a concrete driveway you first see the natural color of the concrete but after a day or so the surface begins to have a white cast. This is efflorescence, a harmless calcium carbonate coating that has little effect other than to change the surface color of the concrete—not to say this isn’t important, owners expect slabs to look aesthetically clean and free of white blemishes and sometimes raise payment issues. This can be serious when specifications call for colored concrete.
Deep carbonation, on the other hand can also cause concrete surfaces to be deeply weakened and this is what causes problems.
By the time fresh concrete is placed and finishing operations are started, the portland cement in the concrete is beginning to hydrate, producing calcium hydroxide (Ca(OH)2) as a byproduct. It dissolves in the mix water and is the principal chemical that gives concrete its high pH. When it comes into contact with atmospheric CO2 the resulting reaction yields calcium carbonate (CaCO3), the process referred to as carbonation. When there is a lot of CO2 present the production of calcium carbonate can become extreme, damaging the surface of a floor and requiring that drastic measures to be taken. The chemical reaction is as follows: Ca(OH)2 + CO2 ------> CaCO3 + H2O
Sodium hydroxide and potassium hydroxide are also present to a lesser degree in new concrete and produce sodium and potassium carbonation.
The Warehouse Environment
General contractors are usually the ones responsible for providing background conditions, including temporary heat for enclosed warehouse construction. When floors are being constructed during the winter months the usual ambient and base temperature requirement is a minimum of 55ºF. If a buildings permanent heating system is functioning it is used to provide the needed heat. But if it isn’t functioning yet temporary heating systems are brought in which are either vented or unvented. Vented systems expel exhaust gases (CO2 and CO) outside while unvented systems send exhaust gases along with the heat into the air inside the building. General contractors sometimes elect to rent unvented systems because heating with them is less expensive.
During the floor construction process openings for ready-mix trucks are constantly open and ready-mix trucks are passing in and out every few minutes. Their diesel exhaust gases put a combination of CO2, CO, soot into the air. In addition, exhaust gases from laser screeds, light towers, and finishing machines also go into the air. The current Occupational Safety and Health Administration (OSHA) requirement limits the permissible exposure limit (PEL) of CO in the air to 50 ppm (parts per million) or 0.05 percent over an eight hour time period. Because of the rule many contractors use CO detectors, or are required to use them, to monitor the air for the safety of their workers but they don’t monitor CO2 levels unless the owner requires, the typical regulation being a maximum of 4500 ppm.
There usually isn’t much air flow in warehouses either and CO2 is heavier than air so concentrations are highest at floor levels.
Why Floors Carbonate
As mentioned earlier, there is always a minor amount of carbonation occurring to the surface of concrete (as well as a little bit in the concrete). This is because some calcium hydroxide dissolved in water moves through the pore structure of the concrete to the surface and there is always CO2 in the air available to react with it. The current level in the air is approximately 400 parts per million (ppm) or 0.04% (this is about 40% more than at the start of the industrial revolution). Water is important to the process because both CO2 and calcium hydroxide are soluble in it and are carried by it, making freshly placed concrete the most vulnerable—rainfall on freshly finished concrete produces a lot of carbonation or efflorescence too because more water is available.
The flooring industry uses concrete mixes that are all portland cement—no supplementary cementitious materials—with water cement ratios of 0.5 or a little above. Finishers start the finishing process after the water on the surface of the struck-off concrete subsides, an environment that encourages the formation of carbonates.
Jose Pacheco, PhD, a concrete materials specialist at CTLGroup, Skokie, Illinois, says that carbonation tests performed in the laboratory are typically performed in controlled environments using 3- to 4% carbon dioxide levels in the air, translating to 30,000 to 40,000 ppm. “Depending on the cement being used, transport properties of the mixture, moisture conditions, and time of exposure, this can produce carbonation in mortar samples as deep as one inch,” he says. There is little information from the field about CO2 amounts at the surface of a floor when unvented heaters are being used but they may be approximately one percent, enough to do significant damage to a floor surface.
Factors that influence the amount of carbonation in floor surfaces include the following:
- The amount of CO2 produced by unvented construction heaters and diesel engines
- The type of cement being used
- The water/cement ratio of the concrete—as related to the transport properties of the concrete
- The amount of air flow or lack thereof in the building
- The surface finish—how porous it is
- The amount and density of cement paste on the surface
How to Reduce the Risk
The most important way to reduce your level of risk as a concrete contractor is to ensure that unvented construction heaters aren’t allowed on the jobsite. Most flooring contractors include this as an item in their pre-job/slab conferences today. Beagley says he hasn’t had a problem since he decided to specify the type of heater they want on the jobsite. Concrete contrators must explain the possibility of these issues and have a cost to remedy or exclude the cost to remedy from their contracts.
It’s not known at present how much CO2 is added to the warehouse environment by ready-mix trucks and other diesel engines. Many contractors have instruments that monitor CO for safety reasons but they don’t monitor CO2 levels. Using fans to move air can help reduce concentrations at floor levels. Moving exhaust out of the building is also helpful, a process that must be balanced with maintaining minimum temperatures in the building.
What to Do If There is Significant Carbonation
Unfortunately, contractors can find themselves having to remove and replace floors that have significant damage to the floor surface. Carbonation can turn cement paste to a powder and make a surface porous. Depths can be as little as 1/32nd to 1/8th of an inch with extreme depths being as much as ¼ of an inch in thickness.
In one case Beagley says the carbonation caused the surface to be porous but the depth was minimal and they were able to diamond polish the floor to the owners satisfaction. This was agreeable to the owner in this case but sometimes owners object. Issues such as who is at fault, who pays for the remedy and large aggregate exposure have to be resolved. Concrete contractors are almost always blamed for the problems and there can be a lot of expense involved.
It is important for you as a contractor to know if the problem you are experiencing is related to carbonation or excessive loss of moisture on the surface, as the two conditions can resemble each other. In the interest of learning from mistakes you should consider hiring a petrographer or concrete floor consultant experienced with these kinds of problems. Beagley said that he hired a petrographer for one of his jobsite failures and was told the problem was caused by carbonation. The owner hired a petrographer too and was told the problem wasn’t related to excessive carbonation. Beagley then hired a consultant to review both reports and it was determined to be a carbonation issue. But in another case he says that an assumed carbonation issue turned out to be excessive non-hydrated cement particles at the surface, attributed to no bleed water and a high rate of evaporation.