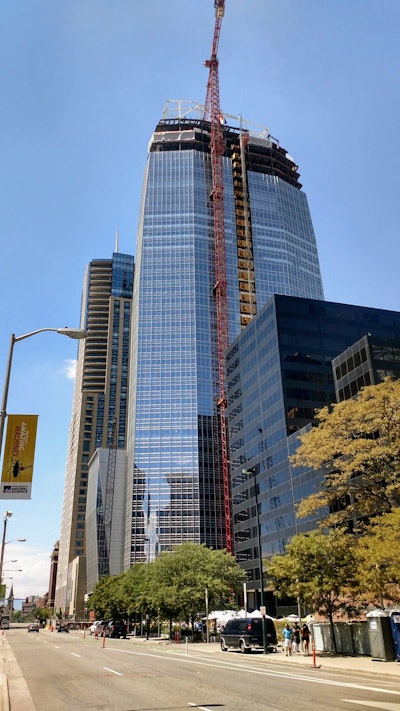
When Hines, a privately-owned global real estate investment, development and management firm, decided to construct the fourth tallest office building in Denver, engineering firms CTL/Thompson, Inc. and Martin/Martin, Inc. were called in to develop a foundation solution that would support this massive structure on the soft sedimentary bedrock. Denver-based CTL/Thompson, Inc. knows a thing or two about foundations. The engineering firm recently celebrated its 45th anniversary.
Hines proposed a 40-floor, 600-foot-high LEED Gold-certified office tower called 1144 Fifteenth, and CTL engineers Marc Cleveland, David Glater and Benny Lujan were charged with the task of helping to find a way to support the building foundation loads on the area’s sedimentary bedrock. The 1144 Fifteenth project would be the first Class A office tower building built in downtown Denver in more than 30 years.
Upon completion, it will be Denver’s fifth-highest building (fourth-tallest if you neglect the spire on top of the adjacent Four Seasons Hotel). It needed to rise above the rest – literally and figuratively – but there is a reason the buildings of Denver’s skyline are primarily low compared with other high-rises in the nation. The comparatively soft bedrock prevalent throughout Colorado’s Front Range cannot withstand the loads induced by very tall buildings, particularly with a dense office use, and soil and bedrock conditions can vary significantly within the foundation area.
The CTL solution
CTL recommended a drilled-pier foundation to safely support the building and the maximum load of 8 million pounds at each pier supporting the building core. The core also imposed extremely high lateral loads associated with a skyscraper, so CTL worked with fellow engineers at Martin/Martin Inc. and contractors to develop methods to preserve the condition of the bedrock for lateral support. The mat foundation or base of the core was heavily reinforced concrete, with a thickness of 7 feet, with proposed dimensions of about 120 feet by 60 feet, totaling about 1,900 cubic yards of concrete. The team designed a system using eight drilled piers, each 10 feet in diameter and bottomed more than 105 feet into bedrock – more than 140 feet below street level.
A creative design approach was implemented, allowing the concrete for the core to be in direct contact with the bedrock to provide increased lateral support. There is no technical term for this method. Essentially, the bedrock face being relied upon for additional lateral support was preserved by installing soldier piles and excavating with care before installing reinforced shotcrete. The core reinforcement was then installed, and the rest fell into place.
CTL engineers and local contractors had used a similar technique called “pre-splitting” once before – for the $300 million Hyatt Regency Denver at Colorado Convention Center hotel a few blocks away. The large concrete pours associated with the piers and core also required a special concrete mix to reduce the heat of hydration during the initial curing of the concrete.
Better option
“The team originally considered using 28 six-foot diameter piers drilled at a shallower depth,” notes Marc Cleveland CTL vice president, “but the contractor thought it would be a very tedious process. So, we opted to go with eight 10-foot diameter piers drilled 105 feet into the bedrock and below the tie beams we need to construct for the core foundation.”
Cleveland and his associate, Benny Lujan, project manager, also developed another design solution to save time and material in constructing the foundation base. Normally on this project a 150-foot long by 60-foot wide by 7-foot thick mat would have been poured over the eight piers. Instead, Martin/Martin designed two 120-foot long by 7-foot wide by 7-foot thick beams over the two rows of foundation piers, connected with perpendicular tie beams.
“Around the perimeter of the foundation structure we installed soldier piles into the bedrock to provide lateral shear strength for the foundation slab that would be poured directly on top of the bedrock,” Cleveland states. “Immediately after installing the soldier piles we sprayed the entire bedrock surface with shotcrete to prevent any moisture from evaporating.”
“The bedrock has a fair amount of moisture content, upper teens to mid 20s as a percentage, and if it’s exposed to the air and the content evaporates, the soft rock starts to disintegrate and begins to flake off,” Lujan notes. “So, using a shotcrete coating is the best way to retain the moisture content and preserve the overall structural integrity of the bedrock surface.
In general, the foundation solution CTL helped design was unique with the limited number of support piers constructed and the added lateral shear approach implemented. According to Cleveland, it’s the largest Denver building structure to date with most of the load being supported by only eight piers.
The concrete placement
Another extremely important construction challenge that had to be addressed had to do with the concrete mixture required for the amount placed for each support pier and the massive foundation beams. Each of the eight piers required 300 cubic yards of concrete, or 30 concrete mixer trucks lined up for the continuous placement that would take six hours apiece. With the amount of heat produced during the hydration process, it was important to keep the concrete as cool as possible to prevent cracking during the curing process.
“We came up with a mix design using 40 percent fly ash to reduce heat during hydration,” Cleveland explains. “The concrete producer, Martin Marietta, also used chilled water (35-40 degrees) at the batch plant to help minimize excess heating during hydration. By the time the concrete reached the project, it was in the 50 to 60-degree range and that really helped to slow the set time. The goal was to keep the concrete temperature in the 147 to 150-degree F range during the curing process. If it gets above 160 degrees, the concrete can overheat and crack.”
There were a few other site issues that had to be investigated, and in some cases addressed, like previous usages of the site. A number of past uses created geotechnical and environmental issues that needed mitigation. In the early 1900s, a nine-story bank occupied one corner of the site. When it was demolished, debris was left in the foundation area. The site also housed an old streetcar loop in the mid-1900s. Old maps show the layout of the past development coinciding with the debris fill found on the site.
As with other site and construction challenges, CTL/Thompson addressed each issue to keep the project moving forward. It was not always easy considering the tightness of the area, which required an innovative design because caissons couldn’t be drilled along a neighboring property boundary.
But with the structure topped off and all exterior glazing complete, interior work is expected to be completed by mid-2018. When tenants enter the shimmering new building for the first time they will marvel at its beautiful design and never know the details of the engineering solutions required to make it a reality.