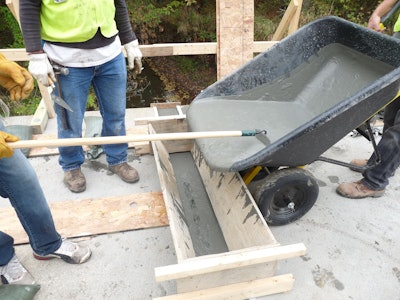
When normal ready-mix concrete is made the largest aggregates in the mix can range from 1-1/2 inches down to 3/8ths of an inch in size with compressive strengths that can be as high as 10,000 psi. Good mixes are “well graded” meaning the voids between the largest aggregates are filled with smaller aggregates and so on down the line until there is the least amount of void space possible. Ultra-High Performance Concrete (UHPC) is like that except that filling the voids between aggregates is referred to as “particle packing.” Sri Sritharan, the Wilkinson Chair of Interdisciplinary Engineering at Iowa State University’s Department of Civil, Construction, and Environmental Engineering, Ames, Iowa, adds that particle sizes for UHPC are kept very small to create a more dense matrix, the largest size not exceeding 600 microns (about the size if a grain of silica sand). This helps increase the standard compressive strength of these mixes in excess of 22,000 psi.
In the beginning it was called Reactive Powder Concrete (RPG) but that changed in the mid-nineties when it became known as UHPC. Research on this product originated in Denmark as far back as 1964 as a part of their effort to develop higher strength concrete mixes. Their research focused on very dense particle packed mixes with low water/cement ratios and in the 1970’s the development of superplasticizers (High Range Water Reducers of HRWR) further helped to achieve low water/cement ratios. Dominique Corvez, Vice President and head of Ductal North America for Lafarge, whose headquarters in the U.S. are in Chicago, Illinois, says they began to look at this technology in France too. Contractors experimented with it first but LaFarge, one of the world’s largest cement producers, developed an UHPC product they called “Ductal” and it is still in use today. In the beginning every batch was made from scratch but today there are several commercial producers of packaged dry mixes. LaFarge Holcim is one of the largest producers of this.
Advantages of UHPC
Compressive strength is the most recognized way to characterize UHPC. As previously stated, compressive strengths are expected to be in the 22,000 to 30,000 psi range to be considered UHPC but research studies of cured UHPC under high pressure and heat have produced compressive strengths as high as 116,000 psi to date. But there are other unique advantages too.
- High modulus of elasticity (MOE) which can be in the 7,500 ksi range
- High tensile strength compared to normal concrete
- UHPC has high bond strength to steel reinforcement and this can reduce the size of a concrete placement needed to bond concrete elements together
- It has excellent resistance to freeze-thaw cycling without the need for air entraining admixtures
- Structural elements can be smaller and more lightweight compared to those made with normal concrete
- Architects can design thinner concrete elements, improving the architectural appearance of their work
- It is a very dense material with capillary pores eliminated making it impervious to water and salt penetration without sealing the surface
- It has very low shrinkage and can be used as a non-shrink grout
- It faithfully transfers even the finest relief from molded surfaces resulting in more ideal architectural concrete pieces
Ingredients The goal for UHPC is to produce very dense impervious concrete by particle packing—arranging particle sizes in the mix so there is minimum void space between particles—in a very low w/c ratio environment. Similar to self-consolidating concrete (SCC), UHPC flowability is measured in “spread” rather than inches of slump. Spread diameters of 12-20 inches are common, making it easy to place and consolidate, resulting in very high strength and good resistance to environmental damage.
There are many different mix designs for UHPC but they will use some or all of the ingredients below:
- Cement. Portland cement with a little longer hydration process is preferred
- Ground Limestone. Used as a fine aggregate
- Sand. The largest size aggregate in the mix.
- Quartz powder. Very finely ground silica which is used to provide vital particle sizes
- Fly Ash. A supplementary cementitious material (SEM) that also helps with the particle packing process
- Silica Fume. A SEM with particle sizes as little as 1 micron to help densify the mix.
- Admixtures. Polycarboxylate superplasticizers (High Range Water Reducers) which are used to assist in the mixing and placing process and making very low w/c ratios possible
- Fibers. A range of fibers are being used in UHPC mixes. They include; steel, glass fiber, Poly Vinyl Acetate (PVA), polypropylene, and others. The amount of each depends on the material used but steel fibers are typically dosed 2% to 3% by volume of the mixture. This corresponds to 0.5 to 0.8 cubic feet of fiber and the fibers are very thin, usually 0.2 millimeters in diameter.
- Water. The low amount of water, approximately a 0.2 water/cement ratio, reduces shrinkage and increases the strength of the concrete
Mixing UHPC
Due to the fineness of the materials and the very low w/c ratio mixing UHPC mixes requires special equipment. Sritharan says most UHPC is mixed on construction sites with high-shear pan mixers but he says he has been on sites where special ready-mix trucks were used. Mixing UHPC from scratch requires an involved blending process to properly distribute all the fine powder materials together. As a result, most UHPC construction applications today use pre-bagged products. For this and other reasons less than 1-1/2 cubic yards is typically mixed at one time.
Heat curing
Sritharan says that subjecting UHPC to steam curing with temperatures in the 194ºF range develops high early strength. Steam curing for 48 hours enables UHPC to attain its full strength quickly and when high pressure is introduced with elevated steam temperatures it’s possible to greatly increase strength even more.
Construction site applications
UHPC is costly to make—much higher than standard concrete mixes and perhaps this is the reason its acceptance has been slow. But when all the benefits are considered it can be cost effective. In the U.S. infra-structure and bridge construction is currently the biggest UHPC user, mostly for connecting precast bridge elements together. It is usual to provide 18 inch reinforcing bar overlaps for proper anchorage but UHPC installations require only 9 inches due to its superior bond strength. As a result concrete yardage for these junction spaces is much less and there is greater resistance to ambient conditions.
Sritharan says the Iowa Department of Transportation is also researching the use of UHPC as an overlay material for bridge decks. A 1 to 1-1/2 inch thick overlay can supply ultimate protection for bridge decks, as they aren’t affected by salt, other deicing compounds or freeze-thaw cycles.
Thin Architectural UHPC Composite Panels
Kevin Gannon, RA, the Director of Program Development for Taktl LLC located in Turtle Creek, Pennsylvania, says one of their biggest problems is differentiating Architectural UHPC (A|UHPC) from civil engineered ready mix products and also Taktl products from Spray-in GFRC or extruded GFRC products. A|UHPC uses only non-metallic reinforcing fibers and often includes continuous mesh. Because of the thinness of UHPC panels, the mix design, and manufacturing methods favor flexural strength over compressive strength, while retaining all of the durability factors expected with UHPC. With the greatest resource for UHPC material reference standards being the Federal Highway Administration, architects are bound to have specification challenges. Taktl has made great strides with regard to establishing the reference standards and criteria for architectural UHPC facade applications. They focus their technical sales and project management resources on educating designers and supporting contractors.. “Once they use the product they readily specify it on other projects,” he adds.
Taktl originally focused on complex injected molded UHPC castings says Jason Flannery, the companies Design Director. It was an outgrowth of their metal outdoor fixture and furnishing business. They began to look at concrete because of how it could be shaped for facades. He says they began manufacturing UHPC facade panels in 2010, something no one else was doing in the US. They spent three years doing research and developing equipment. “We decided early on to develop the new company vertically—do every phase of the work in house from mold development and construction to innovating a continuous semi-automatic casting process,” he says. Today their only business is UHPC architectural concrete and they have a 200,000 square feet under roof with 150 employees. Last year they produced 1.5 million square feet of façade cladding, including hospitals, museums, university building and mixed use high-rise buildings – either field set in rainscreen cladding assemblies, or integrated into unitized façade systems.
Dr. George Quercia, Taktl’s Director of Research says they produce UHPC curtain wall panels which are only 5/8 inches thick. Within this thickness are two layers of mesh as well as glass fiber reinforcement. Typical panel sizes are 4 x 10 feet but they can cast up to 5 x 12 sizes and instead of forming each panel they cast oversize and trim them to size with concrete saws. These panels can replace 6-inch thick normal concrete curtain wall precast panels. The thin panels reduce transportation costs significantly and economically extend the distance to construction projects.
There is another advantage to architectural casting with UHPC—finely detailed mold surfaces are faithfully transferred to the casting due to the very small aggregates and paste structure of the mix. This makes it possible to create ever more detailed mold surfaces to achieve more stunning looks.
The value of UHPC
Though it is considered a new kind of concrete and doesn’t have much name recognition, UHPC has many advantages. Its great strength means that less material is needed to accomplish what regular concrete does. This can translate to engineering lighter structures starting with their footings. Water and ambient conditions that shorten the life of other types of concrete have little effect on UHPC because of its impermeable nature, providing a much longer pristine lifespan. Sticker shock might cause you not to give it a second thought but that would be a mistake. When everything is taken into account, strategic use of UHPC could turn out to be a bargain.