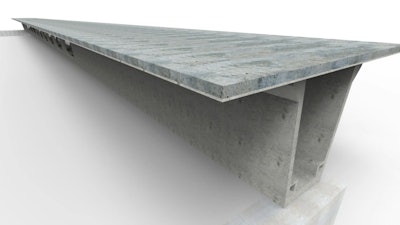
On July 15, 2021, AEEE Capital Holding & Advisory Group (AEEE) announced the completion of a peer review of a new sustainable ultra-high performance concrete mix named EASSCM (EA Super Strength Concrete Mix - AEEE's own UHPC mix). Led by Dr. Maher Tadros, the review confirmed the performance and value as related to the longevity and the sustainable attributes in the concrete.
But before getting into the impressive performance specs, the key difference between the concrete we are mainly familiar with and what has become known as ultra-high-performance concrete (UHPC) is the reinforcement. Where it's common to use a steel or fiberglass bar, UHPC would instead include very fine microfibers into the mix - which should be dispersed throughout the entire volume of the concrete in an integrated chaotic or random pattern. These fibers can be made of metallic or nonmetallic materials, but, explains Tadros, "for structural concrete, steel fibers offer better performance."
Dr. Tadros (ret.), founder of e.construct.US LLCe.construct.US
As a retired professor, Dr. Tadros founded e.construct.US LLC, a structural design firm that focuses in precast and prestressed concrete. Made up of a high number of PhDs on staff, the consulting firm specializes in high-end design. "The design that probably other companies would shy away from because of difficulty and liability," he says.
With over 25 patents, including the THiN-Wall insulated wall panel system, Dr. Tadros was instrumental in the development of the NU I-Girder - a system allowing bridges to have longer spans and shallower depths. This background and his expertise were key to assessing the commercial viability and technical application of AEEE's EASSCM-UHPC (the mix and its proprietary bridge designs).
"Cement is one of the most consumed products on the planet. It represents 8% of the world's annual carbon emissions," says MJ Said, Chief Executive Officer, owner, and founder of AEEE. "We're gratified that Dr. Tadros' peer review not only confirms the unparalleled performance and long-term value of AEEE's concrete mix, but also that its sustainable attributes could help the industry reduce the carbon footprint of cement by 16% by 2030 under Paris Accord commitments. The structural life expectancy of bridges built with this new material could exceed 300 years with virtually no maintenance, which is over four times the 75-year design life of the bridges currently built."
"We not only have a better mix, but we also have a lower cost mix, " says Tadros.
AEEE is an International Construction Management, Mixed-Use Development and Holding firm. AEEE's principals have built and/or advised on over 8.3 million sq. ft. of landmark commercial, residential, infrastructure projects globally. In addition to its portfolio of sustainable construction technologies, the company provides a range of services to its real estate development clients, including pro-forma analysis, pre-construction, construction management, fee-development, and post-completion operations support.
According to Dr. Tadros' peer review, AEEE's proprietary technology could have a disruptive impact on building and infrastructure construction as the Biden administration finalizes its trillion-dollar federal infrastructure bill targeting over 10,000 U.S. bridges. The peer-review overview by e.construct lists possible applications for the EASSCM UHPC mix such as tunnels, explosive restraint structures, wall panels, prestress elements, buildings (mid-and hi-rise), marine/sea walls, decking, storage tanks, and parking garages.
The announcement lists the following benefits:
- An increase in compressive strength to 48,500 PSI (However, such a strength will likely be not needed for the great majority of structures. Dr. Tadros' report shows a more realistic figure of 25,000 PSI.)
- An increase of flexural strength to 3,500 PSI, which is 50% stronger than the current market-leading concrete mixes (Increased PSI here would require the increase of fiber content, which would significantly increase the cost.)
- The mix produces a lifespan of over 300 years for bridges vs. the current ~75 years, according to e.construct
- The mix results (in combination with unique structural design) in potential savings of up to 47% in total project costs with expedited timetables for construction projects of up to 33%; and
- AEEE's precast concrete bridge girder system utilizing the AEEE mix results in 50% weight reduction and in the virtual elimination of steel rebar. The intrusive impact on the environment is lessened by the sharply reduced need for total cement and steel usage and reduced fossil-fuel energy consumption. Offered Proprietary Long Span Bridge Beams/Girders have 20 to 50% longer spans and are more efficient than any other existing concrete beam/girder technology at this time.
Q. How can the EASSCM mix be disruptive to the building and infrastructure construction industry?
AEEE Capital Holding & Advisory Group, e.construct.US
You don't need to do any of that. And the beam is half the weight. So in transportation, it's less costly, not just environmental impacts.
There are two aspects, there's the design aspect. You could have a design, but...you have to have constructability on to a design. That makes sense. When we talk to precast companies...we say, "look, you know, this works, because, from a constructability standpoint, it also makes sense, and here's why." Constructability is important.
On the other hand, when you have materials being sold for $2,500 per cubic yard for a while, and then 20 years later competitors coming in at $850 a yard, things are changing. We know that with our proprietary direction and the assistance of e.construct in helping us get there. We know that we can be significantly less than even that.
Just bagging this up in bags, and telling people, "You can have your own design, do your own thing." However, the ultimate thing is the combination of the material and the design together...you can have it broken out, you're saving money and on both ends.
Tadros: Let me try to simplify this for you. You have a bridge in a major city, an interchange that crosses from side to side 250 ft. And you want to build it with the least interruption of traffic, least inconvenience to the traveling public. And least disruption to the businesses around it. This material and system, because of the strength of the material, will allow you to make pieces that run the full length, the full 250 ft. in one piece. And you set it on the permanent supports. And if the bridge takes four of these pieces, or five of these pieces, because they are low volume, lightweight, because you're not using as much material due to optimization. And you set these four or five pieces overnight, when everybody is sleeping, and then you open to traffic the next day, that's much better than building this bridge for six months or one year using small pieces. And you get rid of the center support—in the center median—by having a full 250-ft. long piece instead of two spans of 125 ft. each with a pier in the middle.
So there are a lot more benefits than just using a smaller quantity that's better for the environment. There are significant benefits and the actual speed of construction and the inconvenience to the traveling public. In the end, you have this material that is virtually indestructible. It can last hundreds of years and that some studies in Australia recommended that one version of the UHPC would have a life expectancy of 340 years.
And that's compared to what we design in our codes in the US, we design for a life expectancy of 75 years. So compare 75 years with 340 years, you'll see that this material would not require much maintenance. You're not going to have holes in it. And you're not going to go patch it. You're not going to get the corrosion and all of the annoying maintenance issues that go with conventional concrete.
Q. What are some of the real-life use cases?
Side: We commissioned Dr. Tadros' firm to look at what we had initially worked on. We wanted input and adjustment as necessary for the North American market...and that's where he came in, that's where e.construct came in and assisted us. And they're the best of the best. And when really, at the end of the day, the mix is one thing. But you if you don't accompany it with your own innovative design, how to implement the mix, then, you're missing out, I guess, right. So, the innovative part of this whole IP or product is not just we have a mix, but we have several designs that we're implementing that makes it a very fruitful endeavor.
The 49,000 is not something that you will try to do every day. It's the capability of the mix to achieve 49,000 sometimes even higher. You will not want to use a mix for 49,000 unless you have to.
—Dr. Maher Tadros, e.construct US LLC
When you use UHPC: it's half the weight, it's the slimmer members, steel rebar is pretty much close to eliminated.
Tadros: I think what MJ said is extremely important very critical because UHPC in various shapes and forms has been tried in this country in the U.S. since the mid -1990s, for the last 25 years. And not much progress has been made for a number of reasons, with the formula that MJ is talking about your treat the whole system, not just a concrete mix, but actually the products that this mix is used in and how to optimize that system.
That was the missing component in the work that has been done here in the US in the past 25 years - one of the missing components, one major missing component. And the other one is it has to do with the mix itself. So you can't really get the total picture unless you talk about a structural system, a bridge, a building something of that nature.
Generally speaking, these mixes are not easy to implement in real life. They are very intricate. And you're converting concrete to a very highly scientific material. Everything has to have very high-quality control to be done correctly and that takes experience and training. But the properties that come out of it are just incredible, extremely high compared to what you see in regular concrete.
Q. Can you expand on the compressive and flexural strength performances?
Tadros: The 49,000 is not something that you will try to do every day. It's the capability of the mix to achieve 49,000 sometimes even higher. You will not want to use a mix for 49,000 unless you have to. Unless you have a reason to use that strength. So, in most practical applications, we will scale down that mix to a strength of 15,000 to 18,000 lbs./sq. in. in compressive strength. That is still about four or five times what you see in regular concrete.
But we have to balance everything. We need to know what we're designing, what the product that we're designing is, and what the demands for that product are before we tweak the mix, to give us the proper properties of the proper strength. It's no sense wasting money on strength you don't need and its compressive strength is probably not that important compared to tensile strength. That's where the fibers play a role and that's where we get rid of the rebar and a lot of the accessories.
This material has a superior tensile strength to anything else that has existed on the market because of the quality and amount of fibers that are used. And there are certain minimum ASTM (American Society for Testing Materials) standards, that we meet with this mix. That tensile strength is a minimum of 2,000 lbs./sq. in. At an absolute minimum, when you do the ASTM testing, most of the time, we were getting 3,000 to 4,000 lbs./sq. in.
Q. Is there a cure time?
Tadros: It all depends on the product you're designing—the bridge, the building, etc. There is a very specific curing method that is used with UHPC that we could invoke if we need to, but again, it costs money. The job is to try to minimize the total cost while still having the superior properties that UHPC gives.
So, what's called post-cure thermal treatment (PCTT) is a method we've been using with UHPC in which we subject the product—the beam, the bridge beam, the building member—to very high temperature, 194º F for 48 hours, under very high moisture and so cook it for that two days. But we don't have to do that and we have not had a need to do that unless it's a very specialized design.
Use the contact us page at the AEEE Capital website for more information on the EASSCM mix, aeeecapitalgroup.com.