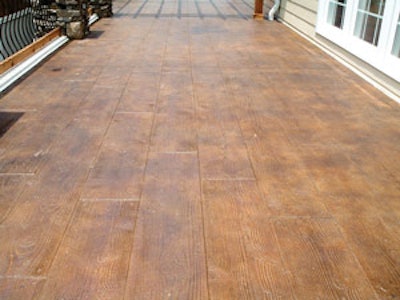
Decorative concrete can be an unpredictable animal at times. We find our problem phone calls from contractors increase when the temperatures rise during the heat of the summer and fall in the winter months. The bottom line is, whether you are working with two-component resins, cement-based skim coats or ready-mixed concrete, these materials set much quicker in warmer temperatures and much slower in cooler temperatures.
Recently we poured a 5-yard panel of stamped concrete (which is not a lot for a supposed pro), not taking into account we were using a mix design that we typically use during the winter months or when temperatures are under 80 degrees. This mix has a higher cement content which gives the concrete a needed boost for quicker setting times in the cool season. On our pour we started placing the concrete with no apparent problems other than our sweat burning our eyes on this 97-degree day.
A couple applications of color hardener later and some very fast finishing, we found ourselves removing the last stamping mat from the slab just one hour and fifteen minutes from the time we started placing the concrete. Shame on me for not taking the extreme conditions into account and compensating for the heat! I'm happy to report our test panel came out great thanks to some lightning fast finishing. You can bet some modifications were made to our next mix in addition to step retarding with Fritz-Pak's Mini Delay Set, allowing us much more time in those extreme conditions.
It is scenarios like this where a professional needs to tap into all of his or her past experiences and training in order to overcome jobsite adversities. A contractor can invest in training along with countless hours of practice and just when you think you have mastered certain techniques, wham, something comes up on an actual project that knocks you down, making you feel worn out, dejected and questioning your ability as a craftsman. I can certainly sympathize with you - I've had a number of my own gut wrenching sleepless nights lying in the bed wondering, "What the hell just happened and how could this catastrophe have been prevented?!" The reality of this fickle industry boils down to this - sometimes disaster is unavoidable and your company has to either fix or re-do the work at your expense.
This was the case with Cody Dawkins of Create-A-Crete, an aggressive, young, up-and-coming contractor in the greater Atlanta area who believes in training and doing things the right way. Despite Dawkins' impressive portfolio of successful applications, he had one of these nightmare projects. After a sleepless night, he decided to call me for some advice.
A tale of two pours
Dawkins' project consisted of pouring stamped and colored concrete on an elevated, corrugated metal pan deck, which is kind of scary even in perfect conditions. His first pour went down "flawlessly," as he put it. The concrete was placed around mid-morning with temperatures in the range of 75 to 80 degrees and stamped roughly two and a half hours later with a perfectly consistent imprint. It was the second load of concrete that took the wind out of Dawkins' sails and in the end cost his company labor and additional products. It also left him wondering what had just happened and how the project could have taken so dramatic a turn in only three hours.
With temperatures exceeding 90 degrees by the time the second load was delivered, Dawkins thought it would be a good idea to add a small dose of retarder from the batch plant to extend the setting time of his second load. Because of the size of the area the crew needed to cover, they added additional retarder on the jobsite to prevent the concrete from setting up too quickly. As soon as he and his crew started placing the second batch, someone noted that the concrete seemed "sticky" and "hard to finish."
Concrete that exhibits qualities like those that Dawkins described is common when the air content is too high, when water reducers were used or a combination of the two. Also, depending on the type of retarder the ready mix producer used (Hc type or lignin based), it could have entrained an additional 2 to 3 percent air. Whatever the issue, it lead to a batch of concrete that set from the top down instead of from the bottom up, resulting in a crusted surface.
Since the first load of concrete went down with relative ease, Dawkins thinks his ready-mix producer sent him the wrong mix or overdosed the admixtures the second time around. Of course the ready-mix producer's response to this was that Dawkins did something wrong, and the salesman even told him he probably got on the concrete too late. The ironic thing was the texture was uniform and the lines were true and straight, which was not the problem.
When Dawkins and his crew arrived the next day to remove the release from the previous day's stamping they noticed a crunching sound as they walked across the surface, almost like they were walking across fresh snow in snowshoes. Much to his amazement, upon cleaning Dawkins found the whole surface had spider cracked, sometimes referred to as random map cracking. After discussing possible remedial alternatives, he decided to scarify the entire surface of the second load then use a stampable overlay to match the first load. This proved to be challenging considering all of the area drains in this deck.
Once Dawkins and his crew successfully applied and stamped the overlay, the next challenge was to color match the two panels. Acid staining ready-mixed concrete compared to stamped overlay would have produced dramatically different results making it difficult to blend the two panels. For this reason he chose water-based stain with sealer over the top.
I have to tell you, he pulled this one off beautifully. I commend Dawkins and his crew for going the extra mile to make it right for the customer despite who was right or wrong. He reports that his customer respected his honesty in the matter and loved his new deck and would highly recommend Create-A-Crete because of its professionalism.
Situations like this can make or break a small company. It's important to consider jobsite conditions before sailing into a decorative concrete project. You might even want to consider holding off on a project until conditions are a bit more forgiving. If you're in doubt, don't do it; and under no circumstance should you try a new product or technique on the actual job without previous testing. Don't be afraid to be up front with your client even if it means holding off on the schedule. And who knows, you may be able to avoid your own ship from sinking and peacefully enjoy a good night's sleep.
Bob Harris is the founder and president of the Decorative Concrete Institute, Temple, Ga., which provides hands-on training in architectural concrete. He has personally placed or supervised the placement of more than 3 million square feet of decorative concrete and is the author of a best-selling series of decorative concrete books and DVDs. For more information, call (877) DCI-8080 or visit www.decorativeconcreteinstitute.com.