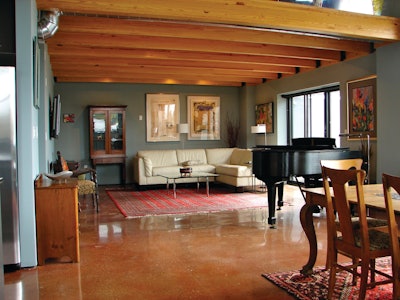
The Blue Line Station project represents a recent transformation of a historic building into a mixed-use development in Champaign, Ill. These beautiful, modern apartments and downstairs retail space have come a long way from their original state. Now a Historic Landmark building, the structure that houses Blue Line station was first built more than 100 years ago as the Hickory Street Trolley Barn, housing trolley cars that transported people throughout central Illinois and to and from St. Louis, Mo.
Since then the building experienced two additions and housed an electrical company and a publishing company before its most recent conversion into a mixed-use facility with nine loft apartments and three retail spaces. Needless to say, the 85-year-old, unfinished concrete floors were less than desirable to look at. The architect of Blue Line saw past their worn down surface and hired our company to create a flooring finish that fits the modern design but still retains the historic feel of the building.
Fixing someone else’s mistakes
The scope of our work started in the upstairs residential space. Our company overcame several hurdles with the floors in the loft apartments. To start with, another contractor performed a polishing process in the apartments but left the floors in sad shape with scratches throughout. We had to completely regrind the entire surface before we could reapply dye and repolish the floors to get them to look as they do now. This was a difficult task due to the magnitude of the scratches.
We originally wanted to do as little rework as possible and avoid removing the first contractor’s dye job. We took a section of the floor as a sample area to determine the necessary process to achieve the customer’s expectation as well as our own. We began with 400 grit resins, then backed down to 200 grit, all the while just exposing more of the scratches the previous contractor had covered up with sealer/densifier. We continued backing down through 100 grit resins, 50 grit resins, 150 metal bond abrasives, and 80 grit metals — all the while unable to remove the existing scratches. We finally recut the entire floor with 30 grit metal bond diamond tools. At this point 90 percent of the previous maroon dye was lost.
We met with the owner and suggested terra cotta as a new shade that would complement the finishings and existing décor for the upstairs apartments. Then we took the floors up through our own polishing processes to a 1,500-grit finish, applying dye after the 200 and 400 grit steps. Once we were happy with the consistency of the color we applied a penetrating densifier and finished the surface with a topical stain protecting sealer.
One other major hurdle with this phase of the project was an issue with the drywall. It had a shadow edge (1/2-inch overhang, ½-inch above the floor), therefore there was no base trim. This made edging a difficult and tedious task. Because the previous contractor used up the majority of the flooring schedule allotted to the project, we had to work swiftly and efficiently to get the floors to the stage they are now.
Upon seeing the final outcome of the residential space floors, the business occupying the ground level front area of the building wanted the same look for its floors. This phase of the project — 11,560 square feet in a marketing studio — was accomplished by full grinding/polishing the surface of the original concrete. The polish and black dye application process we performed on this floor gave an old, drab, dull space a modern feel. And the project won our company a second place award in the “Polished, Over 5,000 SF” category of the American Society of Concrete Contractors 2013 Decorative Concrete Awards.
Neil Roach is CEO and President of Creative Construction By Design and Surface Tech, Inc. The Danville, Ill., company offers polished concrete, pervious concrete and decorative concrete services for residential, commercial and industrial clients. Find them online at www.creativecons.net.