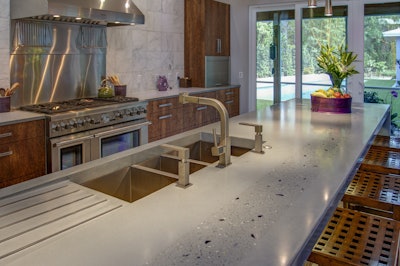
Over the years, decorative concrete has taken on a large advancement and progression in style, strength, and function. In the early days concrete countertop mix designs were limited, styles were basic, however very beautiful in their simplicity. The production time of early concrete countertop fabrication used to be a fairly lengthy process. The average shop used a high-strength traditional concrete mix with low shrinkage characteristics. After the item was cast it had to cure for an extended amount of time to build enough strength for the installer to be able to move on with the next step in the process. This next step would usually be honing, polishing or sealing the piece to bring on the final luster, stain resistance, or appearance desired. In the early days with traditional methods the production delay between steps could have been up to two weeks.
With the introduction of GFRC mix designs, production time and application techniques have advanced considerably. Modern forming methods allow for a host of new design options. The main reasons for popularity with this method are due to the quick turnover in production and virtually unlimited design options. A specialty shop who is familiar with this GFRC process and technique can produce countertops, furniture, mantel pieces, fireplace surrounds, shower panels and just about any type of unique design element. The GFRC process has taken a place in the outdoor market today as well. You will see exterior wall panels, waterfalls and rock features made with this versatile process.
What is GFRC?
GFRC actually stands for Glass Fiber Reinforced Concrete. The traditional GFRC process consists of a very high-strength, low shrink mix design, utilizing a polymer modifier and alkali resistant glass fiber strands. The traditional installation requires a spray on “Face Coat” and also a “Backer Coat.” Many companies utilize the same mix design for both the face and the backer coats, however with the backer coat the glass fiber is added into the mix then applied either by hand packing or spraying (with a specialized gun) over the partially set face coat. The backer coat is consolidated after application. Once cured the piece is then demolded and moved into the next stage of processing. The GFRC process is for precast operations only so you will be building forms before casting the piece.
Forming Techniques
Forming techniques will dictate the final look and style obtained by GFRC. This is mainly due to the mix’s ability to pick up extreme detail. The form for a GFRC project can be smooth as glass, bring on textures to simulate the look of rock or wood and can also pick up the detail of a hand carved piece of art. Custom edge work can be created in countertops by building the form out of traditional Melamine and then utilizing sculpturing clay to create a unique detail to the piece. The clay may be utilized to create simple custom detail edging, possibly to create a sink basin with a unique shape or to create a unique one of a kind edge for the project. These custom edges can be created very quickly with this process and your possibilities are endless.
Mix Design
The mix design for GFRC varies amongst the professionals who manufacture these products. Most formulations start with a fairly simple mix design utilizing equal ratios of Portland cement to finely graded crushed quartz. CSA cement is added to speed set and overall curing time. This high-strength mix is further boosted in strength with the edition of a very fine pozzalon called silica fume. The water to cement ratio is regulated and kept to a minimum with the use of a very high range super plasticizer. The final admixture needed in this formula is an acrylic polymer. Reinforcement is developed through combination of this specialized mixed design and the use of a three-quarter inch (¾”) alkali resistant glass fiber. Please keep in mind an important aspect of the glass fiber edition, that this is generally not added until after the cementitious portion is mixed thoroughly. This is done to reduce the breaking down of the glass fibers into smaller pieces during the mixing process. The specialized admixtures needed for GFRC like the super plasticizer and acrylic polymers are available in both liquid and dry versions.
Application Technique
The application technique is fairly straightforward and also fairly simple. The true magic to the GFRC process actually happens with the forming technique. Forms can be made from a multitude of mediums. The flowing sink designs you see today are actually formed from a combination of traditional Melamine lumber, the use of fabric and even gum rubber sheeting is utilized to create these endless flowing designs. Once the form is built to accommodate the shape of the special requirement. First a very light low build type form oil or wax is utilized, if a thick oil is utilized the GFRC mix will pick up the build of the oil in the finished piece.
Once excess oil is removed from the form, the face coat is mixed. The face coat is generally applied to the form utilizing a Hopper gun powered by compressed air. The degree of initial set is monitored and at the optimal time the backer coat is mixed, fiber is then added into the final stage of the mix. At this point you’ll be working with the mix that closely resembles a cementitious fiberglass mix. The backer coat is then either sprayed onto the face coat utilizing a special spray gun or it is hand packed into position. Once the backer mix is in place, it is consolidated utilizing a small handheld roller design for this task.
This process allows flawless pieces to be constructed in a very short time period compared to the traditional concrete casting process we all knew years ago. Any desired look or color can be incorporated into this modern concrete construction technique.
Endless Design
Once you understand and master the GFRC process you will find an unlimited creative outlet. Your work can bring on the look and detail of a super clean pinhole free fireplace surround or the rustic detail of freshly sawn wood. Design elements can be cast directly into the piece to bring on the realistic interpretation of a water warn fissure or void while not sacrificing strength. Specialized minerals are also available to incorporate into the mix to bring a nice luminescence luster to the finished piece. This can be a very unique and intriguing look you’ll see into the future with GFRC panels.
Ed. Note: Bart Sacco is President of Kingdom Products, www.kingdom-products.com.