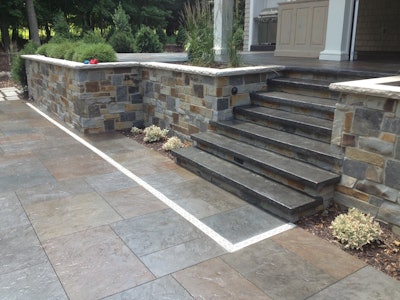
If you haven’t noticed, concrete has become more fashionable in mainstream design. Although the use of colored concrete isn’t anything new or groundbreaking, the interest in concrete as a finished, functional surface has found its way into everything from modern furniture to commercial floors. The boundaries of texture, form and color continue to push the material into new applications.
When it comes to staining concrete, its vital to take a step back and ask yourself what both you and your client expects from the coloring process you plan to use. It’s important to underscore that in general, stains and dyes are not going to provide an opaque, solid color, but rather a variegated representation of color that shows off the character of the concrete surface it is being applied to.
Generally, there are three different types of concrete stains:
- Reactive stains
- Water based stains
- Penetrating Dyes
Reactive Stains
I’ve often referred to acid stains as the Ferrari of concrete finishes…beautiful, dynamic and important to maintain! This material changes the color of the concrete surface through a chemical reaction between the calcium hydroxide in the concrete and metallic salts in the stain, which are typically carried in a hydrochloric acid. This reaction creates a beautiful patina, with highs and lows of color that reflect the variations of the concrete surface. The range of colors is limited to earth tones and can be used on a variety of concrete surfaces. Important considerations for a successful finished product include:
- The concrete is fully cured
- The surface is clean, and does not have any undesired variations from the curing process
- The stain is applied in a way that does not leave application marks…spraying acid stain is preferred over rolling or applying with a brush.
- Residue is completely removed after the stain has reacted and dried, and the surface is neutralized prior to sealing
What you see is not what you get…the reaction process of this material will not reveal the actual color of the final product until the stain has completely reacted, and the surface is cleaned and sealed.
The best type of sealer is applied. For interior floors, multi component epoxies and urethanes are preferred, while outdoor applications are best sealed with solvent based acrylic sealers. Making sure that the sealer applied is properly maintained will ensure that the installation provides years of service.
Water Based Stains
For a slightly less challenging installation process with a wider range of color choices, water- based stains are a great choice. This material combines pigments carried in a suspension of water and polymers to drive color into the surface of the concrete. This material is translucent, however will become more- opaque with multiple coats…a balancing act between achieving the intensity of desired color while maintaining an unpainted look. As with reactive stains, surface prep and site conditions of the concrete are important as well as the following:
This stain can be diluted and also combined with other colors to create a wide spectrum of colors and intensities of color .
- Application method is more forgiving…you will see the color in real time unlike the reactive stains.
- No clean up or surface neutralizing is required after applying the water- based stain.
- Layering of colors and creating more unique effects become a function of the application method, not the material.
- Over-applying water- based stains can cause a build up of solids on the surface of the concrete, which will be unstable and prone to wearing.
Just like reactive stains, apply the best sealer system for the application to keep the surface of the concrete from wearing.
Penetrating Dyes
Typically used for interior floors, these dyes create intense, bright colors and are either carried in an Acetone or water solution. Traditionally used as a part of polished concrete floor, these colors are typically not UV stable and are used for indoor applications. Specific benefits of this method of coloring:
- Intense, bright and translucent colors
- Rapid surface penetration and drying make them ideal for stenciling and detailed artwork in slabs.
- Much like water based stains, these colors can be diluted and combined to create multiple shades and tones beyond the standard color offerings.
- Generally, concrete dyes are used in-line as a part of a floor polishing system, where the color is introduced in-between steps in the grinding/polishing process.
- For non-polished applications, the material is locked in with an epoxy/urethane system.
Different substrates, different effects.
Its important to remember that each of these topical stains will look and behave differently on each substrate you consider applying them to. When you consider the following surfaces, keep in mind these products will have a unique personality on each:
- Micro toppings
- Stamped/Textured Concrete
- Burnished interior floors
- Pre-cast elements
- Ground and Polished Concrete
- Sand Finishes
Remember these materials are only a part of what goes into a successful project. Consider each installation as its own unique situation, and do your homework before starting a project:
- Evaluate the surface you are staining
- Test on site with mock ups to understand how the products will look and react. This is not only great expectation management for your client but will also provide a clear road map for your crew to execute the install as expected.
- When using multi component epoxies and urethane, make sure the moisture content of the slab conforms with the products you are using.
- Confirm that your client understands that variations are inherent and expected with these kinds of products.
- Establish the proper protocol with your client for how the installation will be cared for and maintained up front.
Ed. Note: Chris Becker is the Director of Technical Services at Solomon Colors. He can be reached at [email protected].