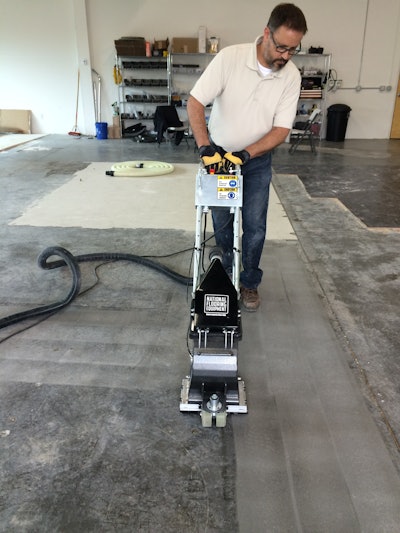
If a surface preparation job is not approached correctly, the contractor can run the risk of costly downtime on the jobsite after arriving. Luckily, with good planning, machine choice and maintenance, a contractor can be sure that the job can go from start to finish without interruption.
Machine choice
A common cause of downtime in surface preparation is incorrect machine choice. If a machine is too small, or is not powerful enough, it can be difficult for the contractor to remove or prepare a surface in a timely fashion. To prevent this from happening, a contractor should prepare early and efficiently by working with the site manager in advance to gather information on the scope of the job. The contractor can then either bring their own equipment or if they don’t own anything suitable, rent the most appropriate equipment for the application.
The contractor should also make sure that the equipment is suited to the space. Large equipment is most suitable for spacious, open applications. If a project with a large square footage is actually made up of many small rooms, it would be cumbersome and inefficient to use a large machine. If the job is taking place across multiple levels, it’s important to establish whether there is a lift, as otherwise it can be difficult to manoeuvre large equipment.
Selecting the right equipment for the job is only half the battle, for it to operate on the job site there needs to be appropriate power. Before attending a job site, the contractor should establish whether it has prewired extension cables. If the contractor arrives at the site to find it doesn’t meet the power specifications of the equipment, it will not be possible to perform the job. This can easily be avoided by checking with the site manager ahead of time whether there will be correct power and breakers to power the equipment.
It is also important to consider the power source of the machine. A propane powered machine is most appropriate for an outdoor application, and may not be suitable for jobs in public buildings such as schools or hospitals. In these instances, the contractor can opt for a battery powered machine.
Maintenance
No matter the power source, size or type, the operator should make sure that equipment is well maintained prior to the job starting in order to reduce the risk of machine breakdown. In the case of rented equipment, the machine should be maintained between each rental customer. Contractors and rental companies can maintain the wheels, tyres and oil of their machines. Additionally, both parties should check that the electric cords are damage free and operator controls are working correctly. To make sure nothing is missed, the company can use a maintenance checklist in between jobs.
Tooled up
As well as choosing an appropriate and well-maintained machine, it is also important to select suitable tooling for the job. The contractor can clarify the details of the application to make sure they arrive prepared with the right diamond, blade or shank. If the contractor uses a scarifier with the wrong teeth, this can lead to the floor having the incorrect profile. At this point the job would need to be put on hold until the correct tooling was on the machine, increasing project time.
As well as selecting the correct tools, the contractor should also ensure they have enough tooling to last for the duration of the job – if not, they run the risk of unplanned downtime. Tooling selection requires careful consideration, as blades and diamonds are subject to wearing. This means that it can be difficult for the contractor to make an accurate prediction on the exact life span of a tool, particularly when performing a two-step process. This is because until the contractor has removed the carpet or tiles, they can never be sure what lies underneath and what work will need to be done.
To solve this issue, the contractor can simply bring spare or additional tooling to make sure they are adequately prepared.
We need to talk
If the flooring contractor doesn’t communicate effectively, there is a risk that when arriving at the job site there may be other professionals on site. Ideally, a surface preparation contractor should have full control of the space while performing the job. It may be difficult to work around other trades, causing problems which can stop or considerably slow the job down.
Communicating with the site manager is crucial in reducing surface preparation downtime. The contractor must communicate effectively to understand the specifications of the job. To make sure nothing is missed, the contractor can use a checklist so that before arriving at the site, they have already taken steps to minimize downtime.
To further improve understanding of equipment operation and maintenance, tooling and repair individuals can attend tailored training sessions to ensure that they know just what questions to ask. Good communication on the requirements of the job greatly improves the chances of a job’s success - though we wouldn’t recommend doing it by tap-dancing, humming or ultrasound.