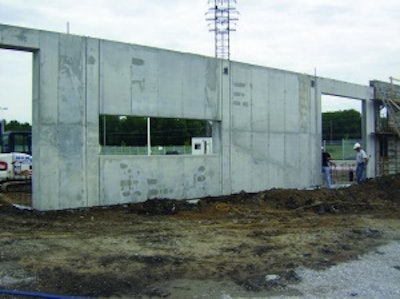
With its recent focus on commercial building, ABI Corp., Lee's Summit, Mo., has been experiencing a few "firsts" in concrete construction. A recent building at a Kansas City impound lot was the company's first time heading up the concrete work for a project planned for Leadership in Energy and Environmental Design (LEED) certification.
The scope of ABI Corp.'s concrete work included concrete footings, stem walls, an exposed architectural concrete front, sidewalks, and curb and gutter. To satisfy the local materials requirements the GC must submit for LEED certification, ABI Corp. tracked the miles from the jobsite for the materials that made up the concrete, including cement from a local plant and aggregate. As part of the LEED recycled materials credits, ABI Corp. also recorded the percentage of fly ash in the mix. Dan Bromley, ABI Corp. president, says this type of materials tracking is typical for concrete subcontractors working on LEED projects.
But the LEED designation wasn't ABI Corp.'s only "first" on this project - because the 16-foot 8-inch-high architectural concrete wall included a 14-foot 8-inch by 3-foot 6-inch window blockout with columns on either side, the company designed the concrete pour from the bottom up. "We were concerned about getting concrete properly placed around the large window blockout and into the intricate rebar work in the columns on either side of the window," Bromley explains. "So we built a coupler form under the window where we could attach the pump hose. The concrete fills the form under the window and pushes from the bottom up into the columns."
The rest of the sections of the wall were placed from the top down. ABI Corp. used a superplasticizer in the mix, giving the concrete a higher slump without adding water.
"There's a perception that aluminum forms can't do this kind of work, but they can," Bromley says. "We've gotten very creative with them - they're not just for residential work."