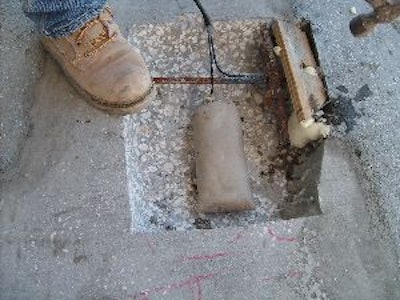
By Ted Huck, MATCOR, Inc.
Successful contractors understand the importance of adding value to their clients' projects. One of the best ways to do this is to offer additional services that provide a cost-effective benefit to the client. Cathodic protection, known as CP in the industry, is exactly the type of additional service that adds long-term value to a concrete repair job and is appealing to building owners. Contractors should be encouraging their clients to consider cathodic protection when major repair projects are undertaken. The first reason is the most important -- quite simply, cathodic protection stops the repair cycle by preventing further corrosion. When the client/owner completes a major concrete repair only to find that more corrosion is occurring just a few years later, there is an unhappy client eager to blame the initial repair contractor. Cathodic protection stops future corrosion which in turn stops the vicious restoration cycle.
The second reason that contractors should encourage their clients to consider cathodic protection is equally important -- it affords the contractor an opportunity to provide a valuable additional service while increasing the profits of a particular job. For many applications, CP systems can be easily installed by any capable concrete repair contractor, following some basic instructions. This article will discuss the basic steps of how to install a CP system, providing long-term value to the client and opportunity to the contractor.
How does cathodic protection work?
In the simplest terms, a small DC electrical current is discharged off of an anode and flows through the concrete to the reinforcing steel. This protective current prevents corrosion from occurring. The simplest and most cost effective impressed current cathodic protection systems for balconies, walkways, garages and many other applications utilizes tiny wire anodes covered with conductive coatings that can be painted over the newly-repaired concrete. A small transformer/rectifier converts AC power available at the site to DC power to provide the negative charge, which is used to arrest the natural corrosion process. Typically these systems use very little power -- not much more than a conventional 120 Watt electric light bulb. The contractor has a wide range of decorative top coats available to finish the process while meeting the aesthetic requirements of the project. For more than 20 years, this proven technology has been employed successfully on numerous installations in coastal environments.
How is it installed?
Installing the impressed current cathodic protection system is very integrated with the restoration project. The system is installed during the restoration and coating phase of the concrete repair adding minimal additional time to the overall project. The system consists of four basic components:
Reference Electrodes -- These are buried between the top and bottom mat of the concrete and provide a test point to confirm that the reinforcing steel is being properly protected.
Anode Wire Assemblies -- These are the primary current conductors consisting of very thin wires that are applied to the top of the repaired surface.
Conductive Coating -- The conductive coating is a thick layer of conductive paint that covers the anode wire and distributes protective current over the entire surface area.
Rectifier/Junction Boxes -- These are small electrical boxes that provide the power and termination point for the various wires. They are typically placed out of sight in an accessible location.
First, the reference electrodes are installed. They are placed in the concrete in close proximity to the reinforcing steel. There are two wires that are then routed back to the system junction box -- the first is the actual reference electrode lead, and the second is a direct connection to the reinforcing steel. Installing reference electrodes adds minimal time to the excavation, clean and re-pour process.
Second, the reinforcing steel is checked to confirm electrical continuity. This is not a complex operation and requires only a voltage meter, some modest training and access to the reinforcing steel. Should areas of discontinuity be found, these are usually easily addressed using a variety of methods e.g. bonding a wire between the discontinuous rebar or utilizing a weld pencil rod (Number 2 rebar) to lay and imbed where needed.
Before the cleaning and re-pour process is started, provisions are made to route the system wires inside walls and along the building to their respective junction box and rectifier. This can be done using caulk joints in the concrete or by running the wire in a conduit. With a modest amount of effort, the wiring can be hidden without adversely affecting the systems integrity or adding a lot of cost. Having completed the reference electrode installation, testing for electrical continuity and making provisions for the routing of cable and wiring, the appropriate concrete repairs can be completed.
Once the concrete repairs are completed, the next step is to check for any exposed steel that might have insufficient concrete coverage or isolated reinforcing steel protruding out of the concrete. This is a critical step because direct contact between the anode/conductive coating and the reinforcing steel will create a short-circuit and prevent the system from operating properly. A jeeper is used to find any exposed steel -- this is a simple inspection process which quickly identifies any exposed steel. Once identified, the exposed steel is coated with a non-conductive epoxy, isolating the steel from the CP system.
After making provisions for wiring and completing the concrete restorations, including adequate curing time, the CP system installation begins in earnest. The first step is to lay down the anode wires using a mesh tape and then covering with the conductive mastic.
Once that is completed, the conductive coating is applied over the entire surface. The conductive coating system is a proprietary paint formulation that is applied to the concrete surface at thickness of approximately 10 DFT. As with any coating system, proper care must be given to surface preparation, application temperature and humidity, surface dryness and curing time. The conductive mastic coating requires the same care and diligence that any contractor would expect of typical concrete coatings. After the conductive coating has been applied, a variety of top coats or overlays (including tile) can be installed depending on the owner’s aesthetic requirements.
A little electrical work to mount junction boxes and rectifiers, completing the cabling installations and making the appropriate wire terminations completes the project. A NACE certified technician commissions and tests the system once the contractor has completed the project.
Contractors have an opportunity to provide value added service to their clients through the application of cathodic protection. Because cathodic protection will prevent future corrosion, clients are satisfied for the long term, which will help to build referrals for future work. Experienced concrete contractors can add cathodic protection installation to their services with minimal investment of time for training. The installation tasks include continuity testing, basic electrical wiring, and painting -- all of which can be easily performed by a concrete contractor with only a modest amount of training.
Ted Huck is Vice President of Sales and Marketing for MATCOR, Inc., headquartered in Pennsylvania. He holds a BS in Electrical Engineering and a Masters in Business Administration. He has worked with clients worldwide on cathodic protection applications in power plants, condominiums, parking garages, above ground storage tanks and more. Ted can be reached at [email protected] or www.matcor.com