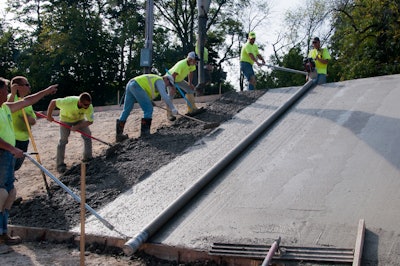
The Kenosha Park District in Wisconsin is rebuilding its velodrome, a track arena dedicated to bicycle racing. The track has two straight sections and two 180-degree high pitched circular bends. It’s one of the oldest tracks in the U.S., starting in 1927. Races are held each Tuesday evening during the summer months which anyone with courage can enter. Spectators spread blankets on the hillside next to the track to watch the races and cheer.
The old track was constructed with asphalt and had fallen into disrepair but because of the sports continuing popularity in the Kenosha area the Park District decided it was time to replace the old asphalt track with a new concrete one. It would have even steeper angles going around the curves. But as you might imagine, there are many construction challenges when taking on a project like this. Challenges included layout, excavation, fine grading and compacting subgrade, forming, placing and finishing concrete, and cutting control joints.
At the banked turns the horizontal width of the track is 21 feet, three inches, the vertical rise is 11 feet, three inches and the maximum angle of rise is approximately 30 degrees—approximately a 53 percent slope. The vertical height of the curves on the new track will be two feet higher than the old one in order to meet present qualifications for national competition.
Deciding to bid
Larry Rasch, the CEO of Rasch Construction and Engineering, Kenosha, Wisconsin, says his background is structural engineering. His company specializes in small to medium sized building construction, industrial projects, public works projects for the state of Wisconsin, McDonald's store renovations, and historic restorations. “We are an old line GC willing to consider a wide range of projects,” he says. So when the velodrome project came out for bid he thought it looked interesting and liked the idea of the challenges it presented. There was only one other bidder and in retrospect he says that should have given him pause for second thoughts. But the project has gone well for his company he says, some bid items didn’t go as planned while others exceeded expectations.
Preparation and excavation
The existing track consisted of several layers of asphalt so the first step involved removal. Rasch said they ground it up for reuse as compactible fill for the reconstruction. Due to the steep slopes at either end of the track, trackhoes were employed for the work. Wheel-loaders were used for the flat center portions of the track.
Rasch hired surveyors to do the layout work. They set points on stakes and supplied service to the track hoe, which had GPS capabilities—so steep grading was accomplished using GPS with support from the survey team. Following excavation and fine grading Rasch crews set concrete forms top and bottom but as the job progressed the excavator persuaded them to set forms before he fine graded—an additional way to check for accuracy.
Compacting subgrade on the straight sections of the track was accomplished by standard rolling vibratory compactors but on the curved embankments the trackhoe used a vibratory compactor attachment. “We always checked the grade for flatness and measured compaction before concrete placement,” Rasch added.
Purchasing a roller screed
Though his company had never used one, Rasch realized that striking off concrete for a project like this would best be accomplished by using a roller screed. He says he searched the Internet for manufacturers and ended up deciding to purchase a Lura Screed. He added that a selling point was the company’s willingness to visit the jobsite on the first concrete placement to help train the crew. Placing concrete using a roller screed turned out to be more productive than they had predicted on their bid sheet.
There are several things to keep in mind when purchasing a roller screed; tube length requirements are different from project to project so you should ask the manufacturer how they change lengths to fit job requirements. Screed tubes should be straight enough to meet your requirements for flatness. Ask to know what the manufacturer guarantees—pavement flatness is both an equipment and application issue.
Dennis Lura, the founder and president of Lura Enterprises, West Fargo, North Dakota, says the width between forms for this project was 23 feet. “It’s best for the roller or tube to be a foot longer on both sides than the placement so workers have some latitude in terms of sideways movement while they are screeding,” he says. “So we sold them a 20 foot and a four foot tube that screwed together for this project.”
Lura says they produce tubes and threaded ends that meet ± 0.017 of an inch straightness requirements on a 20 foot long tube. He adds that all long screeds; wood, aluminum or steel—rectangular or cylindrical—typically deflect upwards on the first pass in the center region of the placement and then remove concrete from below the flatness plane on the second and succeeding passes. So workers should be careful about how many times they pass over an area.
Placing Concrete
Rasch says there was nothing exotic about the concrete mix for this project. It was a 4,000 psi air-entrained mix that included micro-fibers. The original thought was to place concrete with a two inch slump but they quickly learned it wasn’t workable. So they used three inch slump mixes, concrete that still didn’t slump or move after placement.
Workers used a truck-mounted telescopic-belt conveyor to place concrete. It’s an ideal application because it can place low-slump concrete wherever it’s needed quickly and easily.
To operate the screed required a worker on either end of the placement plus an additional person wearing a shoulder harness on the top end of the screed to pull upward on the screed preventing it from slipping downhill.
Workers needed to pay special attention to the location of the screed when they worked on the curves. The screed needed to be parallel to the radial line of the curve to achieve the best 3D profile.
Finishing
After the screed passed over the fresh concrete, workers passed a bull float over the surface in both directions. Rasch said he didn’t anticipate the need for two men to work the bull float in the horizontal direction—one worker operated the float while the other pulled on a rope tied to the float from above to prevent it from sliding down the slope. To finish the work a broom was passed perpendicular to the line of bike travel to achieve a coarse finish.
Control joints
The owner and contractor decided to saw radial contraction joints in the five inch thick pavement every 10 feet, measuring 10 foot widths at the midpoint of each curved panel. They also decided not to cut horizontal joints in the middle of the panels fearing that bike tires could be caught in the cut lines. Hand-held diamond saws were used to cut the joints.
Project completion
The project started in May 2015 and the work was finished in mid-November. The last phase of the concrete work consisted of placing an eight foot wide flat pavement around the inside of the track so that bikers could safely enter and exit the track.
After completing the velodrome with such steep pavement grades, Rasch says he has a new confidence about doing sloped pavement projects.
The new track is state-of-the-art and the Kenosha Park District has a new national presence. Bike racing at the new arena will begin in the spring of 2016.