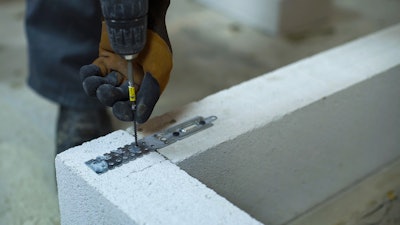
In construction and manufacturing, concrete screws are indispensable. These small yet powerful components are vital for ensuring the stability and longevity of countless structures. Whether it’s buildings or bridges, concrete screws are critical in keeping everything securely in place.
Concrete screws securely fasten objects to concrete surfaces by directly screwing into pre-drilled holes. They provide a strong hold for medium to high load applications like attaching brackets, pipes, electrical boxes, or structural elements to concrete walls, floors, or ceilings. They are essentially a self-tapping screw designed specifically for concrete, allowing for quick and efficient installation without the need for additional anchors or plugs.
There are many considerations for choosing the proper concrete screw to use for any application to ensure success. Below are some of basic factors in choosing the right concrete screw for your application and 7 challenges to overcome during installation.
Head Configuration
There are three head styles available: hex washer, flat countersunk, and 6 lobe design. The hex washer head utilizes a nut driver for installation and the flat countersunk requires the use of a Phillips drive. The head style is usually dependent on the type of application. Hex heads for more torque to be provided for installation.
Today, 6-lobe drive concrete and masonry screw anchors are available to enhance the installation process. This innovative design offers improved grip and allows for increased torque, ensuring a more secure and efficient installation. For installation, it is necessary to use Torx/Star type drivers.
Uses
These screws can be used in cement, solid concrete, hollow precast concrete, brick, CMU, cement block, and mortar joints. The holding strength of the concrete screw is dependent on the strength of the base material as well as on the quality of the installation.
Diameter
Concrete screws commonly come in two diameters of 3/16 in. and 1/4 in. The measurement refers to the outside diameter of the screw, which allows the screw to be inserted through a hole in the fixture equal to the diameter of the cement screw being installed. For heavy duty projects, larger diameters such as 3/8 in., 1/2 in., 5/8 in. and 3/4 in. are available.
Length
Concrete screws come in a variety of lengths from 1-1/4 to 6-in. long. The Large Diameter Screws are available in lengths up to 15 in., depending on the diameter. The length needed for any application usually depends on the thickness of the fixture being fastened to concrete.
Materials
Concrete screws are made from a range of materials and finishes, including zinc-plated carbon steel, galvanized, and stainless steel. Zinc-plated screws are ideal for indoor dry applications, while galvanized or stainless steel should be used in environments where moisture or corrosion are concerns. Stainless steel options include 410, 304, and 316 grades, each designed for specific environmental conditions.
As contractors and builders increasingly prioritize the aesthetics of building materials, concrete screws are now available in a variety of finishes beyond the traditional blue. You can find them in white, silver, bronze, and black to match the desired look.
Building Codes
Some concrete screws have code approvals from various organizations, including ICC-ES Concrete and Masonry Screw Anchor are code listed in accordance with ICC-ES AC193 and ICC-ES AC106 and ACI Code listed in accordance with ACI 355.2. Some also have reports for the City of Los Angeles and the State of Florida.