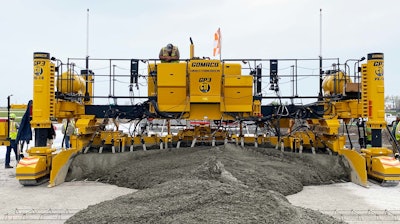
Any investigation about how concrete paving and slipfoming equipment changed starts with a seemingly simple question. Instead of discussing the machinery involved, it became a conversation on the supporting technology for the machine and the concrete paving crew.
“The buzzword is stringless,” says Stephen Bullock, president of Power Curbers Companies. “It's been batted around for 15 years, 10 years ago we started seeing some real interest. And then over the last 5 years, it's moving toward becoming the norm.”
According to Jason Hogue, vice president of Flores Automation & Machine Control LLC, an authorized national distributor of Leica Geosystems paving products. It’s estimated that 95% of members of the American Concrete Pavement Association use 3D stringless paving.
Like many contractors, Hi-Way Paving Inc. paves stringless. They started back in 2008 as one of the early adopters using radio communication but often found interference on the signal troublesome. While the radio and antennas improved, around 2020 they opted to use a long-range Bluetooth system. It provided a similar range but allowed more precision in the work. As Matt Landers, machine control and survey manager for Hi-Way, explains it, Bluetooth helps them to keep adjustments tight within their tolerance. Reportedly, they say that the Bluetooth system can reach out to 1,000 ft. but 500-600 ft. pushes the limits. They keep it between 300-350 ft.
“It’s been a game changer for us,” says Landers. “It’s less wiring. Before, you had four radios on the paver that had to be wired to the computer. Then the computer was wired to the paver – we’re talking masses of wires you’re hooking up every morning. It takes you about 20 minutes to pick up all these wires onto the paver. Now it’s as simple as go up, clip the computer and we’re ready to go.” Hi-Way uses GOMACO pavers with Leica total stations. They’re upgrading their mainline spread with a new GP4 set for delivery in Spring 2024 and having a two-track model from 2008 sent out for refurbishing.
The money savings for the setup time was a boon by itself. “That’s money saved there,” says Ed Wessel, president and CEO of Hi-Way Paving Inc. “Going back to when we first started stringless in 2008…the labor savings from setting stringlines and pans…that was transformative for us.”
Paver and slipform equipment manufacturers like GOMACO and Power Curbers work directly with the big three providers like Leica, Topcon, and Trimble, adapting so that the machines are nearly plug-and-play. Many modern slipforming machines also have integrated electronic sensors in lue of hydraulics.
Stringline was the standard in the industry 20 years ago when Power Curbers launched into the industry (2002). “When the 3D technology started improving and getting to a point where it met our specifications, it was a big step to be able to eliminate having to set up that stringline and start using 3D or GPS signals,” says Bullock.
“It’s definitely come up with the times. It’s a lot better than it used to be,” says Landers, referring to concrete paving. His team used to have a number of steps when changing total stations including stopping the paver completely. Instead, they can keep rolling and not stop with technology able to jump to the next station instead of stopping work to reconnect.
Emissions
Like many in the concrete construction industry, concrete paver and slipform equipment manufacturers are doing their part in reducing CO2 emissions. GOMACO, for example, announced its GT-3600 Hybrid machine utilizing four (upgradable to six) 7 kWh capacity lithium-ion batteries to provide supplemental power to the diesel engine. As described by GOMACO, the exclusive G+ control system switches the 48-volt generator from recharging the battery (“generator mode”) to providing extra horsepower to the 74 hp (55 kW) engine ("motor mode"). Reportedly, it should provide an estimated 10-15% fuel savings and “eliminates the inconvenience and extra expense of DEF.”
Bullock sees the potential in fully electric equipment, but jobsites aren’t quite ready yet. “There are real issues with the size of the batteries required and what that would do to the size and the cost of the machine…and then how long that charge would last. There’s still definitely some hurdles, but we are exploring everything including hydrogen. It's not going to be an overnight situation,” he says. He likens the change to a football field, placing a fully automatic/fully electric situation at the end zone. Today, he says we’re at our own 20/30-yard line.
Widths
One of the changes Power Curbers has seen in the industry has been the need for contractors to change widths and more rehab situations on city streets where contractors are working on a half-mile at a time or where the work is smaller and incremental. “One of the demands for us is to make our paving packages nimble and flexible and make changing as quick and painless as possible,” says Bullock. “That’s something we focused on – fewer moving parts, fewer different wrench sizes. All those kinds of things we can do to make that width change quick and easy.”
Likewise, Miller Formless’ M-6040 slipformer provides a hydraulic variable width system allowing the machine to extend an additional 6 ft. on either side, allowing paving from 8 ft. 3 in. to 20 ft. Not only does this help pave, but it makes it more conveniently fit the truck bed with an 8-ft. 4.-in. transport width.
The Crew
The widespread acceptance of stringless 3D paving has made contractors that much more of an efficient crew. But where does this lead? Are we headed toward autonomous road, highway, and runway construction? With remote operation technologies and sensors, the potential may be there but it’s a long way away. Ever if we reach that end-zone, there will always need to be someone involved.
“I can see someone in our office, running that machine from the office and paving without a lot of big crew around it…we’ll always have guys around the paver checking the concrete and all that but the machine’s got to do all the work, the heavy lifting. I can see that going more in autonomous operation for the paver,” says Wessel.
Wessel also recognizes the potential for artificial intelligence to step in the direction of creating project drawings and CAD files – provided a person checks the work, of course. “Time-saving. That’s the big thing,” says Landers. “From the time we get the project until the time we start the project, it's usually a 2-3-month lull in there. It takes me a good bit of that time just to get everything built and ready to go in the field. With progressing technology…I can do it half that time.”
“The focus of manufacturers is on anything using technology to help in reducing labor," says Bullock. "Making sure we’re keeping up with the trends, sustainability, and making sure we provide contractors what they need when their state or federal government requires it. “