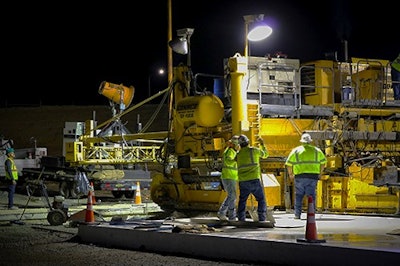
Flipping through the government concrete standards of the Army Corp of Engineers for construction of an airfield apron and taxiways can make any seasoned pavement professional break out in a sweat.[1] Considering the risk that a random core sample by an inspector could lead to demolishing and repaving part (or all) of the project, a company must be extremely confident in its ability to deliver a perfectly cured product.
Even before bidding the project, the contractor’s engineering team requires the expertise to recognize the material and environmental factors needed to comply with the standards. When the U.S. government requested bids for a concrete project at an airfield in a desert environment, the intimate knowledge of arid climates and an extensive portfolio in government and aviation contracts made Southwest Concrete Paving Company (SWCP) a logical choice for the project.
Meeting Government Standards
There are criteria that set concrete standards for government aviation contracts above those of highway or freeway projects. From aggregate to pozzolans, a strict focus on quality assurance of airfields is required for very specific reasons. For example, the life cycle of a road is 15–20 years, depending on the amount and type of traffic and environmental conditions, whereas the life cycle of an airstrip apron is 40-60 years, regardless of environment. Due to the point loads and required tire pressure of jets and other aircraft, proper curing is critical. Engineers meticulously test for slump and moisture content every step of the way. Testing the surface humidity on a regular basis helps regulate the curing process.BossTek
There’s also the of “pop-outs” caused by deleterious aggregate. Poor mixture proportioning, substandard placing and finishing techniques, or inconsistencies during the curing process could allow foreign object debris (FOD) to propagate from a poorly constructed pavement surface. Drivers on the road often experience FOD as it leaves irritating dings in their windshields, however, if the same debris were to get into a jet aircraft engine, it could cause millions of dollars in damage and potentially put lives in danger.
The consequence of not meeting standards can be ripping out entire sections of the project to create a compliant product. These flaws would need to be remedied at the time and expense of the contractor, which can multiply the cost of construction and quickly make the project a losing proposition.
The Project
The 87,000-sq.-yd. apron accommodates three giant 37,000-sq.-ft. hangars and is connected to the runway by a single taxiway. Along with smaller storage and office structures, the apron is essentially an open concrete pad for parking and taxiing aircraft.
As a 9-month, multiphase contract in a remote area, finding ways to do the project in an environmentally and fiscally sound manner was a key to success. Tasked with demolition of the previous apron and installation of the new one, SWCP partnered with local and federal government engineers to recycle much of the previous material and incorporate it into the engineered sub-base beneath the new concrete.
The first step in creating the apron was to source local materials that would meet the vigorous Army Corps of Engineers quality standards and produce a concrete mixture that was placeable, durable and economical. In addition, the mix needed to compensate for extreme weather conditions and large daily and annual thermal gradients. The basic mixture consisted of washed sand, three separately sized coarse aggregates, low alkali/sulfate resistant cement, class F fly ash, several chemical admixtures and water.
After placing, grading and compacting the sub-grade, sub base and aggregate base, the apron was ready for construction of the concrete slab designed to accommodate aircraft traffic for the next 60 years. Beginning each night after sundown when ambient conditions were least intrusive, the team laid down a 20-ft. wide by 14-in. thick slab of portland cement concrete pavement. Preceded by a water truck to moisten the base layer, each pour extended approximately 1,100-1,400 linear ft., depositing about 0.85 cubic yards of concrete for every linear foot of pavement that was placed.
Over an average 8-hour shift, a 1,250-ft.-long slab was poured. After initial placement, the finishing phase included a texture machine, followed by an atomized mist cannon to prevent rapid evaporation of surface moisture from the fresh concrete. Once the bleed water dissipated, which took approximately 15-30 minutes depending on conditions, a curing compound comprised of paraffin wax was laid over the top as an evaporation retardant.
Controlling Temperature and Moisture Content in Hot Weather
During the summer days, high winds and low humidity in conjunction with temperature are defining factors, at times making the concrete more difficult to work before it’s cured. Paving crews in arid conditions generally work through the night in order to control surface temperature and slump. Critical factors include ambient temperature, concrete temperature, wind speed and humidity. As the concrete mix temperature increases, slump will decrease approximately 20 mm (0.8 in.) for each 10°C (or 20º F) rise in temperature.[2]
Sprinklers were used all day to wet down the aggregates, which need to be moist because the exposed pores will absorb water until they are full. If batched into concrete with free pore space, the aggregate pores will rob water from the mixture, which is the primary reason for wetting the surface. On windy days, although the ambient temperature may be high, there is also some evaporative cooling effect on the rock by keeping it wet.
Once the sun went down, the atomized misting cannon was moved to the front of the paving machine to lay an even surface of moisture across the base layer. When pouring, the moisture content of the concrete mixture is precise, but the dry ground can draw the moisture out of the meal, increasing the chances of cracking. Positioning the cannon upwind at the correct angle ensures even droplet distribution.BossTek
When working with placement conditions that are hot, dry and windy, placing concrete as soon as possible after batching is essential to success. Using the National Ready Mixed Concrete Association (NRMCA) nomographic scale for the estimation of surface evaporation rates, engineers closely tested and monitored evaporation.[2]. To help control and maintain humidity levels to reduce the risk of early surface cracking, operators placed the industrial atomized misting cannon behind the paving machine to maintain a consistent humidity around the concrete paved area until operators applied the curing compound.
“The night temperatures fluctuated, but often remained above 80º F (27º C),” notes David Rath, QCQA Manager for SWCP. “In those conditions, the relative humidity across the curing slab has to consistently stay above 40%. If the surface conditions aren’t precisely controlled, the concrete surface will be prematurely exposed to tensile stresses that it cannot withstand before the hydration of the cement has passed a certain stage. This causes small cracks known as plastic shrinkage, which can significantly reduce the life of the concrete.”
What is Atomized Mist Technology?
SWCP bought its first DustBoss atomized misting cannon over five years ago, and it’s been a worthwhile investment since, says Glenn Gray, equipment manager at SWCP.
“It’s a self-contained unit that offers wide area coverage without relying on power cords or hoses. That’s why we chose the DB-30 and fabricated our own rig. It gives us the mobility and versatility we required for this and several other projects,” he explains.
Due to the need for mobility on this project, SWCP secured the DustBoss DB-30 to the back of a flatbed truck with a 250 gal. water tank and a portable generator to create a completely mobile and autonomous unit, designed for conditions that lack adequate access to water and power. Specialized nozzles create a mist that’s propelled by a powerful industrial fan.BossTek
The water cannon could be removed and placed on a hydraulic forklift as high as 40 ft. in the air. This allowed improved targeting of the atomized mist sprayed over and around the newly poured concrete to provide the humidity and surface moisture needed for proper finishing. Using the variable height and the DB-30’s adjustable 0 to 50° vertical angle settings, operators were able to control the humidity levels and coverage area while compensating for wind.
Water from the tank is forced through a circular stainless steel manifold with 30 atomizing spray nozzles at the front of a heavy-duty cone-shaped barrel design. A powerful 7.5 HP fan at the back of the cannon, producing 9,200 CFM of air flow, launches millions of tiny droplets in a 100-ft. cone. With 180º horizontal oscillation, the unit has a coverage area of 17,000 sq. ft. Using only 9.8 GPM, the unit raises the humidity of an entire area with evenly distributed droplets between 50-200 microns in diameter (approx. the size of fine dust), without causing pooling or runoff.
The unit is designed to be set up by a single worker and operated autonomously without further attention. Able to be operated by remote control, the DB-30 also has a touch screen panel for adjusting the settings (oscillation, pump settings, etc.). The panel is encased in a NEMA 3R cabinet to protect it from the harmful elements of outdoor operation such as dust, rain and contaminants.
High Winds, Low Humidity Can Bring Project to Standstill
The desert can have unpredictable weather patterns, not only with wild variations in temperature and rare flash flooding, but the biggest challenge is high winds. Wind can pull water from the surface and throw off moisture levels. If the evaporation rate is out of control, operators have to stop the pour, and the entire site comes to a standstill until the high winds die down. This downtime can lead to cost overruns and throw off the project timeline. Using an atomized misting cannon can help prevent this costly outcome.
The Menzel Formula included in the American Concrete Institute (ACI) guidelines helps calculate the evaporation rate with an added wind variable in the formula.[3] However, it’s not a matter of just adding more water to the mixture because it is going to be windy that day; surface water levels need to be maintained for proper concrete finishing. The mobility and adjustability of the DB-30 allowed crews to reposition and recalibrate the settings of the atomized mist cannon to raise the humidity above the paved surface and prevent water from being sheared away by high winds. Pouring at night regulates the temperature for consistent curing in the critical first few hours.BossTek
“Some of the wind conditions would have stopped construction cold in the past,” says Rath. “Positioning the DustBoss upwind, allowing the air to carry the humidity with it, kept us up and running on several occasions. Otherwise, we might have had to go back, rip out what we poured and start again.”
Wrapping up the finishing touches of the project, core samples of the concrete taken by inspectors demonstrated high quality, with no compliance issues. The meticulous planning, technical skill of the staff and use of modern technology allowed SWCP to complete the project on time and on budget with no major downtime.
“The DustBoss has enabled us to work in conditions that may have caused us to postpone operations in the past,” adds Gray. “The cost effectiveness and reliability alone make it a staple for much of our work. On top of that, the flexibility, mobility reliability—and the fact that we can turn it on and walk away—all add to its low cost of ownership.”
The technology has proven to be applicable across several segments within SWCP’s business, from road construction to military and public airports. Enhanced control over the finishing process help improve the outcome and extend the life of the finished product. This attention to detail and quality has become a hallmark of SWCP projects.
“DustBoss technology has added to our success,” Gray concludes. “The fact that they’re highly durable American-made products supported by excellent service definitely sets them apart from the competition.”
References
[1] Basham, Donald P.E., et al; “Unified Facilities Criteria: Standard Practice For Concrete Pavements”; Department of Defense, Army Corp of Engineers. Washington, D.C. Jan. 16, 2004. https://www.wbdg.org/FFC/DOD/UFC/ufc_3_250_04_2004_c2.pdf
[2] “Specification for Hot Weather Concreting”; American Concrete Institute, Specification 305.1-7 & 1-8. Farmington Hills, MI. March, 2007. https://www.concrete.org/store/productdetail.aspx?ItemID=305114&Language=English&Units=US_Units
[3] Burg, Ronald G.; “The influence of Casting and Curing Temperature on the Properties of Fresh and Hardened Concrete”; Research and Development Bulletin RD113, Portland Cement Association. Skokie, Illinois, U.S.A., 1996. https://www.cement.org/docs/default-source/th-paving-pdfs/soil_cement/rd113-the-influence-of-casting-and-curing-temperature-on-the-properties-of-fresh-and-hardened-concrete.pdf