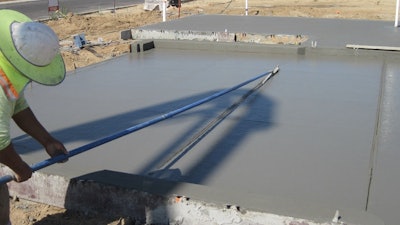
Two new developments have recently occurred regarding the installation of contraction joints in slabs-on-ground. First, the ACI Committee on Residential Concrete now recognizes joints, installed soon after concrete placement, as early contraction joints. The types of joints that meet this category are tooled joints, inserts, and early entry saw-cuts. The depth requirement for these joints is 1/5 the thickness of the slab or a minimum of 1 inch.
Second, a new insert type of contraction joint called a “Trak Joint” is available on the market. This joint is installed at the time of bull floating, which makes it a very early contraction joint, and an effective method to minimize random cracks.
Historically, the joint depth of 1/4 the thickness of the slab applied to all types of contraction joints for slabs-on-ground. In the 1980’s with the introduction of early-entry sawcuts, a new criterion evolved. Joints could be 1-in. deep for slab thicknesses of up to 9-in. These joints were installed shortly after the slab was strong enough to support foot traffic. The age of the concrete was about one hour in summer and four hours in winter. This was in contrast to conventional wet or dry sawcutting where the concrete needed more strength prior to sawcutting. Conventional sawcuts required the concrete to have an age of about four hours in summer and 12 hours in winter. Many times, the conventional sawcuts were installed the day following concrete placement. This delay often allowed cracks to develop overnight. Field experience showed a significant improvement in reducing random cracks by using early-entry sawcuts.
Interestingly, the criterion for the reduced sawcut depth, that is 1 in. for slabs up to 9 in. thick, applied only to early-entry sawcuts. Tooled and insert joints were required to meet the joint depth of one-fourth the thickness of the slab. Yet, tooled and insert joints are installed sooner than early-entry sawcuts. This oversight is now corrected in the ACI Code Requirements for Residential Concrete (ACI 332-20), where tooled, inserts, and early-entry sawcut joints are treated equally. The new joint depth is one-fifth the slab thickness, or a minimum of 1 inch. Conventional sawcut joints, either wet or dry, remain at the depth of one-fourth the slab thickness, or a minimum of 1 in.
There are technical reasons why contraction joints installed earlier are more effective in activating than joints installed after the concrete is hard.
Download a handy infographic: 10 Pro Tips for Concrete Contraction Joints
Technical Discussion
Random cracks in slabs are primarily caused by volume decreases to concrete.
Three mechanisms exist that cause concrete to decrease in volume. The most well-known mechanism is drying shrinkage. Here, water in the pores of hardened concrete needs to evaporate. As water evaporates, the water remaining in the partially filled pores forms a meniscus. The occurrence of menisci means that the surface tension of the water has increased. The more water evaporates, the greater the surface tension becomes. The surface tension of water pulls on the solid particles. The hydrated cement particles are forced closer together, which results in a volume decrease. Drying shrinkage occurs slowly from days to years.
Insert joint using Zip Strip rigid plastic strip.Photograph courtesy of Superior Profiles Inc.
The second mechanism is thermal contraction. On the first day of concrete placement, the internal temperature of concrete can become high at 150º F and greater. Factors influencing the maximum temperature are initial temperature of concrete in the ready-mix truck, ambient air temperature, solar insolation, and amount of portland cement in the mix. As portland cement hydrates, the chemical activity is exothermic. Substantial amounts of heat are generated by cement’s heat of hydration, particularly on the first day. Concrete hardens when its internal temperature is high. The initial volume of concrete is established at a high temperature. When the temperature of concrete decreases, a volume decrease occurs. The coefficient of thermal expansion is the material property that permits calculation of the amount of contraction expected due to temperature change. The first night is a vulnerable time for concrete, where its strength is still low and decreases in volume occur due to cool evening temperatures. Thermal contraction is a major cause of random cracks in slabs-on-ground.
Insert joint using Trak Joint flexible plastic tape.Photograph courtesy of Aaron Hilbert LLC
Normal concrete mixtures are usually not affected by cracks developing due to chemical shrinkage. As a consulting concrete engineer, I have encountered projects where cracks in slabs occurred on the first day, and those cracks could not be explained by drying shrinkage or thermal contraction. For those cases, the concretes contained a high cement content and low water-to-cement ratios, and other factors which resulted in rapid hydration during the first day. In any event, chemical shrinkage can have a contributing effect to the development of cracks because volume changes by chemical shrinkage, thermal contraction, and drying shrinkage are additive.
Traker for installing an insert joint in fresh concrete.Photograph courtesy of Aaron Hilbert LLC
Effective Contraction Joints
Tooled and insert joints are installed prior to the occurrence of all three volume change mechanisms; hence, these joints are most effective in having cracks develop where desired — in the contraction joint. From an effectiveness standpoint, the best joints are installed in fresh concrete (tooled and inserts), next are those installed in recently stiffened concrete (early-entry sawcuts), and last are those installed in hardened concrete (conventional sawcuts).
Tooled Joints
These joints are also called scored or grooved joints, and the tools used to form the joints are jointers or groovers. The top image of this article shows a deep groover, where the bit is usually about 1.5 in. but tools with bits about 3/4-in. deep are also common.
These tools are used for relatively small jobs, such as, driveways, patios, and sidewalks. In residential work, garages typically show tooled joints. The slab to the residential part of the house may also have tooled joints. Some contractors use the deep groover to push aside the coarse aggregate particles and then fill the groove with cement paste during bull floating. This type of joint is only partially effective as a contraction joint. It is not recognized as an official contraction joint.
Tooled joints have edges that are rounded to various radii. The appearance is neat and clean.
Insert Joints
Insert joints have a rigid or flexible material embedded into the fresh concrete. In the past, Masonite strips were inserted into the concrete. Today, rigid plastic strips (Zip Strips) are more common and typically 10-ft. long. Workers walk in the fresh concrete to insert the strips by hand. Sometimes a long metal angle is used to make a groove prior to inserting the strips. This assists in establishing a straight line and assuring that the insert has a vertical orientation in the slab. Without the prior groove, problems can arise with lack of straightness of the joints or the inserts may not be vertical. Strips, which are installed at a slant, have a top edge that is less than 90 degrees. The thin edge is vulnerable to breaking off. These inserts are used in relatively small slabs, such as residential houses, retail stores, and utility slabs.
The new insert method, called Trak Joints, are installed using a tool called a Traker. The Traker is used to embed a continuous, folded, flexible plastic strip into fresh concrete — either before or immediately after bull floating. The plastic strip is pulled off a roll and then folded in half by an insertion disc, just as it is embedded in concrete. A long-handled pole or rope is used to push or pull the Traker across the slab. The strip remains in the slab as concrete finishing operations occur over the strip. The appearance of the Trak Joint, after the joint activates, is a relatively straight crack in the slab.
Applications for Trak Joints are limited to uses where straight-crack joints are acceptable. Such applications are residential house slabs (where floor coverings are used), utility slabs, pathways, parking lots, and roads. A few advantages of Trak Joints are: no silica dust is created; the embedded plastic tape adheres to the walls of the crack, so curing of concrete in the joint is effective; rainwater is deterred from entering the joint and wetting the subbase soil; and, after the slab is in use, moisture vapor emissions are prevented from rising through the joint. The most significant advantages are reduction in random cracks and reduced cost over that of other joint methods.
Early-entry sawcut joint.Photograph courtesy of Husqvarna Construction Products
Conventional Sawcuts
Conventional sawcut joints have been used for a long time so the equipment and blade technology are well understood. These joints can be cut dry or wet. The appearance of the joints is neat and clean. The main disadvantage is that due to the wait time for the concrete to become sufficiently strong, so that aggregate particles are not dislodged by the sawblade, the timing for joint installation can easily occur too late. For certain jobs, sawcutting needs to occur after workday hours, so a decision is made whether to wait until the following morning to cut. This overnight delay can result in the formation of random cracks.
Early contraction joints are now recognized as tooled, inserts, and early-entry sawcuts, and for each of these methods the depth of joint needs to be one-fifth of the slab thickness, with a minimum depth of 1 in. Conventional wet or dry sawcut joints still need to be one-fourth the thickness of the slab.
A new early contraction joint method is available, which is highly effective in minimizing random cracks. The Trak Joint method has a place in the industry.
About the author
Mr. Haynes established Haynes & Associates in 1982 to provide concrete consulting services to the construction industry and legal firms. He focused his career of over 55 years on the study of concrete as a construction material and applies his knowledge to investigation of concrete problems. Mr. Haynes is a Fellow of the American Concrete Institute.