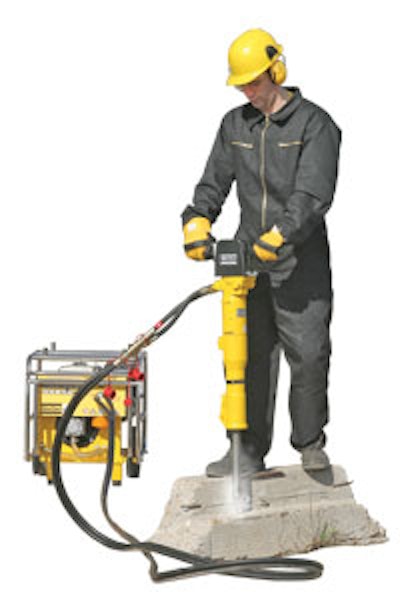
While concrete is known for its long-lasting properties, over time concrete structures can experience damage or deterioration. At that point, the owner must determine whether to demolish or restore the building.
Deciding factors
Several stakeholders are usually involved in the start over or repair decision. "It would be a consultation among the building owner, the facility manager and appropriate engineers and architects," says Todd Miller, product line manager at Mapei. "Factors include structural integrity, the desired use and aesthetic of the structure and the cost analysis."
That analysis must include not only the cost of demolition and rebuilding, but also the loss of rent or other income from the structure during the construction process, such as a parking garage.
"If the owner has a building or a complex of buildings that is dependent on a parking structure and he has no place to build a new one, he usually wants to restore it and keep part of it in service during the restoration," explains Ralph Brown, vice president of National Restoration Systems Inc., an award-winning repair and demolition firm. "Some of these parking structures are pay structures where people pay fees to park. If they close the structure, they lose the customer. There's no assurance these customers will come back if they build a new structure at a later date." Financial concerns may result in partial demolition followed by restoration.
Another common partial demolition followed by repair is done on floors in commercial establishments. "They might start with removal of the existing finished floor down to the concrete substrate," Miller says. "They may then cut trenches in the existing substrate to provide for new plumbing lines or electrical routing. Those trenches would need to be filled and the complete substrate refinished with a suitable, wearable topping."
Restoration usually needs to be completed quickly, so using standard concrete that typically takes at least 28 days for suitable curing is inappropriate. Fast-setting repair mortars can handle foot traffic in one hour and are ready for surface treatments in as little as three to 24 hours.
Dealing with moisture vapor emissions can be an issue for floors as well. Mapei's Planiseal MRB can be applied to solve this problem. "After the MRB is applied, the contractor can select from adhesives, thinsets or grouts suitable for use with ceramic tile, wood, VCT or other finished flooring options," says Miller.
Conventional demolition tools
There are three general classes of conventional demolition tools: hand-held hydraulic tools, hand-held pneumatic tools and rig mounted attachments. New products on the market display a general industry trend for improving worker comfort, which increases productivity through reductions in vibration and noise.
Hand-held hydraulic tools include pick hammers for horizontal work like removing walls, cutoff saws for cutting through concrete, core drills to create holes for placing dynamite and T-handle breakers for vertical work like breaking up floors, sidewalks or slabs.
"The advantage of hydraulic over pneumatic is that the power source for hydraulic can be a small hydraulic power pack which two burly guys can put on the back of a pickup truck themselves, and it will power the equivalent of a 90-lb. air hammer," explains Peter Bigwood, president of Atlas Copco Construction Tools Inc. "These power packs are much lighter, smaller and less expensive than a full blown compressor. The other advantage is that, by the laws of physics, hydraulic power offers the best power-to-weight ratio of any power source when compared to electric, gasoline or pneumatic. You can take a hydraulic paving breaker that weighs about 85 lbs. and it will hit 30 to 40 percent harder than a 90-lb. pneumatic breaker."
Because the vibration created by these tools is so low, operators testing these products sometimes think little demolition is occurring, Bigwood says.
"We now offer the equivalent of a 90-lb. breaker that hits as hard as a 120-lb. breaker would," Bigwood notes. Called the LH40E, it has spring-mounted anti-vibration handles which considerably reduce the vibration felt by the operator. This new machine only throws off 6 meters per second squared of vibration, not too much more than a hand-held electric razor which vibrates at 2.5 meters per second squared. The reduced vibration and the low weight of the power units are causing hand-held hydraulics to gain in popularity compared to pneumatics.
The biggest advantage of the more traditional hand-held pneumatic tools is that they use compressors, which many contractors already own, for power. They include chipping hammers and rivet busters for walls and finish work, cutoff saws, rock drills, which are faster than core drills for setting charges, and breakers. Improvements in these products come from the addition of vibration reducing handles and better mufflers.
Whole building demolition jobs may require the use of rig-mounted attachments, which are put on skid steers or mini and large excavators. They include breakers, crushers, which are used after implosions for taking down large buildings, pulverizers for reducing concrete slabs to rubble, cutters for scrap cutting, shears for cutting steel frames and the universal processor, a combination machine that both cuts and crushes. These rig-mounted tools are highly productive because they can break up much more concrete in the same amount of time than hand held tools, Bigwood noted. Operator comfort is relatively high, as there is less vibration than with hand-held tools and much less noise because the operator works inside an enclosed, air-conditioned cab.
Atlas Copco is introducing the CC1700, a new combi cutter designed to increase worker productivity. Its benefit is how easy and fast it is to change the jaws from crushing to steel cutting, as the process takes only 15 to 20 minutes compared to up to four hours for traditional machines.
More repair materials
While decorative floors can be used in residential restorations, Miller says they are often found only in high-end homes.
tandard residential applications usually involve putting ceramic tile over a wood floor. In this case, contractors must first check for soundness and then use a self-leveling underlayment. This is followed by the use of thinsets, grout and adhesive.
For commercial establishments where a decorative concrete floor is desired, Mapei products range from Ultraplan M20, a midrange product that is popular in large retail establishments as either an underlayment or a wear surface, to Ultratop, a highly durable wear surface product. "With Ultratop, you have the capability to get a very high quality of finish with a virtually crack-free floor," Miller says. "You can diamond polish the product if you want. It acid stains very well. It takes integral color very well. It's a very stable, versatile canvas for anything decorative." The result is a new floor that will have a long, cost- efficient lifecycle.
In addition to products for complete floor resurfacing, there are also patch and repair mortars appropriate for either interior or exterior use. Because they are light gray in color, they blend in well with existing concrete. They set quickly, are durable and easy to use.
Jean Feingold is a Gainesville, Fla.-based writer who frequently covers concrete and other construction-related topics.