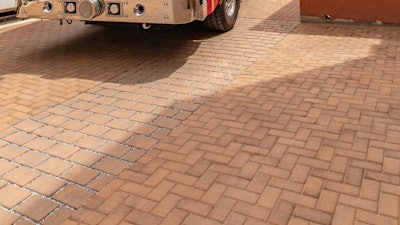
“Our reputation as the leader in the industry has led to some significant partnerships in new product and technology development,” said EP Henry President Eric Long. “This most recent — and perhaps most exciting — partnership with Solidia Technologies, will shift the landscape of the concrete industry.”
Since 2013, the firms have collaborated to integrate the systems into EP Henry’s Wrightstown manufacturing facility. “As the trusted leader in concrete, renowned for driving both market and product innovation, EP Henry was our first choice as the global launch partner for Solidia Cement,” said Solidia Technologies President and CEO Tom Schuler. “We are so grateful that, by sharing their unmatched market knowledge and deep expertise in product and service innovation, EP Henry has helped us make sustainability smart business for cement and concrete.”
Through their combined research and development efforts, the firms demonstrated the many benefits of Solidia Concrete over traditional ordinary Portland cement-based products, including enhanced color vibrancy, the near elimination of primary efflorescence, improved durability, and greater resistance to de-icing salts. The products also gain full strength in 24 hours compared to the 28 days required for traditional steam-cured concrete.
“That Solidia Concrete eliminates efflorescence was my first motivation to explore it,” explained Eric, referring to the whitish deposits common to newer concrete and masonry products. “We have discovered many additional benefits, and we have been pleased with the enthusiastic reception we have received from installers and consumers, who love the product benefits and that their hardscaping projects are helping protect the environment.”
EP Henry’s new pavers and blocks gain their performance advantages as a result of Solidia’s new chemistry, which can be produced at traditional precast concrete manufacturing facilities using standard equipment but with a conversion of curing kilns to CO2. In addition to offering product enhancements, Solidia’s patented processes offer manufacturers considerable energy savings and cost reductions and just-in-time production capabilities, significantly reducing inventory storage requirements. Solidia Concrete products can also be recycled before curing, significantly reducing manufacturing waste.
Today, EP Henry products made with Solidia Concrete are being installed in the Mid-Atlantic and Northeast US. The company is expanding its range of Solidia Concrete product offerings. It plans to convert 50% of the Wrightstown facility to Solidia Concrete production this year, with a full conversion planned for the future. As a result of its conversion to Solidia’s CO2 curing process, within one year, EP Henry will be the largest consumer of CO2 in New Jersey.
“For over 115 years and four generations, our family has sought to make the best quality product for our customers,” said EP Henry’s fourth-generation CEO JC Henry. “Now, with Solidia, we’re making concrete products that are not only better for our customers, but also better for the planet. I have seen the future, and it is Solidia.”