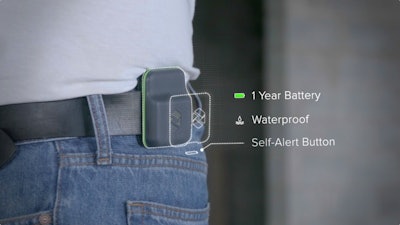
There are ways to track workers and equipment without having to use GPS-based telematic systems.
“There is a tremendous need to bring IOT connectivity to construction to automate data capture from a host of different activities on the site – labor, materials, equipment, tools, buildings, etc.” says Chad Hollingsworth, CEO, Triax Technologies. “The construction site is a really challenging environment because it changes every day. You have a transient workforce. You have materials that are tough to penetrate from a radio frequency standpoint. That is what we really solve with our network technology. It is a proprietary mesh network that can go on site. It requires a minimal amount of hardware. It doesn’t need access to power. It can scale with the job easily. So we have really now enabled connectivity to be deployed on a jobsite and would grow over the life of the job.”
The Equipment Tag is a peel and stick device that you can put on essentially any type of equipment. The Equipment Tag tracks idle time, run time and equipment utilization.
A Jobsite-based Solution
Triax uses a mesh network to track people and equipment on the jobsite. “We don’t use GPS,” explains Hollingsworth. “We only know when one of our sensors is in the site.” But there are advantages to the mesh network approach that are not possible with most GPS telematic systems. “What GPS telematics do really well is track heavy equipment globally.” The challenge on site is when the equipment is used indoors or on multiple floors of a building. “GPS cannot tell you what floor the equipment is on.” You also lose signal strength indoors. The Equipment Tag provides real-time indoor location that allows contractors to view which floor of a building their equipment is located.
Everyone is familiar with the challenges of locating equipment on site. “On our cloud-based dashboard, which you can access anywhere you have a connection to the internet – you phone, tablet or computer – we show where your equipment is on the blueprints or Google Maps,” says Hollingsworth. “We show it on site by floor, within about 10- to 16-ft. of accuracy on the horizontal plane. So I can say there are three scissor lifts on the fourth floor in the East zone.”
The Equipment Tag is a peel and stick device that you can put on essentially any type of equipment. There are several ways to attach it to a machine. You can peel and stick it with adhesive, screw it on or mount it with zip ties. And it is easily transferred between units. “You can move it and assign it to a different piece of equipment on your app,” says Hollingsworth. It only takes seconds. “You simply sign in the piece of equipment you are assigning it too, hit save and then put that tag on the equipment.
The Equipment Tag tracks idle time, run time and equipment utilization. In terms of safety, Spot-R and Equipment Tag link up on the jobsite, allowing contractors to track both employees and equipment. “It can identify that an operator is on the scissor lift on the fifth floor and he is not certified to operate it,” says Hollingsworth. “The system sends an alert to a superintendent or a safety operator on site. It may prevent someone from operating a dangerous, expensive piece of heavy equipment that shouldn’t be. Someone who shouldn’t be operating a piece of equipment probably has a better chance of causing harm to themselves or someone else.”
“What we are really excited about is trying to add another level of safety by ensuring that you have the proper people operating dangerous equipment and also working on reports and analytic tools to show the utilization of your rental fleet,” says Hollingsworth.
“Right now the data that is being recorded is equipment location, when it is being used, the difference between idle and running, or in the case of a scissor lift if it is raise or lowered, and the operator,” notes Hollingsworth. But the company is working to integrate with other platforms producing data on the jobsite. “We are trying to position ourselves as the data provider for your other platforms.” The goal is to provide the data in a form that is easily accessible so you don’t have to look at five different dashboards. “We have an open architecture where we are set up to integrate with other platforms. We see ourselves as being part of the ecosystem that helps collect data on site. But we are not going to recreate the wheel with project management software or payroll or GPS telematics.”