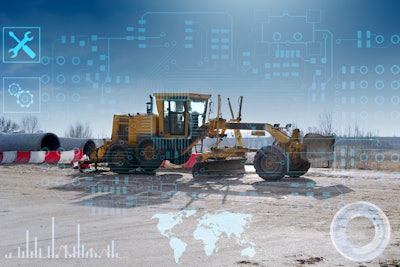
Heavy construction equipment is expensive. As materials and equipment prices have soared in the past year, construction sites have become prime targets for theft. According to the Associated General Contractors of America, “the cost of lumber has increased by 62%, with steel products rising 20% and a 114% rise in the cost of diesel fuel.“
The National Equipment Register estimates the value of construction equipment stolen each year is between $300M to $1B. This estimate doesn’t include tools and building materials. Plus, less than 25% of the stolen equipment is recovered each year. Additional costs associated with stolen equipment include renting equipment to replace what was stolen, lost productivity due to workers not having the equipment to use at a jobsite, schedule delays of a project which can lead to heavy fines, and increased insurance premiums.
What Can Contractors Do to Deter Crime?
Jed Hudson of S. T. Wooten, a construction services and materials company, discovered one of its broom tractors had been stolen from a jobsite. According to the LoJack Corporation’s report on construction equipment theft, wheeled and tracked equipment, like the broom tractor, is the most common equipment stolen. The broom tractor was equipped with telematics GPS hardware from HCSS.
Once the unit’s location was identified and it was determined that the tractor had not moved in several hours, S.T. Wooten and police authorities recovered the equipment in a matter of minutes. HCSS Telematics helped find the stolen equipment. Once police were contacted, the HCSS Helpline was called with the equipment code and GPS serial number. HCSS was able to reprogram the GPS unit remotely to ping every minute whether the ignition was on or off. If the equipment status was to change, automatic alerts would be sent to the equipment owner via phone, text, or email. The equipment was located and recovered quickly.
Tracking Assets with GPS Telematics Equipment
GPS and Telematics devices help contractors track equipment more easily. You can know that you have the right tools for the job at the right location at the right time. You can visibility into your asset locations, while deterring theft. These tracking devices can also be used to track equipment utilization, manage preventative maintenance, and accurately charge costs to each job.
One contractor has several divisions that share equipment, and the divisions rent equipment from each other whenever possible instead of using a rental company to fulfill resource needs. While this saves on rental fees, the company wasn’t getting an accurate idea of how many hours equipment was being used. Using GPS hardware and telematics software, the company can manage equipment across multiple states.
Telematics has helped create a preventative maintenance program as well. GPS data feeds into a preventative maintenance program so managers are aware of machine’s upcoming service. A mechanics can be dispatched accordingly to cut down on maintenance costs.
Telematics equipment also helps the company manage utilization and track job costs. Project managers input employee and resource hours, which is then fed into the company’s accounting system, where the accounting department pays out employees but also charges equipment to the correct job. Field engineers and project managers get instantaneous costs to the job because the company has calculated hourly rates of what the equipment costs. These engineers and managers can get real-time job costing data to monitor how much the equipment is costing them. Project managers run reports to compare what the GPS units have reported to true up discrepancies.
Telematics equipment and software often has a geofence feature where contractors can set up markers around the jobsite to know when equipment is entering and leaving the site. The geofences tie into weekly reports to help the company true up equipment time. Geofences also work retroactively so you can tell if a piece of equipment was within that area in the past. One contractor was told by a local gas station that one of his trucks fueled up and didn’t pay for the gas. The company was able to put a geofence on the gas station and go back in time to verify if their truck was there or not. Turns out, the driver was there but his credit card wasn’t working, so he went inside the station to pay for gas. He thought his card had been scanned, so he took off after fueling.
With telematics equipment project managers can see what equipment is being used and what is not. If a piece of equipment is underutilized, perhaps the company doesn’t need as many of that expensive equipment as they thought. Machine cost is associated with utilization versus spending a lot on equipment the company is not using. The data gathered from the telematics devices is truly valuable.
How to Select GPS Technology for your Construction Business
Construction equipment tracking software and hardware solutions track assets and send telematics data to other management software so you can be alerted to any potential fleet issues before they become problems. You can send telematics data to other software solutions to help catch errors, reduce double entry, and even receive meter readings directly from your machines to automate your fleet’s preventive maintenance cycles.
Many over-the-road units are certified to be ELD compliant so they can be used in fleets to track mileage and driver behavior data. Plug-and-play units can be used in fleet vehicles, heavy trucks, and yellow-iron. For non-powered assets, such as trailers, solar and battery-powered satellite asset trackers are available. GPS information can give a company a competitive advantage by providing more accurate ETAs to customers.
To select the right GPS equipment for your business, first understand the goals you want to reach by using this equipment. Do you want to lower fuel usage? Do you want to improve customer satisfaction? Do you need to improve preventative maintenance processes? Do you need to monitor your drivers? Do you need to keep track of assets at the jobsite? Have there been numerous thefts at your jobsites and you need to track the equipment?
Next, look at how you will connect the GPS or telematics device to your equipment. Will you use Bluetooth? Cellular Data? Will the device be hardwired into your equipment?
Do you want the telematics equipment to send you alerts for: accidents, poor driving, maintenance, out-of-range, or other?
Many companies provide a variety of telematics/GPS service agreements all the way up to 24/7/365 coverage. Look at what you need for your company, including the time it takes for the vendor to return your service call.
Using telematics devices and software in your business can be a real game-changer. The Aberdeen Research Group reports that businesses that use telematics solutions report a 46% increase in on-time arrivals and a 13.2% decrease in fuel costs.