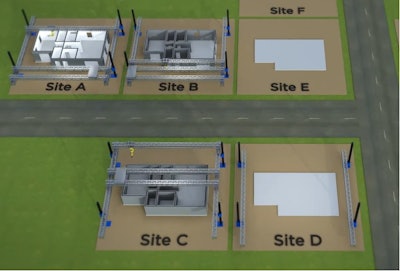
3D printing of concrete structures including homes has made a dent in the news, but less so when it comes to penetrating the market for new homes or commercial structures.
Barriers to progress for this technology, which proponents claim could make housing more affordable and available, include:
- A lack of ability of companies to secure patents—one such company has refused to brief ForConstructionPros to shield trade secrets that are not yet protectable and others have not responded to queries
- Proprietary mixes that require engineered aggregate materials
- Building code requirements that throw up local delays to project approval
- A lack of commercially-available 3D concrete printing machinery
Yesterday, Phoenix-based Diamond Age announced $50 million in venture capital funding for its integrated building automation building system that addresses building code issues by basing its technology on the existing code for stack masonry construction. The company’s tech augments 3D concrete printing with robotic features that cut wall openings, level cut concrete surfaces, install electrical and mechanicals and other labor-intensive steps in the home building process.
The series A round was led by Jackson Hole, WY-based Prime Movers Lab. Seed investors Alpaca VC, Dolby Family Ventures, Timber Grove Ventures, and Gaingels all invested above their pro-rata and are joined by Signia Venture Partners. Additionally, 20 percent of the round came from Diamond Age customers, including production home builders and land developers. The company received $8 million in seed funding in August of 2021.
Cracking the 3D Concrete Building Code
On a call with ForConstructionPros the day after the funding round announcement, Diamond Age Co-Founder and CEO Jack Oslan outlined how the company built its tech stack around compliance with the International Building Code for dry-stack masonry, which is already recognized widely by municipalities that will need to approve projects built by Diamond Age. UL has created its UL 3401 standard for 3D printing equipment, fabrication processes, additive manufacturing materials, quality control procedures and production records. The International Code Council ICC Evaluation Service has similarly created its ICC-ES AC509 standard for 3D Automated Construction Technology for 3D Concrete Walls. Diamond Age is taking an end run around both, opting to align with technologies with a long track record of performance and commonly allowed for in municipal codes. Approval by these bodies can help a new building technology win regulatory approval in a jurisdiction where contractors propose deploying it, but Oslan points out that dry-stack masonry is already a known quantity.
“The portion of the building code we modeled after is dry-stack masonry,” Oslan said. “We are also using post-tensioning system found in any big box warehouse and have created a composite wall system that has been undergoing third party engineering certifications for the past year and will continue to go through all the engineering standard reviews to receive a performance engineering certification and a P.E. stamp for submission into the International Code Council. We will be able to prove our structures are safe.”
Unlike other 3D concrete printing technologies, Diamond Age does not extrude concrete as a continuous pour. Rather, they lay down a single layer at a time the length of a wall section that in essence behaves like a continuous, wall-length masonry brick. The weight of layers upon each other and the post-tensioning system means each layer does not need to chemically adhere to the ones above and below.
“We have a patent around the composite wall system that is already crushing the standards for wind loading and water intrusion,” Oslan said. “We are super excited to be able to present that data to building departments. We have a patent around the extrusion process—we do this very differently from all the other people 3D printing in concrete. They are trying to take a desktop Makerbot and scale it up. If you look at the way desktop 3D printers work, they heat up material and then rely on a mechanical hardening process. Concrete is a chemical curing process. The idea is that you can 3D-print continuously and bond structures to have the same strength as a single pour. We figured we would approach this as dry-stack masonry and engineered the wall system to account for that.”
The code for dry-stack masonry allows Diamond Age to build structures up to three stories, but this is well beyond their goal of focusing on the starter home market.
“We can print up to a 2,000-square foot single story house,” Oslan said, adding that they are capable of building a two-story home of up to 3,600 square feet. “One of our early customers is exclusively building two story homes—we are getting certified for that, working with third party engineering firm for projects across the United States.”
The company’s gantry-based technology can also reach below grade to pour basements.
“Sure, we can build basements,” Oslan said. “With our gantry system itself, the limitation is when we build the roof.”
Diamond Age does not rely on highly-engineered materials for its concrete extrusion process, and is rather designed around bag cement from Home Depot and half-inch aggregate, commonly available through any local quarry.
“Our mix design is such that we are extruding a 2.5-inch square brick,” Oslan said, stressing that the goal was to ensure materials were readily available while meeting performance requirements. “Our mix design has zero slump … 1 to 3 percent shrinkage but zero slump. That 2.5-inch height means we are printing two and a half times the layer of other 3d printers.”
Automated Mechanicals Installation
The Diamond Age technology extends well beyond concrete extrusion however, and includes a series of tools attached to its overhead gantry to in essence deliver a manufacturing execution system that installs electrical conduit, wiring and mechanicals, cuts windows and doors, level-cuts the wall tops to accept roof trusses and more.
Oslan credits Diamond Age CTO and Co-Founder Russell Varone and his experience and network of engineering talent with experience at Tesla with driving the tech-forward approach that essential creates a modern, automated factory on a job site.
The system is built around seven automation systems referred to as cohorts that will eventually support 26 different automated tool sets—tool sets involved in initial stages of construction are currently released to market and patented while others are developed but not yet released. The cohorts are set up sequentially, completing one phase of a structure before moving to the next structure in a multi-structure development project.
“If you think about the way electrical and plumbing go in with PEX and Romex, we do it the same way,” Oslan said. “But we have the robotic system that is able to reach that down into the wall and pay it out—taking material off a roll, counting the inches and length, and knowing how far it has to get to and then leaving a pig tail that can be attached to a two-gang or four-gang box. People come in later and do the connections. It is in the wall vertically instead of horizontally. And we might use a bit of extra material. But the labor savings and taking low-value work off high-value people makes up for that.”
This automation though requires a significant number of structures in a single geographic area to deliver the efficiencies of automation.
“We don’t deploy a cohort for less than 150 homes,” Oslan said. “That is six months worth of work. For us to pack up the circus and come to town, we want to be on site for probably six months. The development we are starting in, our first project that we break ground on here in April of this year, is over 200 homes.”
Oslan said the company does not plan to license or sell their technology, but rather use it to deliver projects for commercial developers.
3D Concrete Printers for Sale
Other companies do in fact, however, sell the 3D concrete printing tech commercially.
Midvale, Utah-based MudBots is currently seeking regional distributors for its printers, which range from 15-foot by 15-foot by 10-foot high to 100-foot by 50-foot by 10-foot high. COBOD markets is BOD2 printer, which ranges from 14.86 feet feet by 145.92 feet by 10 feet high to 39.69 feet by meters by 81.2 feet feet by 26 feet high.
Black Buffalo 3D Corporation launched its production-ready NEXCON 1G printer at the National Association of Home Builders (NAHB) International Builders Show in February.
Black Buffalo 3D
“We just feel the only way it scales beyond really successful fund raising is to commercialize it,” Big Sun Holdings Group Head of Marketing and Strategy Peter Cooperman said. Big Sun, a member of HN Inc. formerly called the Hyundai BS&C Co. Ltd family of companies, is Black Buffalo 3D's parent company. “I will be on stage with a lot of our customers in the coming months that are going to be announcing doing hundreds of homes. But we will also use what we are talking about to 3D-print as much of our new factory as possible—some of it will be printed tilt-up walls and some printed in place, and we hope to be zoned so our customers can print some homes and sample properties on a recently-purchased parcel in Pennsylvania.”
Cooperman said the company is currently building eight machines per month, with most assembly taking place at a facility in South Korea and in Elizabethtown, N.J. The factory to be built in Pennsylvania will help them scale even further.
Engineered Concrete for 3D Printing
Unlike Diamond Age, Black Buffalo 3D does rely on a proprietary mix for its extrusion process.
“I think we are the first that invested extremely heavily in the materials—and this is an area that needs some standardization across the industry,” Cooperman said. “We have spent tons of time and money while developing the material with our partner, Mapei.”
Black Buffalo’s printing technology uses a proprietary cement-based ink that cures to over 7,000 PSI in 14 days. Mapei will distribute the product in the Americas, but because Black Buffalo 3D owns the IP, they will be able to license ink manufacture in regions of the world Mapei may not have distribution.
“We started with a very good mix from our R&D team in South Korea, and spent the past year and a half improving it to meet the strictest standards for safety, consistency and performance that is being verified by ICC-ES and Intertek,” Cooperman said. “The shrinkage requirement was hardest to meet. We are also working on a bio-friendly ink, and looking at hemp-based materials to replace some of the components of our traditional ink mix.”
The material and printing method were certified under ICC AC 509 in 2020 for wall heights of up to eight feet, and then Black Buffalo worked with ICC to revise the standard to allow for multi-story printing to meet their maximum print height of four stories and future proof the standard.
“We spent a year doing sheer tests, compression testing, determining how the structure holds up in an earthquake, how do you need to prepare the wall—going through that with ICC and (construction product testing firm) Intertek … When it comes to getting coding or zoning approval, we can hand over some legit, scientific material.”
Printers shipping now
Black Buffalo 3D's gantry-based printer is fully modular design and has a max print height or 26 feet.
“It is commercially available right now,” Cooperman said. “We are selling them, and working on financing and leasing programs. Our business revolves around increasing adoption of 3D construction technology and we want to make NEXCON printers available for trial projects to prove why our material and machines are best. We see the leasing element as critical to giving builders a chance to test the technology and experience the benefits first-hand.”