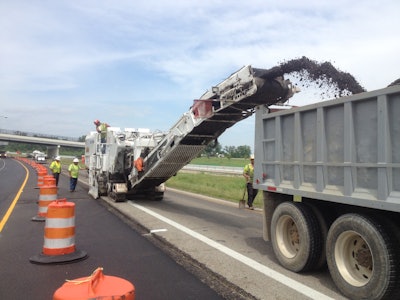
The road construction market is dynamic. It continues to evolve and change due to technology.
Technology has become interwoven into the means of production and how road construction businesses are run. What technology has done is provide valuable information … real-time information, which allows for better decisions to be made. Access to information benefits the road construction contractor in all areas from the heavy-equipment operator to the site superintendent to the business owner. Large amounts of data can be filtered and selectively used by individuals in their jobs to help them be more effective, productive, and accountable.
Telematics currently offers contractors the ability to monitor where their fleet of equipment is currently located, which machines are running, and the level of productivity being achieved. With GPS and 3-D digital site models, machines can grade, compact, mill, and pave with astounding accuracies. Machines can “tell” owners when it’s time for scheduled maintenance and diagnose the cause of mechanical and hydraulic issues.
It’s in this area of diagnostic software where cutting edge developments are occurring. Remote diagnostics can provide real time data which can address a contractor’s worse nightmare: a stalled machine.
“We've developed a custom remote diagnostic system for our machines that can address a problem and correct it to maintain the contractor’s productivity,” states Max Peters, Guardian account manager with Roadtec. “Our system consists of software, on-machine viewing screens, and wireless signal boosters to send and receive data from the machine.”
Information access
Numerous functions such as engine data and fuel consumption can be viewed at the machine or on your computer screen from a remote location.
With telematics, construction contractors have access to engine information … a lot of data that can make certain the machine’s engine keeps operating efficiently. The data can tell company personnel if an engine is faltering, how much fuel is being burned, if the engine is idle, how long it’s been idling, and where the engine, i.e., the machine, is located.
With the emergence of telematics, contractors are experiencing the benefits of technology. Fleet management can help track assets and save time when a need emerges for a piece of heavy equipment that may be sitting idle on the other side of a jobsite or at another location.
Engine diagnostics can prevent costly workflow slow downs or stoppages. A machine that’s dead on the site can not only impair the workflow but endanger a contractor’s timetable. Missing a deadline can incur penalties and affect the contractor’s ability to move quickly on to other jobs and opportunities.
The engine diagnostics feature of telematics has certainly helped contractors meet the demands of today’s expectations for shorter completion deadlines and slimmer margins. There is little room for errors.
There is a flaw in the most current evolution of the telematics engine diagnostics picture: the tremendous amount of data and benefits are there, if the engine is running. What happens when the engine has stopped?
The Roadtec Guardian Telematics System has the ability to show why the engine will not start.
“We’ve taken the next logical step with telematics and can diagnose why a machine’s engine has stopped,” Peters says. “Telematics can tell the contractor that the engine has stopped, where Guardian tells why.”
This technology innovation promises to address the following:
- Show why the engine won’t start, such as a failed neutral switch on a propel joystick or possibly an E-Stop that isn’t activated because a wire is loose. Or perhaps a circuit breaker didn’t “pop,” but failed internally. Additionally, the contractor will be able to see what the battery voltage is when trying to crank the engine.
- Provide a visual guide — Live Schematics — so the machine operator, technician, or machine owner can see where the voltage path stops in the circuit under test.
- Create customized fault codes for the machine, not just the engine. With this advance, a contractor can be notified when a steering or grade sensor fails. And receive warnings when hydraulic pressures or temperatures are out of spec.
- Educate a new technician who is not familiar with the circuit/system by guiding them directly to the problem.
- Provide access to engine operating data in real time with fault code reporting. The fault codes are decoded and provide the fault description in text, not just an SPN number.
Clearly, the ability to troubleshoot and know why an engine has stopped can help technicians be better prepared to repair and restore a machine back to productivity. The Guardian Telematics System is geared toward increasing jobsite productivity and up-time for business owners, and clearly reflect a continued evolution of the benefits of technology in construction today.
Less machine downtime
The Guardian system consists of software, on-machine viewing screens and wireless signal boosters to send and receive data at the machine. Numerous functions such as engine data and fuel consumption can be viewed at the machine, on the owner’s computer screen from a remote location, and by Roadtec support.
“Let me give you an example of the benefits of having a contractor’s machine connected to Roadtec support via Guardian,” states Peters. “Our support center received a notice from a milling machine working in Florida reporting that the signal from the left front pulse pickup was lost. A pulse pickup monitors the speed of the hydraulic motors that drive the tracks. On this particular machine, the left front track pulse pickup value showed zero and all other track pulse pickup values were normal.
"An engineer at Roadtec logged into that machine in Florida and confirmed the condition," he continues. "The engineer called the owner of the milling machine and told them, and the customer quickly found a broken wire. The problem was corrected within 30 minutes of the time Roadtec received the notice.”
It's possible to monitor and troubleshoot everything from the machine’s fuel consumption to engine codes; starting circuits to cutter circuits; and the machine’s propel functions, load controls, hydraulics, steering circuits, and grade and slope settings. Everything can be seen instantly, even the exact location of the machine via GPS.
Help from Roadtec service is only a phone call away. With Guardian, Roadtec technicians are available 24/7. The support staff technicians can see the same machine circuits and systems as live schematics that the contractor sees and can guide them through a fix or do it for them remotely.
Telematics is helping milling and paving customers stay ahead of the technology evolution occurring in road construction today. The Guardian Telematics System appears to offer one option in the telematics area that can help contractors control production, monitor progress, be alerted to any problems, and help manage the machine, the project, and their business.