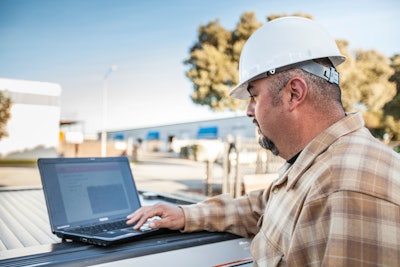
Technology either evolves or gets left behind. In the underground construction industry, evolution most often correlates to improved efficiency and ROI. As the industry has grown, these goals have become even more important, leading contractors and equipment owners to demand more from their equipment. Many technological advances can be found in the operation and functionality of the machines themselves, but equipment manufacturers have also been stepping up their game in the ever-changing world of telematics and fleet management.
What started with simple GPS location technology being used to track equipment and aid in theft prevention and recovery has led to equipment owners and fleet managers being able to centralize their machine and fleet information. In addition to location information, telemetry data is available for engine hours, fuel usage and diagnostic information to assist in service and planned maintenance, among other options. While it varies by manufacturer, generally speaking, machines equipped with telematics can offer machine owners as much information as they need to make informed decisions about their operation.
The overarching goal of telematics is to empower equipment owners to increase the profitability of their business. Contractors can monitor their fleet’s performance and jobsite history to improve overall business profitability and effectiveness on and off the jobsite. Data is available 24/7 via any mobile device to help underground construction contractors work smarter and gain valuable machine insights anytime, anywhere.
Telematics can help you see if a drill is being misused or overused, as well as track wearable and service parts to understand how quickly crews are going through drilling bits or digging chains.
Through comprehensive reporting capabilities, operators have the power to track individual machine indicators, including working and idle hours, which enables them to schedule routine maintenance. The technical data provided in each machine can illuminate potential problems before they occur, such as keeping an eye on fuel and DEF levels, battery performance and other vital systems. As more information is collected and analyzed, the smarter and more efficient the industry will get.
Contractors can see if a drill is being misused or overused. They can begin to track wearable and service parts to understand how quickly crews are going through drilling bits or digging chains. They can see how long the engine has been idling. These machine insights can assist in bidding for jobs and ensuring contractors are gaining the most ROI on their equipment.
Check with your local dealer to see how this information could help your business.