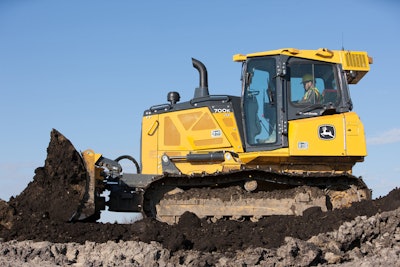
Inertial Measurement Unit (IMU) technology uses accelerometers and gyros to measure change in any direction in three axis: roll, pitch and yaw. It can perform this task much faster than slope sensors on traditional GPS-based grade control systems.
“With traditional GPS [grade control], you are processing at 10 to 20 Hz, 10 to 20 times per second,” says Murray Lodge, senior vice president and general manager, Construction Business Unit, Topcon Positioning Systems. The IMU technology can operate at speeds up to 100 Hz. “This is five to 10 times faster than any traditional machine control using GNSS.”
This faster reaction time translates into greater accuracy and grading speeds since it can rapidly correct any deviations. But in order to use this speed for optimum performance, the system needs to know the exact blade position at all times. With a single IMU on the blade, it can be a challenge to understand whether a machine is turning or the blade is rotated.
To increase precision, Topcon has developed Dynamic Performance, a dual IMU system that mounts one IMU on the blade and another on the dozer body. “Dynamic Performance knows at all times the difference in relationship between those two pieces of the dozer,” says Lodge. “It has a reference to where the blade is, whether it is straight or whether it is rotated.”
Dynamic Performance dual IMU technology has been integrated into Topcon’s 3D-MC2 grade control solution to create 3D-MCmax. “Topcon 3D-MCmax is maximum performance in all applications, whether that is crowns, steep slopes or tight turns,” says Lodge. “Essentially, you have a dozer that you can now use in all applications at the speeds you want for the most productivity.”
[VIDEO] How Topcon's 3D-MC MAX Improves Dozer Speed, Control and Performance
A Change for the Better
Dual mast systems have been used in the past to establish exact blade position. “Traditionally, you had to have GPS on the blade so that if it rotated, you knew there was rotation,” says Lodge. The IMU simplifies the entire system. “You don’t have to add any additional sensors or technology. The IMU can monitor all of it.”
The most obvious change with Dynamic Performance technology is no more masts on the blade. Instead, single or dual GPS antennas (depending on the application) are relocated to the top of the cab. This makes it possible to track productivity. “Now that I put the antennas on top of the machine, I am always measuring to the tracks,” says Lodge. That eliminates the errors on the cut/fill mapping if the blade is on the ground or lifted. The result is more accurate production data.
[Video] Topcon 3D-MC MAX Integrated “Mastless” Dozer System
It also means less risk to the operators and sensitive equipment. Historically, installation of receivers on traditional masts posed many challenges, with operators having to crawl up and down on the blade. “Climbing up and down, trying to put that GPS out on top of the blade — it did not matter if it was one mast or two, all that did was make it more difficult,” says Lodge. Integrating the antenna into the cab totally eliminates this task.
Getting sensitive equipment off the blade takes it out of harm’s way, as well. “That is where the most damage is done,” says Lodge. With the mast systems, many customers would simply leave the systems installed all year long. “You see expensive components sitting out there because customers just don’t want to take them off. It is too time consuming or, especially in cold weather, difficult.”
The 3D-MCmax system allows sensitive equipment to be relocated to the cab, providing protection against both damage and theft. “Now you look at [the machine] and you cannot tell,” says Lodge. “Everything on this machine looks like it is a normal dozer — all protected.”
Another proposed advantage of the 3D-MCmax is the ability to minimize the amount of equipment on the jobsite due to the enhanced fine grading capability. “Traditionally, a dozer was always out there to rough grade,” notes Lodge. “When it came time to finish, you had to bring in the motor grader. But with a dozer today, you can bulk the material around, balance the material and fine grade. That was not an option in the past. Many times, motor graders are not even necessary.”
Deere Dozer Gets Smart
John Deere’s new 700K SmartGrade dozer builds on Topcon’s dual IMU technology to offer a fully integrated grade control solution. Deere & Company worked closely with Topcon to develop this proprietary solution for its dozer line.
“We are now using a dual inertia measurement solution,” says Liz Quinn, product marketing manager, John Deere Worksite. “It is fully integrated and the machine software is actually talking to the 3D-MC2 software, as well as the inertial measurement unit firmware. So the complete solution is integrated and we will be able to create new features as a result of that integration.”
One new feature already unveiled is Auto Smart Grade. Typically, aftermarket grade control systems are used for the final few passes to get to finish grade. “With Auto Smart Grade, you can actually use it earlier in the earthmoving cycle. In cutting, where you may have 2 or 3 ft. of earth to move, it provides a gradual start rather than going right to grade,” Quinn explains. “[This] is especially helpful for new operators. It leverages the benefits of the automation earlier in the earthmoving cycle than they were able to do with an aftermarket kit.”
The idea is to balance the load on the blade with the tractive power of the dozer. “In cutting applications where you are moving a whole lot of dirt at the beginning of a job, a new operator is going to load up the blade as much as he can,” says Quinn. “We find that sometimes they slip the tracks. Sometimes the engine lugs down. Not with Auto Smart Grade. It is going to detect before those tracks slip. It is automatically going to raise the blade just enough to get that machine over the hump so the operator is not backing up a big mound of dirt; it is a nice slope.”
The monitor is the key to setup and tuning for the particular jobsite. “We are able to dial in the performance of this feature by easy to use icons,” says Quinn. “First, you are going to set how much load level the operator is expecting on the job that day.” Then you set the type of material — hard clay, loose sand. “In essence, we are fine tuning this machine to get the most dirt moved with every pass it takes, without excessive track slippage and wear and tear. The machine knows how much load it can take and it is going to take as much as it can before it automatically raises the blade.”
John Deere has also realized increased accuracy with its 700K SmartGrade dozer. “In road building, where accuracy is paramount, our tests have shown the IMU sensor solution was more accurate than the aftermarket solution,” says Quinn.
One reason is the elimination of the mast. When the receiver is mounted on top of a 10-ft. mast, it can cause some unwanted movement. Integrated components result in a more robust solution.
“The monitor has been completely integrated into the cab,” says Quinn. “In the aftermarket solution, you have masts and cables that are very vulnerable to damage on the blade. We have removed all of that and we are protecting those IMUs by John Deere steel behind the blade and under the chassis. Should anything go wrong or need to be looked at, they are very easily accessible.”
Tying the new system to the existing telematics capability allows customers to immediately identify if the system is working properly. “We have connected all of the different components to JDLink, the telematics infrastructure,” says Quinn. “We understand if things are connecting to the base station like they should be.”
Integration has also allowed simplified machine controls. Increment and decrement controls have been integrated into buttons on the control levers. This allows the operator to easily raise or lower the actual grade above or below the target grade without having to go through the monitor.
Moving forward, SmartGrade will serve as a building block technology that will be adapted to future products. “This summer, we plan to introduce the 750K and 850K with the SmartGrade option,” says Quinn. “Really, this is the building block of future automation.”