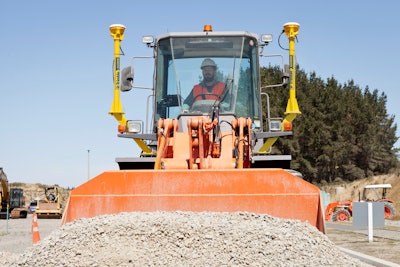
Machine grade control technology has evolved to allow faster speeds and tighter accuracy, as well as more machine forms including dozers, motor graders, excavators and wheel loaders. Various solutions currently exist that address unique jobsite challenges and required tolerances.
“Quality, functionality and price go hand in hand,” says Morten Nissen, product specialist, grading solutions, Leica Geosystems. “As both new hardware and more sophisticated software are being continuously added to high-end 3D solutions, their costs have risen. But at the same time, [they offer] faster return on investment through productivity and prevention of costly mistakes. As the technology develops, contractors are offered an increased number of choices between systems of different functionalities and prices.”
According to Jeff Drake, business area manager for machine control systems at Trimble, “A lot of the advancements that you will see in the coming years will be addressing the shortage of qualified operators.”
Komatsu's integrated dozer technology allows the dozer to run in full automatic mode from the first pass rough cut through to finish grade.
Manufacturers of 3D systems have worked to ensure a fast learning curve. “We spent almost two years in front of operators making sure that the user interface [Trimble] put in front of the operator is very simple to use,” says Drake. It is an Android-based platform that simulates the operation of most smartphones.
Robotic Total Stations vs. GNSS Solutions
Robotic total stations and GNSS solutions are the primary 3D grade control technologies. They require a 3D design model that is loaded into the grade control system’s display.
“That terrain model is what our system is referencing from a guidance perspective,” explains Drake. “We take incoming blade or bucket positions computed from the GPS or robotic total station and difference that with what our 3D design model says and create a cut or fill value to guide that blade to the right elevation.”
The basic components of a 3D machine grade control system include either a single, dual or twin antenna receiver; a base station or robotic total station; machine sensors; a control box; and cables and brackets connecting components.
In the case of a GNSS solution, the positioning signal utilized to run the system is broadcast from satellites orbiting the Earth. Accuracy is affected by satellite geometry, signal blockage, atmospheric conditions and receiver design.
To make this signal useful for most earthmoving applications, the accuracy needs to much more precise. This is where the base station enters the picture. A base station is set up on a precisely known surveyed point. This allows it to determine the error and broadcast a correction across the jobsite to all the machine receivers.
In some areas, the base station is not needed because these systems can use corrections from a local Virtual Reference Station network, or VRS. Anyone within reach of the VRS network can get positioning information using a cellular connection. But unless you are certain of the quality of the cellular correction signal or corrections from the local VRS, you may want to stick with a base station.
“It is becoming more common to get corrections via a cellular link,” says Drake. Yet, there are quality considerations. “If a contractor wants to have that reliability — that 100% uptime of the correction service — then most of the time they should think about putting their own GPS base station on the project. They are in control of the quality behind the setup.
“We have seen contractors increasingly using VRS corrections to increase the speed at which they can get machines into the field,” he continues. However, the ability to use a VRS is dependent on whether there is a network available in your area; you have reliable information that the network is maintained by a professional organization such as a Department of Transportation; and whether corrections are available 24/7.
GNSS systems typically need an unobstructed view to the sky in order to receive satellite signals. “Customers should also be aware that GNSS will typically only give you centimeter level accuracy over your grading area,” says Drake.
The systems allow you to work in a much larger area and work multiple machines. “But if you have a need for higher accuracy, then you would need a different technology,” Drake states, adding, “Trimble offers the positioning technology for every excavation and grading application.”
GNSS accuracy has improved over the years, and there are now multiple satellite systems available, Drake points out. They include GPS, GLONASS, Galileo and BeiDou. More satellites translate into better positioning and system uptime.
Topcon 3D-MCmax allows the operator to see a true representation of the dozer on its GX-55 display. The dozer’s position and blade angle are correctly represented on the screen, giving the operator comfort of knowing where the machine is in tight spaces.
“We have laser-augmented GPS, where a laser receiver is mounted on the blade and a GPS receiver sits on top of that laser receiver,” says Drake. “We augment that vertical performance of GPS with the laser vertical position and get within millimeters using laser, but it is still getting the horizontal coverage using GPS. That is a great way to extend your working area while still getting millimeter vertical accuracy.”
Yet, there are applications where you might not have visibility to the sky and will need a different solution such as robotic total stations. Unlike a GNSS solution, working in urban environments with limited visibility to the sky, canyons or inside structures such as tunnels or buildings does not restrict use of robotic total station technology. The technology is very precise, typically in the 3- to 5mm range.
“You might need a robotic total station solution if you are looking for 100% uptime in your grading solution,” says Drake.
A limitation is that robotic total stations typically require a separate total station for each machine to be controlled. They can also offer a limited working range. “However, we have produced a method by which you can have multiple total stations tracking one machine to extend the range,” says Drake. “Or you can have multiple total stations with a station tracking one machine and a second total station tracking another machine. Or you can hand off use of the second total station from the second machine to the first machine to increase the working range of that first machine.
“There are interesting ways we have implemented the total station handling of multiple assets in the field to increase the working range or get multiple machines using the total stations on the job,” he adds.
There are solutions for customers who need both total station and GNSS technologies due to changing jobsite conditions. “Knowing this can prompt our dealers to offer external radios such as the Topcon MC-i4, which would accommodate machines needing both connectivity to a total station as well as connectivity to a base station for GNSS corrections,” says Fred Beachner, product manager for machine control, Topcon.
Machine Selection
The 3D machine grade control systems can be added to almost any machine. If the aftermarket install is done correctly, most GPS system suppliers claim there is no noticeable difference in accuracy between factory pre-wired and other machines.
“There are makes and models that are more easily adapted to this technology,” confirms Beachner. “Since the John Deere IGC (integrated grade control) dozers and graders became available, and since we were able to develop a VSU (valve switch unit) for Cat machines that utilize CAN (Controller Area Network) communication with Cat, we and our customers have found it profoundly easier to adapt this technology on the later model machines.”
“There are big advantages with installing on machines that are prepared for machine control,” says Nissen. “Most machines with machine control as an option have been tested with regards to response time and accurate movement to guarantee the optimal performance. We can encounter machines that are no longer in production and are not built for fast and accurate movements, and therefore are not the best choice for machine control.”
A limiting factor for 3D machine control is often the machine’s hydraulic system. “Machine control technology is able to measure faster than the machine is capable of moving. Therefore, our maximum efficiency will never be faster than the fastest physical speed of the machine,” says Nissen.
For example, Topcon’s System 5 consisted of a GNSS antenna(s) mounted above the cutting edge, a standard slope sensor, MC-R3 controller and in-cab display box. “With System 5, the operator was finally able to have a constant reference to grade no matter where he was within the boundaries of the model,” says Beachner. Material only got moved to where it needed to go, resulting in fuel savings and decreased survey costs.
Then Topcon 3D-MC2 was introduced. Its MC2 IMU (Inertial Measurement Unit) sensor meant dozers could grade at high speeds with more accuracy. The sensor could also be installed on graders for improved grading stability and, when used in conjunction with the Millimeter GPS system, could provide very tight accuracy.
Next came the 3D-MC MAX dozer system. “Topcon took the GNSS antenna from the pole mounted above the cutting edge and placed it on top of the cab,” says Beachner. “This was made possible by developing an even better IMU, the MC2+ sensor.”
[VIDEO] Topcon 3D-MC MAX Integrated “Mastless” Dozer System
Topcon placed two sensors on the machine: one on the body and one on the blade. This system increased accuracy and dozing speed even further, and ensured that same speed and accuracy through turns. “3D-MC MAX also allows the operator to see a true representation of the dozer on the GX-55 display,” Beachner notes. The dozer’s position and blade angle are correctly represented on the screen, giving the operator the comfort of knowing where the machine is in tight spaces.
Instead of relying on aftermarket installations, some manufacturers, such as Komatsu, are integrating grade control technology with the base machine controls. “Machine control systems must be able to coordinate with the base machine to understand blade loads and track slip. This allows for a tailored response, given certain parameters on the base machine in relation to the automated blade control. This communication is something that only exists on factory integrated-type solutions,” says Anetsberger.
With the integrated machine solutions, all of the components communicate with each other. For instance, consider the Komatsu Intelligent Dozers. “Since the grade control is tied into the base machine, it can sense the load on the blade [and] the load on the drivetrain,” says Anetsberger. “We know the maximum load our machines can push. We can set parameters so that when the blade load increases to a maximum, we can raise the blade accordingly to minimize any track slip that may occur.
“If the track slip is low, the load is low and we are still above grade,” he adds, “the system is smart enough to lower that blade to work its way down to the target elevation.”
This integrated dozer technology allows the dozer to run in full automatic mode from first pass rough cut to finish grade. The dozer automatically pushes the optimum amount of material in each pass.
“It all trickles down to productivity, fuel savings and ultimately return on investment,” says Sebastian Witkowski, product marketing manager, Intelligent Machine Control, Komatsu America. “You are not wasting time spinning tracks. You are not moving dirt twice. There is no guessing. You always know where you are.”
Telemetry Changes the Game
“Telematics solutions are one of the main reasons to use machine control,” says Nissen. “[Telematics] are already an integrated part of 3D solutions.”
Among the benefits:
- Visualize and validate data used and generated on site in 2D and 3D localized on interactive maps to collaborate and communicate with everyone on site
- Share updates and corrections to reference model data in real time across the project to guarantee transparency and quick reaction to design updates
- Convert formats to integrate third-party platforms, increase connectivity and integrate existing workflows
- Monitor machine control operations remotely by assigning work and providing positioning and reference data to operators and grade checkers, ensuring you avoid costly rework and errors
- Report productivity for the work that has been performed to validate what work has been completed and that the results are to specification
Telemetry provides production data in real time so contractors can make timely adjustments.
“On projects where the design changes frequently, getting that design out to the machines quickly can mean that a machine does not build to the wrong elevation at the end of the day,” he adds.
Telemetry also provides production data in real time so contractors can make timely adjustments. Traditionally, tracking this data was a labor-intensive process that involved sending surveyors out to do a topographical survey, with the results often being at least a week out of date.
“Now you have the ability for 3D grade control to measure that rate of production and get that over the air,” notes Drake. “Back-office systems are performing calculations in near real time. It gives the contractor a real-time view to make important decisions about the progress on that job and make changes more frequently than how they were conventionally able to do that. It is real time savings and real money savings.”