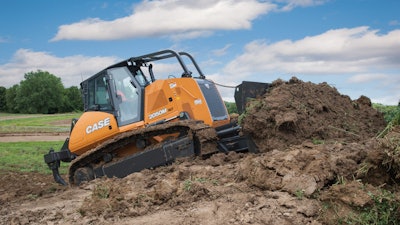
Probably no technology has had as dramatic effect on earthmoving efficiency as 3D grade control. “A lot of focus has been on 3D,” acknowledges Kris Maas, director - product management, machine control, Topcon. “That is going to continue in the future. But there are so many applications you can do with 2D where you don’t need 3D.”
Even in cases where you already own a 3D grade control system, 2D can be a better solution on some projects. “I have been on jobsites where contractors set the base station and they are building a flat pad,” says Maas. “As long as they have 3D, they want to take maximum advantage of it. In some cases, it is not necessary.” In the case of the flat pads, a laser is likely a better solution. “It is easier to set up, easier for the operator.”
The 2D solution can also be very cost effective. “If you look at 2D, price has been under constant pressure,” says Maas. “When I started in the business 25 years ago, we sold a flat plane laser for $5,000. Now you can buy it for $495.”
And 2D technology continues to evolve. “We are reinforcing our efforts to modernize our 2D platform for the future,” says Maas. “We are definitely going to come out with new technologies in the next year.”
2D Technology Advances
“2D is still a fantastic place to get started with construction technology,” says John McKendry, market segment manager, Trimble Civil Engineering and Construction. “Over the last 40 years, we have continued to innovate on 2D technology. The latest evolution, Trimble Earthworks GO!, highlights our continued investment in 2D as a way for contractors to leverage grade control as a first step into technology.”
He adds, “Technology adoption produces bigger gains in efficiency and productivity than any other single thing a contractor can do, rather than adding head count or adding machines. If we can reduce the barriers of getting into technology and show contractors the ease of use in the 2D space, then it opens up the conversations about future jobs or future expansions into other 2D or 3D solutions.”
Trimble Earthworks GO! is dedicated to 2D machine control. “It is a product for compact grading attachments for skid-steer loaders,” says McKendry. “At first release, we are supporting the Bobcat loader with the Bobcat grader — either the HD or the standard grader. We are also supporting the Cat D Series skid steers, compact track loaders and multi terrain loaders with the Cat BB121 or BB124 box blade.”
Trimble has tried to reduce the barriers to adoption of Earthworks Go!. The ease of use and cost have been two of our highest priorities with this product in order to make it easier for customer to adopt.
At the core of the system is the Earthworks GO! software that guides the user through installation, setup and operating modes. The software was specifically designed for local small site contractors and owner-operators. iOS and Android compatibility allow operators to use their smartphone as the primary machine interface.
The system includes a magnetically mounted electronic control module (ECM) that plugs into the attachment with a single cable. Laser receivers plug into the attachment, as well. An app on your phone connects to the ECM wirelessly.
“With just the phone app, you can automate the blade in a slope-only manner; you can add a single laser so you could hold an elevation and a cross slope; or you can go to a dual laser setup for more flexibility,” says McKendry.
Installation is very simple. “We ran a time trial at Trimble Dimensions where we timed customers installing the system,” notes McKendry. “They did an abbreviated portion of the install and people were finishing in three minutes.”
Trimble has tried to reduce the barriers to adoption of Earthworks GO!. “The ease of use and cost have been two of our highest priorities with this product in order to make it easier for customers to adopt,” says McKendry.
On the excavator side, Trimble Earthworks offers solutions that range from simple 2D to full 3D. “Earthworks today is a very complete 2D excavator system starting at the basic no laser reference — just using a touch point to go down to a certain depth for a utility or for a water line,” says McKendry. “You can bench off the ground and go down 4 ft., or whatever your frost depth might be. You can add a laser receiver and start working off a rotating laser. You can work off a bench if you are trying to carry a certain slope on a utility line to maintain the appropriate drain slope.”
OEMs Offer Built-in Solutions
Caterpillar’s GRADE with Slope Assist is another innovation that provides a simple, cost-effective solution for grade control on the company’s dozers. “2D Grade technology with Slope Assist can benefit projects that are not as complex,” says Scott Hagemann, Cat GRADE market professional. “By using the sensors integrated on the machine to maintain a desired main-fall or blade slope based on the level of the tracks, no infrastructure is needed. If you want to have a blade slope of 2% for watershed, input 2% for the blade slope, press auto and you control the blade elevation. The machine will maintain the blade slope.”
Without a base station or laser, the system measures grade relative to the tracks. “You set the value you want and the blade is controlled to maintain this value in reference to the tracks,” Hagemann elaborates. “If you want a flat pad, build a section to get your machine on, and now you have your base elevation for the tracks to get on and reference.”
Cat Grade Control Slope Assist automatically maintains pre-established blade angles for the grade, enabling operators to finish up to 39% faster with up to 68% better surface quality and using up to 82% less operator effort. It maintains blade angles so you get better surface quality, even with a less experienced operator. No base station or laser is needed, there is no additional hardware, software or equipment to buy and there is nothing to remove from the machine at the end of the day.
The system is also adaptable and fully upgradable as the nature of your projects change. “You can add other 2D or 3D systems with the included AccuGrade Ready Option (ARO),” says Hagemann. “Customers can rent a 3D system if they need it for a short-term project. ARO are plug-and-play for other Grade technologies.”
[VIDEO] Contractor's View: How Cat Slope Assist Cuts Two-Thirds of Road Staking
The 2D indicate-only system for Cat excavators provides the operator with precise real-time bucket positioning relative to the desired grade. Using a combination of position sensing hydraulic cylinders and sensors on the stick and boom pins, the system calculates bucket tip position relative to a grade/survey stake or benchmark.
“You then use a known point — either a stake with a reference mark, existing ground or laser transmitter — to ‘bench’ from,” says Hagemann. “You put your desired cut in and as you move the machine linkage, the display will give you guidance on what is needed to get the bucket teeth to grade. Benching off a laser is more accurate and recommended when digging slopes. The Assist semi-automatic function does work on our integrated 2D and 3D systems.
New Cat Automated Grade Controls Usher in More Efficient Excavators
“With our Next Generation excavator machines, we include the 2D Grade and Assist functions with the standard machine,” he points out. “It can’t get more affordable than that. They also include some safety features like E-ceiling, E-fence and E-wall.”
Case Construction Equipment offers the SiteControl CoPilot system, which is the result of a global partnership with Leica Geosystems. It is available on the 1150M, 1650M and 2050M dozers.
“The Case SiteControl CoPilot system was developed for use with our M-Series dozers, and is comprised of an inertial measurement unit, wiring harness and in-cab display,” says Richie Snyder, solutions marketing manager at Case. “The easy-to-use system allows operators to set a desired slope/grade reference, and automatically holds that grade/slope without the need for lasers, masts or GPS, regardless of underfoot conditions. [This enables] both seasoned and less-experienced operators to easily achieve and maintain a smooth surface, slope or grade throughout the work area.”
The Case SiteControl CoPilot system was developed for use with M-Series dozers and allows operators to set a desired slope/grade reference, and automatically holds that grade/slope without the need for lasers, masts or GPS.
For excavating, Case offers 1D and 2D options. “The 1D excavator system, the iXE1, uses three inclinometer sensors mounted on the boom, stick and bucket. The sensor on the stick also has a built-in laser receiver,” says Snyder. “The system is reset by means of a laser plane or a physically defined reference height, like a grade bar or a curb stone height. Then the desired depth and slope are entered into the control box.
“With this system, you only work with a one-direction slope. The arrows on the display will indicate whether you are too low, too high or on grade,” he explains. “This information is also given by means of an audible signal, while the LED screen also displays the level in metric units or U.S. feet.”
The 2D option, the iXE2, combines depth, pitch and roll, providing a complete picture of the job at hand. An additional rotation sensor on the counterweight upgrades the system to a dual-slope capability. The 2D function uses a compass to fix the slope direction. This means you can move the machine without the system losing direction.
The dual-slope system contains two sensors that record pitch and roll and compensate for the tilt of the machine. The excavator can then stand at an inclined position and still carry out leveling work around the entire machine.
Choose A Solution for the Application
Topcon’s entry-level excavator system is the X-52. It offers several different 1D and 2D options depending upon the components utilized.
“A 1D system has four sensors — a bucket, stick, boom and body sensor — that will just give you the position of the machine,” says Maas. “When you move your machine, you have to reference your bucket again because there is no other elevation reference on site that the machine can refer to.”
Topcon’s entry-level excavator system is the X-52. It offers several different 1D and 2D options depending upon the components utilized. The system components can be upgraded to 3D.
You can step the 2D solution up even further with use of a laser catcher. “When you are working in a certain area and you move the machine to a lower section, you don’t need to re-reference your bucket. Your laser catcher knows the difference between position A and position B,” says Maas. “It will compensate for the height difference of the machine automatically.”
The best solution really is dependent upon the application. “When you are just digging a trench with a slope, you can easily do it with the 1D system,” says Maas. As the jobs get more complex, you need to step up to more advanced 2D and eventually 3D solutions.
Topcon also offers a range of jobsite grading solutions. One 2D solution that often proves useful in conjunction with 3D is the sonic tracker — a very simple technology that shoots a sound wave off a solid surface and measures the time it takes to bounce back to determine the distance. “Then you can set a distance as a constant to follow a stringline, curb stone or other existing reference on the jobsite,” Maas points out.
The sonic tracker can help eliminate any concerns that there may be errors in a 3D design performed by a downstream contractor that could result in surfaces such as driveways and curbs not lining up. “A lot of customers are using 3D on one side and using sonic on the other side to match the existing surface or the existing structure,” Maas notes. The combination of 3D and 2D on sites is a popular solution.
Display Technology Evolves
Trimble has introduced a Bring Your Own Device (BYOD) option for its newest generation platform. “With the Trimble Earthworks platform, we made a pretty big change to our displays,” says McKendry. “We now have a 10-in. Android touch display, the TD520. That display is used across 2D and 3D. As an option for entry-level customers, we allow you to bring or use your own display, as well. We have seen a lot of people do that.”
The BYOD approach was made possible through a change in the system architecture. “In the past, our control box in the GCS900 system did all of the calculations for the positioning and comparing where you were on the design with 2D or 3D, and controlled the valves or automatics,” says McKendry. “In Trimble Earthworks, that ECM is mounted on the machine. The display is just really providing that graphical interface to the operator.”
Screen technology has progressed with the advent of 3D systems. This technology is most often also used for 2D. “Touchscreen color displays give operators very large, clear reference whether it is arrows or numbers to guide them to the desired grade,” says Hagemann. “We have audible options to let the operator know when they are getting close to and have achieved the desired grade.”
Modular Approach Yields Benefits
The majority of systems on the market use a modular approach where it is possible to upgrade from 2D to 3D by simply adding or swapping out a couple of components. In many cases, this makes the systems scalable for the job at hand.
“Our dealers offer the rental possibility to customers,” says Maas. “If you have a 3D job and a 2D system, you can rent 3D components to make it a 3D system for a particular job and then go back to the original equipment.”
“Equipment owners and fleet managers should consider their long-term needs and research the scalability of their machine guidance/control systems,” Snyder advises. “Several equipment manufacturers have partnered with technology companies in order to offer some form of grade control option installed direct from the factory. Specifying grade control options direct from the factory not only saves time and money in the long run by eliminating the future downtime for installation, it also means its easier and more affordable than ever for contractors to get started.”