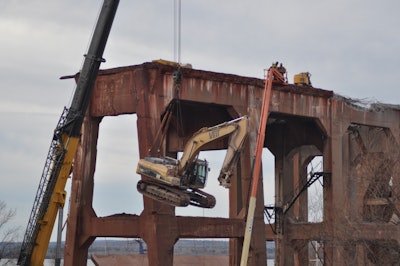
Information from this article was first published in Demolition Magazine and is being reused with permission from the National Demolition Association.
What’s more dangerous and challenging than demolishing a 60-foot-wide, 2,000-foot-long structure composed of concrete, iron and wood? Demolishing it 80 feet off the ground over the largest freshwater lake in the world.
The City of Ashland, Wis., and Wisconsin Central railroad had both a historical and safety challenge on their hands when it came to deciding what to do with the long out-of-use Ashland Ore Dock. Built in the early 1900s, the structure once loaded vessels with iron ore mined in the area. The ships then transported the ore from Lake Superior through the chain of Great Lakes and out to the eastern seaboard for nearly half a century. The dock has been a significant landmark for the city, but it gradually fell into disrepair.
The city petitioned the state to conduct an engineering assessment study to determine the structural integrity of the dock. Comprised of a structural steel frame that held railroad platforms and rails on top, structural steel unloading chutes and a treated timber frame trestle that led up to the dock, the results of the survey and condition of the components varied greatly. The decision was finally made to tear it down.
Prepping the site, protecting the lake
After a few months of removing the pieces of the structure that were the greatest risk to the public’s safety, CN, the current owner, selected NDA member, Veit & Company, Inc., a specialty contracting firm located near Minneapolis, to oversee and perform the demolition.
“After gaining the necessary permits from the various organizations involved, we began removing the wooden trestles in the fall of 2011,” said Steve Hosier, vice president of demolition with Veit. “The next step was determining how to best approach the job. It’s pretty unusual to have a job that’s only 60 feet wide, 2,000 feet long and out in the middle of a lake, and 80 feet above the water.”
Video: Genesis Demolition Recyclers Take Down Ore Dock
As well as the structural challenges of the dock, the Wisconsin Department of Natural Resources regulations required that Veit’s demolition team ensure none of the concrete, iron, wood or other debris fell into the surrounding water, which reached depths of 24 to 28 feet below the surface. “The city’s intake for fresh water supply is located just down from the structure,” said Ryan Olson, demolition general superintendent with Veit. “If any demolition debris entered the lake water, it had the potential to affect the city of Ashland’s water supply.”
To meet this challenge and ensure no debris fell into surrounding Lake Superior, the Veit team spent three to four months prepping the site for demolition, which included covering open-water areas at the base of the dock with steel plates and developing deflection panels and barges – the first of several innovative fabrication projects the company designed and constructed as part of the project.
The next fabrication project proved a bit more challenging, however. Working at 80 feet in the air, the material had to be contained when it fell off the dock. In order to keep the debris within the footprint, the demolition team constructed deflection panels that were attached to barges floating alongside the dock, which would catch the rubble and keep it away from the water. The panels and barges were designed and fabricated at Veit’s shop and then assembled and modified at the jobsite. As a further precaution to keeping the water safe from demolition debris, the Veit team implemented a 28-foot geo-tech fabric turbidity curtain below the water surface, essentially encasing the immediate work area and separating it from the lake.
Taking demolition to new heights
The Veit team decided to work from the top down. This meant the majority of work would be done starting at heights of 80 feet, sitting above deep, open water with strong currents. It also meant that heavy equipment, such as backhoes, needed to be transported and secured for operations at the 80-foot height. “It was unique and interesting lifting a couple of 90,000-pound backhoes on top of the dock,” Hosier said.
The team also had to ensure the excavators were safely secured when in use and mobile for transporting them down the dock as the demo work progressed. The work plan called for demolishing the structure from top to bottom and front to back, which meant the backhoes had to move in phases once each section of the dock had been removed.
Veit secured the backhoes on a custom-fabricated railcar. Utilizing the existing railroad tracks that ran along the top of the dock, they designed and built custom railcars that were safely and soundly secured to the backhoes, could be locked down during demolition and then unlocked and repositioned throughout the duration of the job.
Safety first
“Safety was the biggest challenge,” Olson said. “It wasn’t normal operating conditions to work at the heights we did, and we had deep water right next to the worksite. Working on top of the dock was a 100 percent tie-off area.” Veit also set up a lifeline system that ran the full length of the dock so that crewmembers were harnessed and connected to the main cable at all times.
As part of the demolition process, the Veit team separated the concrete, steel and wood components from the structure and prepared it for recycling to be used in various capacities throughout the local area, such as steel scrap, road base and retaining walls. The steel materials were sold to the scrap yard to be melted down and reused; the concrete was crushed and sold to local contractors to be implemented as road base, and the wood materials were repurposed locally as well.
While no plans are currently underway for improving the base of the dock, ideas include developing the structure for recreational use, such as fishing and swimming, and adding kiosks with historical photos, information and artifacts from the dock, and refurbishing some of the dock’s original light poles for use on the base.