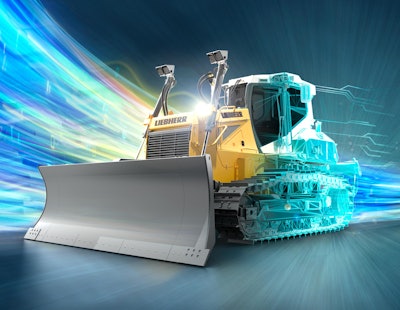
As the complexities of construction jobs proliferate—whether they be space constraints while working in urban areas, challenges onboarding new workers or the obstacle of grading a tricky slope—crawler dozer technology must likewise evolve. In last August’s issue of Equipment Today, a feature story deep-dove into the crawler dozer automation technologies that now make operators jobs easier, more productive and safer. This year, grade control technology, drivetrain updates and data transmission take on more importance than ever before, in the face of a labor shortage crisis, steep inflation and a possible recession in the United States.
However, rather than delineate every automation feature of each new dozer, this latest dozer technology analysis strives to serve as a practical handbook for choosing the best dozer for the jobsite and business. This issue of Equipment Today will serve as a case study guide to solve contractors’ most pressing problems while providing the essential dozer specifications and images users want to see. That is not to say there are not new dozers to discuss. There are several, including Doosan’s first dozer for the North American market, the DD100, and CASE Construction Equipment’s Minotaur DL550 compact dozer loader. The equipment and technology a contractor chooses will vary depending on the situations and desired solutions of the task at hand.
Worksite Challenges Offer Opportunities for Dozer Machine Control to Shine
The Situation: A construction company takes on an urban jobsite with a small turning radius that requires concrete demolition and grading prior to building. This project could possibly be a municipal jobsite, for example, in a high population density area of a city.
The Solution: “We went on a customer visit where we were looking at our guidance system in downtown St. Louis, in a block, trying to run machine control, grading down and it was a really tight jobsite, and I think the area they were trying to grade, dump trucks had been driving over and it was super hard, packed down,” said CASE Construction engineer Brady Lewis at the recent CASE Minotaur DL550 launch in Tomahawk, Wis. in August, describing a project for a nonresidential office building that used the industry-first Minotaur DL550 compact dozer loader. “So, it was a very good test of the machine. They had to go rip up a lot of stuff before they could even get to the point where they could grade, just because in that small site, everything was all concentrated together.”
In this case, Lewis and the CASE team effectively used the Minotaur DL550, a compact dozer loader, to solve the packed-down grading with the Minotaur’s optional, integrated ripper. The 17.7 in. rubber tracks and two steel grouser track options of the Minotaur DL550 allow for thorough versatility on a jobsite with mixed materials, from earth to concrete rubble.
The uniqueness of the CASE Minotaur DL550 lies in its chassis-integrated C-frame with a six-way dozer blade. The C-frame hydraulically couples into both the chassis of the machine, as well as the attachment coupler. This design provides the stability and operating plane of a small dozer while ensuring that all operating power is channeled through the whole body of the machine. This establishes greater performance and long-term reliability than the simple combination of a dozer blade attachment to a traditional compact track loader.
It also comes standard with CASE Universal Machine Control, which makes the machine ready for any of the major three providers of machine control technology—Leica Geosystems, Topcon and Trimble. As mentioned in the scenario above, the Minotaur DL550 is available with an optional, industry-exclusive fully integrated ripper for tearing up tough terrain to simplify dozing and earthmoving operations. Customers must order the integral ripper with their initial purchase of the Minotaur DL550, as it cannot be removed or added as an aftermarket accessory.
The C-frame is then detached to allow the operator to use it as a loader with a heavy-duty 1.25-cubic-yard bucket, or with hundreds of common loader attachments many equipment owners already have in their fleet.
“The CASE Minotaur DL550 is built like a dozer with the full control and operator experience of a larger machine,” explained CASE product manager Jeff Jacobsmeyer. “That includes the ability to deploy a full range of 2D and 3D machine control solutions that turn this machine into a compact fine grading solution that can get into areas and jobsites where it’s not practical to bring in a full-sized dozer.”
A Continuing Labor Shortage Requires Innovative, Nimble and User-Friendly Technology
The Situation: Like many construction businesses in the past decade, contractors today struggle to source, hire, and retain skilled, consistent labor. Despite the slowing of the 2022 U.S. economy, with the potential threat of a full-blown recession, many construction job openings remain, according to July’s report from the U.S. Bureau of Labor Statistics.
Even if construction industry job growth peters out into 2023 and project focus shifts from the private sector to the public due to the Infrastructure Investment and Jobs Act, construction companies still vitally need a robust and trainable workforce. Less experienced operators require equipment that can adapt to their developing handling skills. The dozers that these new workers use should offer hydraulics and machine control to ease the bumpiness of adapting to the landscape of a new job, pun intended.
The Solution: Enter the Doosan DD100 dozer, the manufacturer’s first dozer for the North American market, which debuted as a prototype in early 2022. Similar in size and power to the Caterpillar Cat D3, John Deere 650K and CASE 850M dozers, the Doosan DD100 is at the higher end of the 10-ton size class of its smaller dozer competitors at 25,209 lbs. At a slightly higher horsepower—122 hp—and weight than the Case 850M, the DD100’s prime selling point is its commitment to scale to any operator’s skill level.
Visibility is a key element in the DD100, which offers full-view windows, thin pillars to avoid obstructing an operator’s sightline and the notable absence of a mushroom-shaped pre-cleaner on the dozer hood, offering an integrated version instead. All of these intentional visibility features add up to an easier, safer experience for an amateur operator.
Similarly, electro-hydraulic controls come standard on the Doosan DD100, meaning that operators can fine-tune the machine’s performance to their desired feel, whether the job requires more power and thus more fuel or the fuel efficiency that comes with precise pushing. A skilled, seasoned operator of the DD100 can adjust the dozer for finer control, whereas a newer worker may wish to rely on an optional, mast-less 3D machine control by Trimble.
“The visibility is excellent with these machines and the seat-integrated controls make it very easy for the operator to use the machine,” said Aaron Kleingartner, dealer and product marketing manager, Doosan Infracore America, at a product preview in early 2022. “Right out of the gate we are going to have the ability to have 3D machine guidance and control.”
Doosan also intends to release a 13-ton dozer in or around February 2023, possibly in time for CON-EXPO, the DD130.
“This is the next significant milestone in the development of the new Doosan dozers,” said Edward Song, CEO of Doosan Infracore North America. “Our North American dealers and their customers are eager for the arrival of the new Doosan dozers. We look forward to launching the new line of construction equipment later this year.”
Precision Hydraulics and Grading Among Dozer Technology Features
The Situation: A hilly worksite provides a plethora of opportunities for dozer technology to shine. The jobsite may require multiple grading levels, and the user needs to be able to set precise parameters for work and drive hydraulics.
The Solution: Machine control and operator assistance systems are being used more frequently to increase productivity, and have set the crawler dozer market down the path toward autonomy. Liebherr is addressing this trend with its Liebherr Operator Assistance Systems (OAS), which currently offer three levels—Free Grade, Definition Grade and 3D Grade—for 1D, 2D and 3D applications.
Free Grade is active blade stabilization for free or creative grading. This assists with creation of flat surfaces, ramps and dams. Definition Grade is for basic modeling of 2D surfaces. It operates without additional equipment such as GNSS receivers or base stations and provides automatic position control of the blade to a specified target inclination. 3D Grade offers automated six-way blade control for exact blade positioning to create 3D site models.
The Liebherr OAS is controlled by a 9-in. touch display that allows the operator to fine-tune dozer operating parameters such as responsiveness of work hydraulics, responsiveness of drive hydraulics, ECO mode, automatic speed reduction and engine shutdown.
Similarly, the CASE Minotaur DL550 compact dozer loader offers onscreen hydraulic flow control balancing of function combinations, to meet various jobsite needs, according to the CASE Minotaur DL550 team.
“Now, that’s a complicated statement there,” said CASE product manager Brad Stemper at the Minotaur DL550’s launch in Tomahawk, Wis., in early August. “Hydraulic flow control balancing. This function is enabling the operator to adjust combinations of functions and make them more efficient for what the operator needs to do. What I mean by that is, it’ll give you an option to adjust priority to arm or boom, or make an adjustment to arm and swing, dedicating more flow to one of those within those pairs.”
These are independent adjustments, he explained—the arm and boom and the arm and swing.
“I can take some flow away from the swing operation and dedicate it to arm, if I don’t need to dedicate as much flow to swing, to give me faster cycle times,” Stemper explained. The hydraulic flow control balancing feature of the Minotaur DL550 allows the operator to tailor the machine’s flow priority to the functions they prefer to use, based on the digging application.
Telematics Essential for Dozer Fleet Maintenance
The Situation: The jobsite and the operator are ready to tackle the obstacles of the project, but the dozer is having trouble running, breaks down or needs software troubleshooting attention.
The Solution: To avoid additional downtime, contractors require dozers with telematics solutions to enable support for remote troubleshooting or even repairs, aside from the typical productivity data that telematics software usually provides. Some of the latest telematics solutions, like John Deere’s SmartGrade Remote Support, ADVISER Remote and JDLink, allow for service technicians to view the machine’s health or maintenance problems remotely while the machine remains connected to the John Deere Machine Monitoring Center. The John Deere Machine Monitoring Center is supported by both the dealer and factory support staff, who stand by ready to help in the event of the need for more targeted expertise.
The CASE Minotaur DL550 compact dozer loader offers a similar telematics service.
“Our CASE DNA ensures that everything is ground-line service,” said Jacobsmeyer. “CASE takes it a couple steps further and supplies one year of site-watch telematics along with the availability of remote diagnostics and software downloads.”
The CASE Minotaur DL550 comes standard with the CASE SiteConnect Module, explained CASE support engineer Josh Belmont, as well as the CASE Site Manager app, allowing for a greater flow of telematics data and service interval information.
“It allows your fleet manager or your dealer service department to keep an eye on things proactively before opportunities arise from machine issues or downtime,” Belmont said, emphasizing that allowing access to the dealer through the SiteConnect Module allows two sets of eyes to remain on the Minotaur DL550’s health and performance.
The Site Manager app, downloaded to the owner or operator’s mobile device, allows for remote access between the Minotaur machine and dealer service technicians.
“This allows them to diagnose issues before they ever leave the shop, cutting down on unnecessary trips back and forth from the jobsite to the shop, ensuring they show up with the right parts and tools to solve the issue and helping you ensure that your machine is up and running when you need it to be,” Belmont said.
As contractors and construction companies continue to encounter obstacles to productivity, rising costs and worksite challenges, keep these new dozer technologies in mind for fleet purchasing decisions.
"All the precision and connected technologies offered for the Minotaur DL550 are in demand, and that demand is only going to increase in the future," Belmont said.