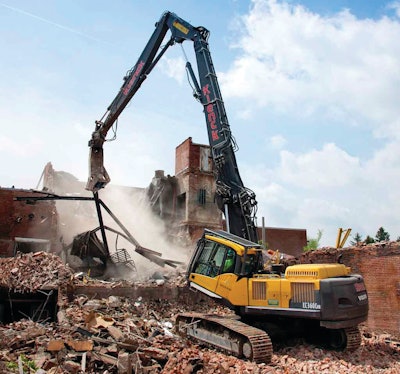
Information from this article was first published in Demolition Magazine and is being reused with permission from the National Demolition Association.
Klenck Company President Tim Klenck and his crew took on a challenging project with the demolition of an aging and idle meat processing facility in Anderson, Ind. He estimates that the building had more than half a million dollars of ferrous and non-ferrous material in it. “We can bring demolition prices down, save money for the owners, complete the job and still make a profit,” said Klenck.
The meat packing plant was a sprawling two- and three-story building built with interlaced bricks, concrete and structural steel. The building was filled with metal meat processing equipment. Some rooms were lined with stainless steel – a valuable commodity.
The Klenck Company, a member of the National Demolition Association, used three primary demolition tools to tear down and recycle the building: one Volvo EC360C High-Reach fitted with a multi-processor and two Volvo EC330B excavators. One excavator was fitted with a grapple and the other wielded a concrete crusher from its boom. A Volvo L110E loader worked on the demolition site as a support machine. Also on site as a support machine was the Volvo MCT 135 Compact Track Loader which has stable tracks, power and great visibility, according to Klenck.
The High-Reach machine had a 69-foot boom. Its multi-processor could crunch the concrete and brick structure with the front part of the jaws and cut through metal in the rear of the jaws. Klenck started demolition work on the rear of the building, saving the south and east walls for the last because they faced the street.
“Those walls protect the site from prying eyes and thieves,” said David Wagner, project superintendent. “Most people can’t even see that we were working back here. Plus, the wind usually blew from the northwest, so it was a favorable direction for us to use the dust suppression system” he said. The dust machine sprayed out a fine mist of water, which trapped dust particles and brought them down to the ground.
Wagner explained that the High-Reach started at the top of the building and crunched the brick and concrete so that it fell inward on the floors. That helped to fracture the floors and bring them down easier. That method is also the safe way to fell a building, Wagner said.
The multi-processor pulled out the structural steel and metal equipment and laid it back on a temporary pile while the grapple-fitted excavator sorted the metal into other piles behind the building. Meanwhile, the Volvo excavator with the concrete crusher worked on bringing down another portion of the building.
“The EC360 High Reach gives our people a great safety factor for the high-reach areas that they work in. It gives them great visibility and keeps them out of the fall area. It offers great protection. It’s a tool we've wanted for a long time; we just needed the right jobs to justify it,” said Klenck.
“We've been running Volvo equipment for four years,” he said. “We wanted something that would separate us, give us a certain image, and Volvo equipment does that. When people drive by and see Volvo equipment, they know it’s Klenck working.”