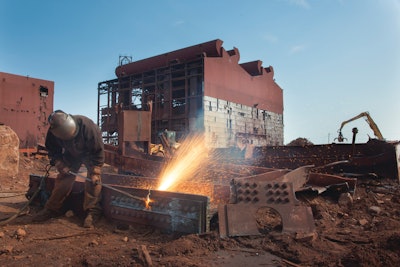
Information from this article was first published in Demolition Magazine and is being reused with permission from the National Demolition Association.
When a long-closed 100-acre steel plant in Sept Isle, Quebec, Canada, was slated for demolition, the Montreal-based branch of The EDS Group tackled the job, combining its asset recovery expertise with large-scale demolition proficiency. Using an arsenal of heavy equipment, as well as the latest in mobile shears and other attachment technology, the company has approached its spring 2013 deadline, anticipating the recovery of 65,000 tons of steel and concrete.
The building is owned by the Iron Ore Corporation of Canada (IOC) which had planned to reopen the building until the 2008 economic downturn dashed those plans. “This is a massive plant, two structures with a combined footprint of approximately 376,740 square feet that just didn’t fit into IOC’s plans,” said Sylvain Dupont, president of EDS Decommissioning Canada. “Because of the one-time intent to restart this plant, however, it had a lot of good equipment that we were able to sell. Once the salvageable equipment was removed, we were able to tackle the demo itself.”
Demolition started with the identification, careful removal and appropriate disposal of thousands of gallons of used oil, BPC-contaminated ballast, mercury thermostats, and asbestos from the structures.
“IOC has a proven commitment to safety and to minimizing its impact on the environment in all facets of its business,” said Dupont. “So they wanted to ensure that same commitment extended into the demolition of the pellet plant. Ultimately, they want this area to look like it did in the early 1970s before the plant was even built. In light of those concerns, we felt that a systematic approach, primarily using mobile shears to bring it down, was the best option.” The use of explosives was ruled out due to the ultra-heavy-duty steel composition of the structures.
That systematic approach to which Dupont referred included processing sections of each structure using the shears. Then, once the cut material was on the ground, they segregated it by material type and size and moved it to a separate area onsite where it could be further downsized. Using shears, the crew worked with more than 45,000 tons of steel along, placing it into individual piles down to the 2-foot by 5-foot pieces needed for shipment.
Although there is not much material the shears have not been able to cut, and they’ve been shearing material as thick as 1-inch, “In those cases, when the beams are simply too huge to shear, we still rely upon hand torching, but it’s fairly minimal," Dupont said.
Rising some 26 feet above the already impressive 130-foot profile of the plant was a pair of stacks used to vent emissions from the pelletizing process. While it would have been possible to shear each stack in place and let the processed debris fall to the ground, it was decided that pulling them down would be faster, more efficient and ultimately, safer.
“To do that, we used a Liebherr R984C-EW with a Jewell 160-foot, ultra-high reach boom and a Genesis GXP 300R mobile shear to first remove all the critical supporting material from around each stack,” Dupont said. “With that cleared, we then pulled each structure down. Once on the ground, we set to work with our larger demolition shears - usually the Genesis GXP 660R Maxx units - getting them down to manageable sizes. We had both stacks downsized and ready for shipment in about two days.”
As might be assumed with a 12-story-tall structure, the shear-equipped long-reach boom had been a huge part of the Sept Isle demo. In addition to clearing the way for the stack removal, the tool could access all the upper reaches of the plant. “Being able to process steel beams at such heights eliminates having a worker or workers up there with torches. Not only is the level of efficiency dramatically improved, safety - which is paramount in our operation - is as well.”
For areas of the plant that were a bit more accessible, EDS relied upon a Genesis GXP 1500R mobile shear. The added power of the larger demolition shear (as much as 2,800 tons of cutting force) proved critical in processing some of the larger material they encountered. “There was an unending stream of huge material coming out of that plant,” said Dupont. “Being able to immediately cut through such hearty structural beams and so on has been invaluable in keeping us moving forward.”
The Sept Isle site also contained a good deal of dense concrete that was used in pylons and floor slabs and to support a pair of kilns. Dupont said that while they only have to remove material down to slab grade, they nevertheless generated sizeable volumes of concrete. “We figure that we will have removed more than 20,000 tons of concrete, all of which is being crushed and either used or disposed of locally. Because this was originally the port from which pellets were shipped, recycling of the steel was equally simple. It was taken by truck from the jobsite to the waterfront where it was loaded onto ships and sent overseas to a number of different buyers,” he said.