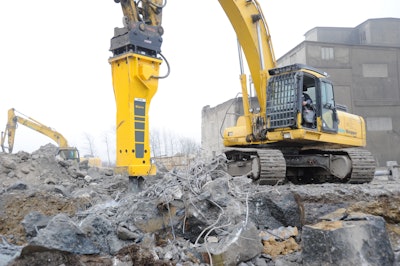
It is remarkable that modern hydraulic breakers provide a useful life measured in years since under normal operation one piece of metal attacks another piece of metal up to 1,000 times or more per minute. A preventive maintenance plan is the first line of defense, and employing the latest technology to track use ensures major maintenance intervals are not missed.
“A hydraulic breaker attachment — while designed to take and dish out quite a beating — has many components that can fail due to careless operation,” says Jerry Hutkowski, product manager for construction attachments, Case Construction Equipment. “A worn piston or compromised valve on a breaker will introduce dirt, debris and other contaminants into an otherwise healthy hydraulic system.”
“Breakers are high-maintenance attachments,” notes Greg Smith, marketing communications manager, Okada America. “Hourly, daily, monthly and yearly maintenance intervals are available from the manufacturer and can be found in the operator’s manual and maintenance manuals. It is important that the distributor representative provides this information and discusses the maintenance procedures with the end user and maintenance personnel when delivering the attachment.”
It must be noted that maintenance intervals are guidelines, because the severity of the application and operation may require additional and increased scheduled maintenance.
“Proper care in operation, as well as regular inspections and maintenance are the keys to breaker longevity,” says Tim Miller, U.S. sales manager, Montabert. “With the energy transmitted through a breaker in order to fracture material, any unattended loose or worn parts can become a much larger problem due to the forces exerted. With a brief and accurate walk around with corrective actions taken as needed, you can expect several years of uninterrupted service from your breaker.”
Every breaker manufacturer has a routine checklist of items that should be inspected on a daily, weekly and monthly basis. “They are all very similar in the inspections needed,” says Rich Elliott, product and application specialist for Epiroc Tools & Attachments Division. “The more routinely that the inspections are completed, the better the breaker will perform and the lower the downtime, which maximizes production. These inspections will also enable the operator to get more comfortable with the breaker. When something does not seem correct with the operation of the breaker, or something looks off, the operator knows to stop the breaker and inspect what is going on.”
“Sticking to the maintenance intervals will help to ensure that proper tolerances are kept up on tool bushings and other common wear items on breaker attachments,” says Hutkowski. “Proper care and maintenance of a breaker will also reduce wear on the bushings and pins on the machine.”
Size Hammer to Job and Machine
The first step in ensuring longevity is to properly set up and size the hammer for the job. “One of the most common mistakes is mismatching the breaker attachment to the carrier,” says Hutkowski. “Operating an oversized breaker will not only cause unnecessary wear and even critical damage to your excavator, it will also be extremely unsafe for the operator and everyone around them. So, check the operating manual or consult with your equipment dealer to make sure you have the right match.”
He adds, “The primary machine considerations for breaker usage are the operating weight, tipping load, length of boom and arm, overall lift capacity and hydraulic flow characteristics — namely the operating pressure, hydraulic flow rate and auxiliary flow rate.”Once the hammer energy is greater than the comprehensive strength of the material being broken, any ‘extra power’ after that is wasted energy. The hammer and excavator need to be properly sized.Caterpillar
“The application should and will determine the hammer size selection,” says Tom Munch, business development representative, Caterpillar. “Too small a hammer for an application will cost the operator and contractor production and profit. Too large a hammer will be classified as ‘overkill’ for a jobsite. Once the hammer energy is greater than the comprehensive strength of the material being broken, any ‘extra power’ after that is wasted energy. The hammer and excavator need to be properly sized.”
The size of the existing carrier is sometimes the main criteria for hammer selection, narrowing the choices to those that fit your carrier. “A hammer needs to be properly sized to the machine that it will be configured on,” says Munch. “Too heavy of a hammer for a machine will make it unstable and unsafe. Too light of a hammer and the machine weight can cause premature wear of the hammer.”
Keep Grease Flowing
Grease performs a two-phase job: it lubricates and it clears the tool bushing area of debris. The grease also needs to be able to withstand heat and pressure. Breakers exert a tremendous amount of force on the tool. The material causes heat and pressure in the tool bushing area. Manufacturers typically recommend high moly chisel paste with a working temperature above 500° F. The moly provides added lubrication once the oil additives break down. If you apply a grease that breaks down at temperatures below 500° F, you have no lubrication once the unit has been run for a while.
“Greasing a hammer every two to four hours is the No. 1 preventive maintenance for a hydraulic hammer,” says Munch. “Whether the hammer is greased manually or has a hammer-mounted or carrier-mounted auto lube system, it is a critical requirement that the hammer receives not only the grease, but a high-quality, high-temperature hammer paste. A quality grease will not break down as internal component temperatures within a hammer rise. A standard grease will ‘liquefy’ as a hammer is operated and not provide the hammer the protection it requires.”
Auto lube systems can continually supply grease to the hammer. This increases the chances that the tool and bushings will get lubricated on a regular schedule. However, a major concern with auto lube systems can be a false sense of security. It’s not uncommon for the canister or cartridge to empty during operation.You have steel against steel and a lot of heat so you need a good lubricant, and a lot of it. Manufacturers typically recommend high-moly chisel paste with a working temperature above 500° F.Okada
The key is to make sure sufficient grease is applied to the tool/bearing interface. Monitor the tool and ensure 4 to 6 in. of melted grease is flowing from the hammer, properly lubing, cooling and flushing contaminants.
The amount of grease depends upon the application. “Unless you have an automatic lubrication system, grease, grease and more grease,” advises Smith. “You have steel against steel and a lot of heat so you need a good lubricant, and a lot of it.”
The larger the breaker, the more likely you should use an auto lube system. On some larger hammers, there is no practical way to supply enough grease by hand, and the breaker needs to be running grease all of the time.
Continually Conduct Inspections
In addition to greasing, routine inspection can save a lot of damage and repair expense. Many breakers are gas/hydraulic operated. These designs use nitrogen gas in the backhead as a cushion and/or for increased power and may also utilize an accumulator to absorb hydraulic spikes during operation. These gas charges should be checked for the appropriate pressure reading on a weekly basis, as a change in ambient temperature can affect the required pressure.
Visually inspect the hydraulic breaker for loose or broken bolts and worn out bushings. Keep an eye on tool and bushing wear. If the tool appears loose in the bushings, the play should be measured and recordedThe primary machine considerations for breaker usage are the operating weight, tipping load, length of boom and arm, overall lift capacity and hydraulic flow characteristics – namely the operating pressure, hydraulic flow rate and auxiliary flow rate.Case Construction Equipment
“Visual inspections should be conducted daily,” Miller advises. “Check welds for possible cracks on the bracket cap, cradle, tool and boom.” (Do not weld on the cradle without checking with your dealer.). Check for loose nuts and bolts in the bracket cap, suspension, accumulator, side plates, tie-rods and wear plates.
Worn out front bushings will cause misalignment between the piston and working steel. This may allow the piston to contact the inside cylinder wall during operation, thereby damaging the piston and cylinder — the two most expensive components.
Tool retaining pins are also subject to wear. The tool and tool retaining pins should be removed and inspected every
40 hours of operation. This interval could be longer or shorter depending on the material and application.
Look for damage in the retaining pin area. If there is excessive wear on the tool retainer during routine weekly inspections, examine how the hammer is being used. Tool retainer wear is the first indicator of blank firing, followed closely by the tool retainer shoulder.
Some manufacturers suggest rotating the retaining pins to have them wear evenly and to double the life of the pins. Minor galling is expected, but when deep scarring becomes noticeable, you need to replace the retaining pins. If you choose not to, the pins could deform, making them very difficult to remove.
“When replacing tool retainers, always replace them in sets and rotate them equally,” says Miller. “A good tip is to mark the ends of the retainers to keep track of the rotation order.”
The working steel should be inspected weekly. Most wear on a working steel should be on the end doing the impacting. But the section of the working steel in the hammer can also show signs of wear. Look for scarring and galling around the working steel where it comes into contact with the front bushing. This is usually a sign of insufficient grease. When scarring or galling occurs, immediately replace the working steel. If the front head bushings are also worn past recommended tolerances, they should be replaced. A new working steel and front head bushing could prevent unnecessary piston and cylinder damage.
“Some bushings are grooved to provide even grease distribution,” says Miller. “Replace the bushings when grooves are worn through. Excessive bushing wear causes tool misalignment to the piston, causing premature breaker failure.”
Every inspection will give you a full use profile of that breaker. Note peculiar wear patterns. Uneven wear on the top of the tool indicates the operator may not be running the hammer at 90° to the product, which is optimal. If wear is present on the side of the tool, operators are working at less than ideal angles.
Properly Set Up the Hydraulic System
“Make sure that the auxiliary circuit is in the breaker mode and the hydraulics have been properly set up by the service technician to operate the specific model breaker,” says Elliott. “This will ensure proper operation of the breaker, increase production and decrease maintenance requirements.”
With the energy transmitted through a breaker in order to fracture material, any unattended loose or worn parts can become a much larger problem due to the forces exerted. With a brief and accurate walk around, with corrective actions taken as needed, you can expect several years of uninterrupted service from your breaker.Montabert
Another common cause of hammer failure can be unexpected failure of the quick-disconnect couplers on the hoses that are installed on the carriers. “Many machines can be outfitted with quick couplers that make it easier than ever for an operator to attach a breaker to the end of the stick without leaving the cab. But connections should be checked regularly for dirt and debris, which can get into the hydraulic lines and cause unnecessary damage to the machine,” Hutkowski points out.
He adds, “Every time you hook up a different attachment to a machine, you are potentially introducing contaminants into an otherwise closed system.” Always be sure that your breaker attachments are properly maintained and that couplers are thoroughly cleaned.
“Hydraulic ball valves and quick couplers may be a source of erratic performance and/or cause a rise in hydraulic temperature,” says Miller. “Ensure they are 100% open, in good condition and not leaking oil. Continuously check for oil leaks and any rise in the oil temperature. This is an indication of worn or damaged seals that need to be replaced.”
“The carrier’s auxiliary circuit for the breaker should be tested on a yearly basis or any time that there is a major hydraulic component changed on the carrier to ensure that it is set within the operating parameters of the breaker,” Elliott adds.