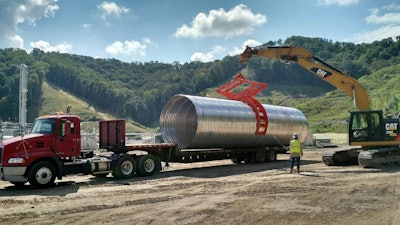
Dedicated pipe handling attachments increase jobsite productivity and safety, but choosing the best attachment for the job requires an understanding of utilization, the type of pipe that needs to be placed, carrier lifting constraints, versatility and much more.
“Everyone knows that the right equipment and tools for the job makes any project easier and faster, such as excavators for digging, hammers for demolition, crushers for refining hard soil and materials, etc.,” says Justin Hendricks, general manager/director of engineering, Vacuworx. “Choosing the right attachment for material handling is no different. Companies should look for attachments that work with their existing host machines, offer the degree of attachment flexibility that is needed (i.e. do they want to attach to an excavator and then leave it on indefinitely or do they need to switch out attachments during a job), and operate in a way that keeps workers out of harm’s way.”
Machine versatility is a common concern. “For example, Vacuworx attachments are available with a variety of quick connect options for virtually any excavator, cab be installed and ready to use in under an hour, are available with either diesel engines or can be run off the host machine’s hydraulics,” he adds. “All heavy-duty RC and MC Series lifters feature 360-degree rotation and wireless remote operation from the cab of the excavator to keep people away from hazard areas.”
Rigging Slings Adds Risk
In some instances, contractors have used slings for lifting and positioning pipe as opposed to purchasing dedicated attachments. “Traditional material handling methods, such as slings and chains, expose workers to risks by requiring them to be in the loading area, possibly climb onto the pipe, or be in the trench to release the pipe,” says Hendricks. “These methods may also create an unsafe environment due to pipe that is not secure, unsafe rigging, or environmental conditions that could affect the load.
There are many potential downsides to using slings. “Using slings can be time consuming when connecting and disconnecting,” explains Dan Mongan, The Caldwell Group. “In addition, pulling the sling out from under the resting pipe can be dangerous and cause sling damage. Dedicated attachments increase efficiency and safety.”
You really want to limit the number of employees working around the pipe being lifted. “Any time you reduce labor or interaction with the lift, it is safer,” adds Mongan. “In addition, some of our pipe lifting attachments can be removed from the pipe without having someone in the trench. Others shorten the time they are in trench.”
The benefits are clear. “It’s really about productivity and safety,” he says. “If you imagine a sling wrapped around a pipe and you lower the pipe into the trench, somebody has to get in the trench to disconnect and you have to pull the sling out. It’s laying under the pipe. You have to drag it out from under and that can cause damage to the sling. There is tension in the sling and all of the sudden it comes free. You have all that energy in the sling and it could hit somebody. So there are a lot of advantages to using an attachment.”
Using the correct attachment also simplifies the entire process. “The idea is to do everything as right and safe as possible the first time,” says Tracy Black, operations manager, Kenco. By using a pipe lifting attachment, the bedding material isn’t affected. “Slings wrapped around the pipe must be removed after the pipe is installed. This typically causes the sling to be drug around the pipe and through the bedding. Many times this will rotate the pipe and occasionally unseat the joint.
“As contractors become more safety oriented, there are many transitioning to purpose built lifting attachments,” notes Black. “Unlike slings, the Kenco Pipe Lift, Pipe Hook and SuperLift allow the operator to be off center of the pipe and still make a safe pick. Slings constantly move against the pipe which creates wear.”
Any pipe lifting attachment can greatly increase the safety of unloading, staging and laying pipe. “The operator has the ability to position the lifter over or in the pipe to eliminate putting personnel in harm’s way,” says Black. “The same applies after the pipe is placed. The operator has total control of placing and removing the attachment.”
Making A Choice
There are several things to consider when choosing a pipe handling attachment. “It is important to know the pipe outside diameter, pipe weight and pipe material,” says Mongan. “Other factors include the lift capacity of the excavator and how the lifter will connect to it.”
It is important to understand the range of pipe you will be installing. “All of our pipe lifting attachments are rated for weight and some versions have diameter ratings as well,” says Black. “For instance, the Pipe Lift grabs the outside diameter of the pipe thus it has an Outer Diameter (OD) range per model. The Pipe Lifter was designed with capacities that coincide with standard pipe diameters of its given range. The Kenco PL2000 will accommodate 8-in., 10-in. and 12-in. PVC, ductile iron or steel pipe. This model has an outside grip range of 8.63 in. to 13.20 in., which factors in the pipe wall thickness. Standard Pipe Lift models are available to handle 4-in. PVC/ductile iron through 48-in. Reinforced Concrete Pipe (RCP). Each model will typically handle two to three pipe sizes which minimizes the ditch width.”
Some attachments increase versatility by being able to handle multiple pipes. “The [Kenco] Pipe Lift and SuperLift are designed to accommodate any pipe material,” says Black. “These lifters are mechanical so they can only squeeze the pipe proportional to the weight being lifted. They can also be used on longer lengths of pipe. The operator is afforded the opportunity to relax the grip and slide the lifter to the preferred balance point without the need from ground personnel.”
There is an attachment suited for almost any pipe laying application. “We have a lot of different attachments,” notes Mongan. “With some, you still need to get into the trench and with others you don’t. It’s just dependent on the specific lifter and the application. Our Pipe Pick or Tea Cup could lift a variety of sizes of concrete where a tong or a grab or a vacuum lifter might be designed for one specific diameter.” So versatility also comes into play.
With the Tea Cup lifter, the Tea Cup sling is typically lowered through a hole in the pipe. The Tea Cup carrier is then aligned and insert on the sling. “We sell a lot of Tea Cup pipe lifters every year,” notes Mongan. “It’s very versatile. It is inexpensive.”
The pipe material often dictates the attachment required. “Most attachments are specifically designed for the type of material the pipe is made from,” notes Mongan. “Is it made for concrete, cast iron, plastic or PVC?” Product information on company websites and experienced sales professionals can help point you in the right direction. “Even if you do not see a lifter that suits your needs, we can engineer and build a custom solution. “Fifty percent of our business is custom engineered lifting equipment.” This includes odd size pipes or capacities larger than those listed in the catalog.
Some attachments allow you to move more than pipe. “The Pipe Hook is versatile pipe lifting attachment specifically designed for RCP,” says Black. “When equipped with our detachable wings, box culverts can be easily moved as well. Standard Pipe Hook models will handle 8-ft. joints of pipe (or shorter) and accommodate a larger amount of pipe sizes. For example. For example, the PH9000 is designed to lift 12-in. RCP up to 9,000 lbs. The Pipe Hook is well suited for narrower trench box operations. Stock models range from 3,500 to 30,000 lbs., however custom pipe lengths and capacities exceeding 60,000 lbs. are designed.”
Another pipe handling attachment that Kenco offers is the SuperLift. “This lifter is designed to share multiple tine sets to pick different ranges of pipe,” Black explains. “Other tine sets are available for logs/debris, block and barrier wall. This versatility makes it the perfect choice for a lot of contractors. One unique feature of the SuperLift is once the load is placed and the lift plate is reengaged to the actuator, the lifter can be picked up until the tines are in clear space, at which point they will fully open for the next lift cycle.”
Frequency of use also impacts the decision. “Frequency and budget go hand in hand,” says Mongan. “For example, you could use a Caldwell CPP Pipe Pick or a Caldwell Model CPL Leveling Pipe Lifter on concrete pipe. The CPP would be less expensive but it requires a person to install and remove it from the pipe. A CPL is more expensive but can be installed and removed by the excavator operator alone. So if you are making a lot of lifts, I would recommend the CPL. If lifts are more periodic and budget is a concern, I would recommend the CPP.
“You can make an argument that the simpler a lifter is, the more rugged it is, the less problems you are going to have with it,” says Mongan. “But you need to look at the entire scope of the application to really decide the best way to go.”
The other thing that comes into play is the weight of the lifter versus the lifting capability of the carrier. “Our CPL, the leveling pipe lifter, some of those lifters weigh upwards of 1,000 lbs.,” says Mongan. “When you are talking about excavator capacity you also have to consider the weight of the lifter.”
Vacuum Lifting Simplifies Pipe Installation
Vacuum lifting allows faster load and unload cycles with less downtime than conventional methods since there are no slings and chains to hook and unhook, while the need for fewer ground personnel reduces the risk of accidents and lowers payroll and insurance costs. It also eliminates the need for costly cribbing or spacers for pipe or plate.
“Vacuum lifting offers significant advantages in safety (keeping workers away from the material being lifted), efficiency (faster load cycles, less downtime and easier placement of the materials), and requires less labor overall since tag line operators are not required on the ground,” says Hendricks. “One of the advantages of vacuum lifting is that you can load/unload pipe without disturbing adjacent materials, as well as reduce or eliminate the need for costly cribbing or spacers. In addition, the powerful positive engagement of the load, wireless remote operations and 360-degree rotation gives the operator precise control.”
Some pipes can be damaged if they are not handled correctly. “You want to select a lifting system that will not damage delicate materials or bonded coatings,” says Hendricks. “Vacuworx vacuum pads are designed to prevent damage to delicate materials and bonded coatings. Our state-of-the-art Tough Seal protects materials with no metal contact and secures proper vacuum even on dirty and somewhat uneven surfaces.”
Personnel on the ground can be minimized. “Vacuum lifting systems create a power positive engagement of the pipe that is more secure than traditional rigging methods,” says Hendricks. “Vacuum lifting eliminates the need for employees to climb on trailers to attach slings or chains and reduces the need for tag line operators on the ground. Finally, vacuum systems are able to go where people should not be (in trenches, on stacks, etc.).
“Vacuworx lifting systems have four principal components: a vacuum pump (which is driven by a self-contained engine or hydraulically powered by the host machine); a vacuum reservoir and valve which provides vacuum in the event of a power failure; vacuum pad(s); and visible and audible vacuum alerts,” says Hendricks. “The diesel engine (or hydraulic system) powers a vacuum pump that evacuates air to create ‘negative pressure’ and maintains a constant vacuum in the pressure reservoir. When activated, the system pulls a vacuum between the pad and the material to be lifted, providing a powerful positive seal,” he adds. “The vacuum valve opens and closes via a wireless remote controlled by the operator. When the valve is opened, vacuum pressure is released and the ‘negative pressure’ is transferred to the vacuum pads.
“Pad seal is used on the vacuum pad or pads to cover the material to be lifted and create the necessary suction,” notes Hendricks. “The vacuum seal holds until the operator activates the release (even in the event of a power failure). If anything happens while the load is engaged, such as running out of fuel, engine failure, vacuum pump failure, or even vacuum valve failure, the load will not release. The emergency light will flash and an alarm will sound to alert the operator that there is an unsafe situation, and the load needs to be brought down to the ground immediately.”
The overriding goal of all of the dedicated pipe handling attachments is to increase jobsite safety while simultaneously increasing productivity. The best solution really depends on your application and budget.
USE AT LEAST ONE IMAGE PER MANUFACTURER; OTHERS CAN BE CONSIDERED OPTIONAL