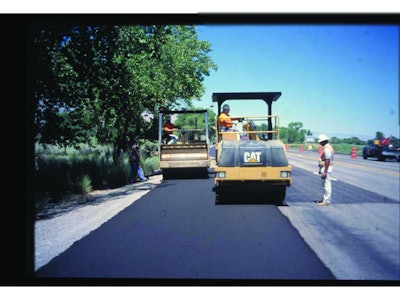
Hot mix asphalt mixtures that have tender characteristics still have to be compacted to a minimum level of density or a maximum level of air void content. Because of the lack of internal stability in the mix, however, the compaction of a tender mix is often very difficult.
It has been found that a mix that has tender properties – that moves or shoves excessively under the weight of the compaction equipment while being rolled – may be able to be compacted to the proper density level by taking advantage of the three temperature zones which normally exist in that tender mix.
In the first, or upper, temperature zone, the asphalt concrete mix is relatively stable during the compaction process. Within the temperature range from laydown (320°F to 285°F, depending on the use of polymer modified binder and other factors) down to about 240°F, the HMA material is stable under the applied compactive effort. In this upper temperature range, the mix will not shove or check under the rollers regardless of whether a vibratory roller or a static steel wheel roller is used.
The lower limit of this upper temperature zone is not an exact value – it depends on the characteristics of the mix, the rate of cooling of the mat, the thickness of the layer, environmental conditions, and the type of roller used. In some cases, this value may be as high as 250°F or higher while in other cases it could be as low as 230°F or lower.
The middle temperature zone – the problem range – extends from approximately 240°F down to about 195°F. In this temperature range the mix will move, shove, and check under the applied compactive effort. A bow wave will form in front of the steel drums of the roller and the mix will crawl longitudinally. The mix will also move laterally or transversely and the mat will widen out if the edge of the roller is not positioned properly over the unsupported edge of the asphalt concrete mat by at least 6 in. In this middle temperature zone, the HMA material lacks the internal stability to support the weight of the steel wheel compaction equipment.
The lower temperature zone extends from the bottom of the intermediate temperature zone down to approximately 160°F or even lower. Within this temperature range the mix is cool enough to regain the internal stability necessary to support the weight of the compaction equipment. It is possible, but usually very difficult, to achieve the required degree of density within this relatively narrow temperature range if the mix has been de-compacted during the rolling of the mix when the mix temperature was in the middle temperature zone.
Compaction Options
To compact a hot mix asphalt mixture which has tender characteristics and moves under the rollers in the middle temperature zone, a contractor has one of two choices.
- All of the compactive effort can be applied in the upper and/or the lower temperature zones when the mix is internally stable and does not move, shove, or check under the steel wheel rollers. In this case, no compactive effort is applied to the mix when the mix temperature is within the middle temperature zone.
- If it is necessary to roll the mix while the temperature is within the middle zone, a pneumatic tire roller can be used because the mix will typically not shove in front of the rubber tires (as it will in front of a steel wheel roller drum in this middle temperature zone).
In order to compact a HMA mix that is stiff, it is necessary to roll it as close behind the paver as possible. In order to compact a HMA mix that is tender, it is also necessary to roll it as close behind the paver as possible in order to take advantage of the upper temperature zone in the mix.
For most asphalt concrete mixtures that exhibit tender characteristics, the tender mix must be compacted to as high a density as feasible, as quickly as possible. For most tender HMA mixtures that means placing two rollers on the mat within the upper temperature zone.
Two Double-Drum Vibratory Breakdown Rollers
Perhaps the most efficient way to compact a tender mix within the upper temperature range is to use two double-drum vibratory rollers in echelon (almost side-by-side). One double-drum vibratory roller can operate on one side of the mat and the other double-drum vibratory roller can operate on the other side of the mat.
In essence, when one roller moves toward the paver on one side of the lane, the other roller also moves toward the paver at the same time on the other side of the same lane. The rollers operate together, moving forward and backward at the same time on different portions of the mat. The purpose of this compaction process is to get as much density in the mat as possible before the temperature of the mix drops into the middle range and the mix begins to shove and move under the steel wheel rollers.
The exact roller pattern depends on many factors, including the width of each double-drum vibratory roller, the width of the lane being placed, the temperature of the mix immediately behind the paver screed, the temperature at which the mix starts to move and shove (the start of the tender zone), and the maximum frequency at which each vibratory roller can operate.
To adequately compact an asphalt concrete mixture, it is proper to extend the edge of the vibratory or static roller drum over the unsupported edge of pavement and/or over the longitudinal joint by at least 6 inches. Theoretically, therefore, one would need a 13-foot-wide roller to compact a 12-foot-wide pavement, allowing for a 6-inch overlap of the outside edges, whether unsupported or a longitudinal joint. Since no roller exists that is 13 feet wide, it is necessary to use multiple rollers of normal width to overlap the edge of the previous roller pass by a minimum of 6 inches.
Vibratory rollers used for most highway paving projects, for example, typically are manufactured in three drum widths: 66, 78, or 84 inches. If the width of the lane is 12 feet and the roller being used has a width of 84 inches (7 feet), then the whole width of the lane can be covered with two passes of the double-drum vibratory roller – one on the left side and one on the right side, allowing for a 6-inch overlap of both edges of the lane as well as a 6-inch overlap of the drum in the center of the lane.
If a narrower double-drum vibratory roller is employed, however, with a drum width of only 78 or 66 inches, then three passes of the roller are required in order to compact the whole width of a 12-foot-wide lane and still have the correct amount of overlap over the unsupported edge and/or longitudinal joint and between internal passes within the lane width.
Rolling in the Tender Temperature Zone
If only one double-drum vibratory roller is available and if a pneumatic tire roller is available, then the rubber tire roller can be used in the intermediate position in the tender zone. The vibratory roller should make as many passes as possible over the width of the lane before the temperature of the mix drops to the point that the mix starts to move and check with an additional roller pass. Once the mix starts to shove and de-compact under the drum, all compaction with any steel wheel roller – operated in either the vibratory or static mode – should cease.
An asphalt concrete mixture, even a tender one, does not normally shove in front of the tires of a pneumatic tire roller. The rubber tires on this type of roller tend to tuck the mix back under the tires instead of shoving it forward. Thus, in the middle or tender temperature zone, a pneumatic tire roller can be used to accomplish what a steel wheel roller cannot do – compact the mix.
It is important to note, however, that it might be difficult to use a pneumatic tire roller in the middle temperature zone on some polymer modified mixtures, particularly if the mix has been modified using a latex (styrene-butadiene rubber) type material. Pickup of the mix on the tires might be impossible to avoid in some instances.
If a pneumatic tire roller is used in the intermediate position on a tender mix, it will be necessary to use a static steel wheel roller to complete the compaction process. The finish roller is employed to remove the marks of the rubber tire roller and to increase the density of the mix to the final, required level.
Care must be taken, however, that the finish roller does not operate in the middle temperature zone and actually de-compact the mix instead of compacting it. The static steel wheel finish roller should be moved closer and closer toward the back of the rubber tire roller until the mix starts to move or shove under the drums. This is an indication that this roller is inside the middle or tender temperature zone. If this occurs, the finish roller should be kept farther back from the intermediate roller and operated completely within the lower temperature zone.
Using this roller pattern to compact a tender mix is not as efficient as using the two double-drum vibratory rollers in echelon in the breakdown position since three rollers are needed – a double drum vibratory breakdown roller, a pneumatic tire intermediate roller, and a static steel wheel finish roller. This pattern, however, can be used, if necessary, to obtain the required level of density in a tender mix.
James A. Scherocman, P.E., is a consulting engineer who, in addition to being a regular presenter at educational conferences such as National Pavement Expo, can often be found arbitrating project conflicts between contractors and public agencies. He can be reached at 11205 Brookbridge Drive, Cincinnati, Ohio 45249 or at [email protected].