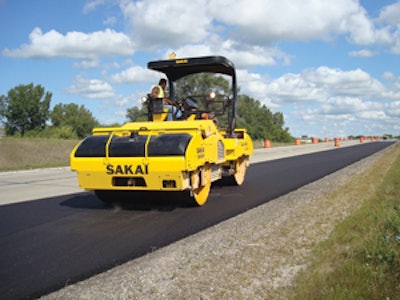
Whether new or used, equipment needs to be in top operating condition to be most productive. Take a ride-on vibratory compactor, for example. In order to produce a smooth mat with the desired density, all critical components need to be in good working order.
"All equipment is bright and shiny when it leaves the factory," comments Bruce Monical, Wirtgen America. "But no matter how good it is, if it's mechanical, it will eventually wear out."
The single biggest influence on how quickly that happens is maintenance. "If you follow the recommended maintenance procedures for your particular compactor, you should be able to extend the life of the machine," says Monical. "And that also influences the performance, because the better the machine is maintained, in general, the better it will perform. If the engine doesn't 'miss', if the pumps don't surge, if the drums are smooth and not pitted, if the water system is clean and provides a constant spray of water to the drum - all of that will improve the job because the performance of the machine is what it should be."
Keep it serviced
Maintenance of the engine and hydraulic system components is particularly critical. "In order for a hydraulic vibratory system to have the proper output to compact the asphalt, the engine has to run at its specified rpms," notes Dave Dennison, BOMAG. "If the engine isn't turning fast enough, the hydraulic system won't perform as designed and your vibratory performance will be diminished."
Using clean, high-quality lubricants also plays an important role in reducing wear, lowering operating temperatures and obtaining the maximum service life from components.
"Keeping the cooling system clean contributes to the lowest possible operating temperatures, which helps prolong the life of lubricants, seals and components," says Tim Sturos, product support supervisor, Caterpillar Global Paving. "Improper maintenance can lead to contaminated hydraulic oil and high operating temperatures, which cause increased wear and poor performance."
Fluid analysis will help you to more easily track lubricant condition. "Regular oil sampling helps establish the condition of the lubricants," says Sturos, "and guides equipment managers in making optimal maintenance decisions in order to avoid unscheduled downtime and excessive maintenance costs."
To ensure optimal mat quality, pay attention to the water system; in particular, make sure the scrapers on the drums are adjusted properly. "They have two functions," says Bob Marcum, Volvo Roadbuilding. "The first is to distribute water evenly across the drum. The second is to remove any material that might stick to the drum. If they're not properly adjusted, they won't do either function in an optimal manner."
Operate rollers appropriately
Operating procedures greatly affect the life cycle of a compactor. "Jumping curbs, driving rather than ramping the roller off the trailer, quickly moving from forward to reverse, breaking up concrete blocks, etc., can all damage the machine," says Monical. "If you use the roller the way it's designed [to be used], on jobs it's designed to do, you will positively influence how long it lasts."
Over compaction can also have negative repercussions on roller longevity. "The energy that you create in the drum has to go somewhere," Marcum points out. "If the material won't absorb it, then it comes back into the machine. That feedback, or energy, has a high potential of damaging the isolators that allow the movement of the drum. It can also cause premature damage and wear to the bearings." To minimize and/or eliminate over compaction, establish a rolling pattern for each job and verify it through testing.
When maintenance isn't enough
Even with an optimal maintenance program and proper operation, you may be forced at some point to make the decision between making a major repair and replacing the unit. When an existing compactor becomes more costly to repair than to purchase, or when it experiences excessive downtime, it's likely a better option to purchase new.
"And if you ever get to the point where a machine poses a significant safety problem," says Dennison, "that's another reason to upgrade to a new unit."
When determining whether to repair or replace, take into account the costs of parts, labor and downtime required to maintain or rebuild a unit nearing the end of its service life. "Certain components may be very expensive to replace, such as heavily worn drums," says Sturos. "Consider, too, that certain replacement components may no longer be readily available or available at an economical cost."
Also ask yourself if the compactor still allows you to meet job requirements in terms of size, width, tonnage and production goals. "Essentially, ask if your current roller can keep up with the paver in production," says Marcum.
With manufacturers continuing to introduce new approaches to the compaction process, you may find that the benefits in terms of mat quality and productivity quickly offset any cost advantages of repairing an existing model.
Some new models also include an onboard mat temperature gauge that allows the operator to monitor how quickly the asphalt is cooling. "The gauge is right on the machine, so the operator doesn't have to rely on a temperature gun or someone else to check readings," says Dennison. "We also have an impact spacing display to provide immediate feedback, so operators know if they have to adjust their travel speed."
In addition, manufacturers have focused on improving engine management with Tier III and ultimately Tier IV engines. "We can manage the engines more efficiently for better fuel consumption, while maintaining the power needed to run the hydraulic system," says Marcum.
Read more roller maintenance tips at "Tips for Keeping Rollers Maintained for Longevity and Performance".
Kim Berndtson is an editor for Equipment Today magazine