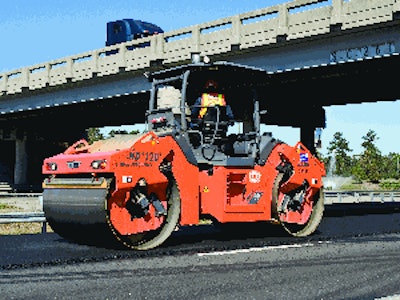
On a project In South Carolina, two high-frequency HD+ 120 VV HF rollers from Hamm Compaction Division were teamed with a Hamm HD+ 120 VO Oscillation roller to effectively accelerate placement of a 140,000-ton Interstate overlay last summer, eliminating a fourth roller in the process and delivering results for the contractor.
For this 17-mile northbound project on I-95 near Manning, asphalt paving contractor C.R. Jackson Inc., Darlington, S.C., matched a 10-foot Vision 5203-2 wheeled paver from Vögele America Inc. to the three Hamm rollers.
"The breakdown roller and intermediate roller are used in vibration, and the oscillation roller is being used more for ride quality than compaction," says Kael Morris, project supervisor for C.R. Jackson. "It effectively takes out a lot of the roller marks our operators may put in the mat, and tends to increase the smoothness of the mat more than a static roller."
Oscillation, in this particular operation, is used for this finish rolling. A fine finish is critical, as the contractor must completely meet the smoothness spec of 40 I.R.I. or incur a penalty. "We also used oscillation on our cross-slope correction and profile leveling, and it performed well there also. But for finish rolling, I like the outcome better than that of a static roller."
Oscillation compaction is a non-aggressive means of compacting pavements because it compacts with a gentle rocking motion, not a vertical pounding. Unlike conventional vibratory compaction, which works by "bouncing" the drum on the surface, Hamm oscillation technology ensures that the roller drums maintain constant contact with the surface for faster, more effective compaction.
In the oscillation drum, two eccentric masses turning in the same direction cause a movement around the drum axle. The movement changes its direction of effect during one turn so it generates an oscillating or rocking movement of the drum. Horizontal forces are transmitted from the drum into the pavement, and the result is better compaction in fewer passes, with less vibration-related wear and tear on operators and surroundings.
Reducing the number of rollers
With the rollers employed on the interstate project, C.R. Jackson was able to reduce by one the number of rollers required to achieve results.
"Our Hamm rollers are working really well," Morris says. "Normally, with the daily production we have been meeting, we would have used four vibrating rollers, with one running static in the back. But we now are getting the above-standard compaction numbers with the three rollers. In dropping one roller and maintaining production, we have been able to save money on labor and equipment."
The new construction project specifies minimum 92.2% density on the mat and the Hamm HD+ rollers were helping C.R. Jackson get there.
"It's an attainable requirement for an Interstate where you normally have a decent subgrade," Morris says. "There is a bonus for compaction, combined with lab test results. We can get up to 105% total pay by meeting all the requirements set forth in the contract."
Paving over repaired PCC
The existing surface was Portland cement concrete, dating to 1964. Beginning in February 2009, prior to paving hot mix asphalt, C.R. Jackson repaired the existing concrete pavement.
"We removed and replaced the concrete areas that were broken, cracked or settled and then began correcting the cross-slope and profile with asphalt. The existing surface was typically a 96:1 cross-slope with many areas being flatter than that. We increased the slope to a 48:1 on the tangent sections, and corrected the curves to meet their individual requirements," Morris explains.
On this rehabilitation project, asphalt has been placed up to a depth of 7 inches at the center of the road to correct the cross-slope and strengthen the roadway. "The first two lifts were cross-slope correction, followed by a strengthening [intermediate] course, a surface course, and a friction course for water drainage," Morris says. "We are also having to place borrow material along the shoulders to correct the drop-offs.
"The mix is what used to be called a 12.5mm Superpave mix, Surface Type A with PG 76-22 polymerized liquid asphalt," Morris says. "The mix has been very stable, with no real tender zone so far. I give credit to my QC manager; he has done a great job setting the mix up at the plant, because with a little too much or too little rock this mix has been known to slide around on you."
The project was to be wrapped up by Nov. 30, but in early October, the region had been hit by an early frost. "It forced us to change our times," Morris says. "We had been working nights, but the cool weather has forced us to daytimes. We are allowed 24-hour lane closures starting Sunday nights through Friday mornings," Morris says. "On weekends, we are only allowed to work nights."
Ultimately an open-graded friction course will be placed on I-95, but that work likely will take place in the spring of 2010.