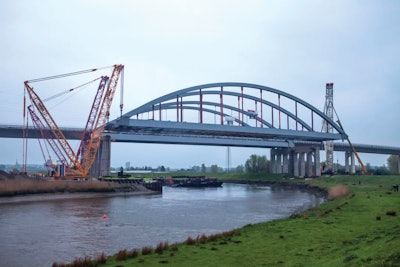
The challenge:
Lift a 393-foot-long tied-arch bridge onto 65-foot-tall piers over a river to close a gap in the expansion project for the A23 motorway between Hamburg and Heide, Germany.
The players:
Ulferts & Wittrock
Wagenborg Nedlift
Sarens
The process:
Crane service providers Ulferts & Wittrock, Wagenborg Nedlift and Sarens worked together to lift a 393-foot-long tied-arch bridge onto 65-foot-tall piers, closing a gap in the expansion project for the A23 motorway between Hamburg and Heide. In order to perform this challenging lift over the river Stör, the companies relied on a trio of Terex crawler cranes: Wagenborg with its CC 2500-1; Sarens with its CC 6800; and Ulferts & Wittrock with its new Superlift 3800, which was on its first assignment for the company.
Despite the complexity involved in performing a lift with three cranes, Ulferts & Wittrock focused on one main criterion when deciding on which crane to use for the project: “This new crane allowed us to eliminate the costly and time-consuming process of having to build an auxiliary structure,” explains Albert Schrör. Before the cranes started their work, however, the 1,322-ton bridge first had to be positioned so that it would be ready to be lifted - a process that also required considerable effort. During the first step, two modular heavy haulage vehicles moved the steel giant to the designated place on the river bank, where a pontoon waited. The vehicle in the front then drove onto the pontoon together with the bridge, after which the rear vehicle pushed the pontoon, together with its load, to the other side of the river, where yet another one of the heavy haulers was ready to “receive” it.
Once the bridge was placed exactly where it needed to be and was aligned parallel to the piers, the teams were able to sling the load. On one side of the river, the Sarens team setup its CC 6800 crane with a stationary SSL 50 configuration, which picked up 661 tons of the bridge’s weight. On the opposite bank, Wagenborg’s team setup its CC 2500-1 crane with an SSL 42 configuration and equally split and picked up the remaining 661 tons with Ulferts & Wittrock’s new Superlift 3800. The Superlift 3800 crane was set up with an SSL 42 configuration featuring a 137-fott main boom and a superlift tray. The counterweight was 110 tons on the vario-superlift tray and 165 tons on the superstructure. In addition, the crane was equipped with a vario-hook with 10-part reeving for this specific lift. “We had very high expectations when it came to the new Terex Superlift 3800’s first assignment, and were really looking forward to seeing how the ‘new kid in town’ would fare in its debut,” Schrör said.
The company was not let down in the least bit. In fact, the new crane, designed for cost-effective transport, literally paid for itself as it only needed 20 trucks to bring all of the crane’s components to the jobsite. For example, the superstructure, with the assembled carbody, fit on a single transport vehicle. This not only eliminated the need for an additional truck but also helped the team save time during setup. In addition, the platforms and handrails placed all around proved to be very advantageous for the assembly technicians, who did not have to awkwardly walk on the crane’s tracks during setup. The tracks, in turn, delivered outstanding handling performance at the worksite thanks to their especially wide design, which provide reduced ground pressure.
Lift under adverse weather conditions
The challenge when carrying out this type of lift is twofold: The load has to be perfectly balanced, and all the cranes need to be flawlessly synchronized. This is where the Terex IC-1 crane control system, featured on all three cranes, proved to be indispensable. “The IC-1 control system made sure we were able to keep tabs on the way the weight was distributed at all times,” Schrör said. “The new Superlift 3800 not only has unbelievably precise controls but also responds perfectly to every input."
This enabled him, as well as his fellow operators in the other Terex cranes, to lift the bridge with the necessary precision to the required height of 65 feet and place it on the concrete piers with a single, smooth slewing movement. And even though rain kept trying to put a damper on their plans throughout the entire lift, the operators were able to do everything as planned. After about 5 hours, the job was completed as scheduled and another gap in the expansion project for the A23 autobahn had been closed.