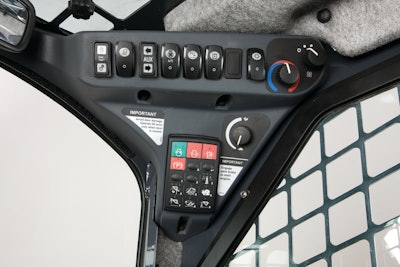
Compact machines are becoming “smarter” as the electronics available on modern hydraulic and engine systems are being integrated with software to increase productivity and slash fuel consumption. New features and options simplify operation and reduce operator fatigue. And as new technologies such as telematics expand into the compact equipment market, expect the importance of electrohydraulic (EH) controls and software-driven features to grow.
More features are being offered on machines today due to control technology advancements. “Prior machines had mechanical and hydraulic control of the lift, tilt and auxiliary functions,” says Mike Fitzgerald, Bobcat. These controls are limited in what features can be added. When hydraulics systems are controlled by pilot controls, the operating characteristics can only be changed by changing the pressure or flow through the control.
The development of EH controls made possible the ability to offer customized solutions. “There are things we can do with electronic controls to help the customer operate the machine more efficiently,” says Fitzgerald.
Technology is rapidly evolving. “The days of just having cables and levers are so antiquated, and that was only three to five years ago,” says Vincent Whelan, JCB. “Now if you look at those machines, they seem really archaic compared to what you have today in terms of the trend to automated functions.”
The end user is seeing a much more technologically advanced, efficient and productive machine. The cost of ownership is also lower, though that is a long-term benefit due to the higher initial purchase price, according to Whelan. Part of the savings is due to increased fuel efficiency. By having precise control over the engine and hydraulic system operating parameters, you can maximize fuel efficiency for the specific task at hand.
Trends Drive Market to EH Controls
There are a few trends driving the movement toward EH controls and the associated features available through software. They include a desire to offset the increased cost of compact equipment due to emissions regulations via increased productivity and fuel efficiency; the need to compensate for less skilled operators; and rising customer expectations.
Let’s start with emissions requirements. Tier 4 has added up to 20% to the initial purchase price of many compact machines. To offset this increase, manufacturers are busy developing productivity enhancing features. Many of these features are based in proprietary software that enhances machine performance through the electrohydraulic and engine electronic control systems. For instance:
- hydraulic response rates can now be set to individual preferences;
- cruise control allows maximum machine travel speed to be set independent of engine speed to provide maximum hydraulic pump output;
- auto idle saves fuel;
- return-to-dig and tool positioner features ease operator work load;
- and engine anti-stall simplifies operation for novices.
These features just scratch the surface on what is currently available and what is possible.
Manufacturers and their suppliers are working closely together throughout the product development process to design integrated systems solutions.
Danfoss provides EH system solutions to a majority of the manufacturers who supply compact construction equipment. “Especially over the last three years, we have seen OEMs coming to us and saying, ‘We have had to charge our customers a lot more for emissions, but we have to give them something else to justify that cost increase,’” says Eric Bretey, manager, advanced systems engineering, Danfoss. “It usually comes in the form of ‘Is there something we can give in terms of productivity or some smarter way they can use their machine by giving them something in software?’”
Many manufacturers now deliver enhanced productivity features. “We needed to come up with some good ways to give something back to the customer in terms of advancing our machine forms and technology to increase their productivity, so they are more willing to accept the higher prices that go along with that engine,” says Greg Zupancic, product marketing manager, John Deere Construction & Forestry.
The cost increases are unavoidable. “End users are beginning to see clarity that Tier 4 is not something they can avoid,” says Whelan. “You have end users saying, ‘I am paying more over Tier 3. What is my benefit?’”
Then, contractors must consider the differences in skill levels between operators. “A lot of the operators using these machines today are not as technically skilled,” says Bretey. “We hear a lot of OEMs ask us, ‘Can you give us a solution that will make it easier for a new operator to be productive more quickly?’ That involves using a lot of the interfaces that they are already used to, like their smartphone.”
Finally, customer expectations are changing due to technology. “They want easier, more comfortable to operate, less fatiguing machines,” notes Fitzgerald.
The automotive market is partially responsible for the changing expectations. “When the machine operator drives to the shop in the morning, he is in his brand-new Ford F-250 or Chevrolet Silverado and he has all of the technology involved with one of those trucks in the cab,” Bretey explains. “He then expects when he gets into the cab of a machine to have a similar experience. Operator expectations are getting higher and more sophisticated. Along with that, there are all of these things the technology now enables us to do.”
The trick is to simplify the information and provide operators with only what they really need. “We don’t want to overwhelm them with 23 dials or 50 buttons and switches,” says Bretey. “We need to give them what they need to do their job and not distract them from it. That’s all about productivity.”
Software as a Solution
So why is software the solution? Because it has the ability to dramatically improve productivity in certain applications without adding significant cost. “It doesn’t cost anything in hardware,” says Zupancic. “The real investment is the guy writing the code. There is a cost in the switch and wires, but that is typically very low.”
Electronic control features on the latest-generation skid-steer and compact track loaders allow the operator to customize machine response to personal preferences and optimize machine efficiency. These controls go far beyond the ability to merely switch between the preferred H or ISO control patterns.
Many of the features are the result of the continued movement to EH controls. “Once you have the basic drive-by-wire technology (EH controls), then a lot of the electronic features are just programming,” says Zupancic.
JCB is also moving toward standardization of EH controls. “It seems to be that all of our competitors are following the same route,” says Whelan. “Ultimately, we benefit as a manufacturer with this optimization.”
The machine can be optimized around the EH control layout and then adapted to mechanical controls for those market segments that require it. By standardizing on a single global platform, the manufacturers can better control cost and quality.
The move toEH controls makes it easier to implement new options. “Before, there were a lot of hydraulic- or manual-only systems. But the improvement of electrohydraulics is also opening the door to a lot of capability that we could not do before,” says Bretey. Electrohydraulics allow precise control of the machine, improving productivity and fuel savings.
“Once you have established that you are going to electrohydraulics on your machine, you have all kinds of options,” says Russ Peters, engineering manager, Propel Systems Development Test Lab, Danfoss.
Manufacturers are looking at software development to offer unique productivity features. “At John Deere, one thing that differentiates us is we have our own proprietary software,” says Zupancic. “We have our own team to write code for us. The big players in the industry have that capability and have been doing it for years. It makes sense if they already have the in-house software programmers that they continue to move in that direction to own that intellectual property to have some pricing power related to it.”
Customers will realize tangible benefits from software advances. “If at the press of a button you can make the machine do a certain function that will make the operator be more productive, it takes the physical effort out of running the machine,” says Zupancic.
There are many different approaches to market the new software-driven features. For instance, John Deere offers an EH Joystick Performance Package as an add-on option to its EH joystick control. The package is available for around $750 on any John Deere skid-steer or compact track loader equipped with EH controls, and comes as a factory option or field-installable kit. A Creep Mode, switchable control patterns, adjustable boom/bucket speed settings, and adjustable propel response rates are all included as part of the package.
Bobcat takes a different approach with its Selectable Joystick Controls (SJCs). These EH joystick controls have evolved over the past decade, and offer a full gamut of features that were available well before the move to Tier 4 emissions standards. Features include Speed Management, where the operator can match machine speed to the attachments, drift control and adjustable hydrostatic drive response rates.
“We try to give customers the features that will benefit them right from the start without having a software upgrade to change things,” says Fitzgerald. “We have always given them a very large base package when they select the joystick option. It may also involve some software tied into that, but customers are not just buying a software upgrade package from Bobcat.”
Although Bobcat had its SJC package in place prior to the latest emissions requirements, a new feature has been added during the transition. “With the addition of an electronically controlled engine, we can now add Auto Idle,” says Fitzgerald. “We didn’t have that before because we had a mechanical throttle. Today, we have an electronic throttle.”
Auto Idle can be tied into the joystick controls because it is electric. “When you have a manually controlled machine, you do not have Auto idle available because you don’t have the sensors needed to be able to read where the control settings are,” Fitzgerald points out.
A Tale of Two Markets
There are two distinct markets emerging for compact machines: one for a basic machine and another for a high-end machine with many productivity enhancing features. So don’t expect manual or pilot controls to disappear anytime soon.
Rental businesses are typically price sensitive and therefore often prefer mechanical linkages. “A rental company cannot charge more for electronic or software features,” says Zupancic. “So they buy a machine with basic mechanical linkage controls.” To serve this large market, even manufacturers that optimize their machines for EH controls are offering mechanical and/or pilot controls.
Bobcat sells three different control systems to meet customer demands. “Some operations that are more cost conscious or where machines are used more for utility purposes may want a lower cost,” says Fitzgerald. But he notes that not all rental companies buy strictly on price. “We have some rental operations that buy our joystick controls because that is what their rental customers are requesting.”
Whether you can benefit from advanced software features available with EH controls depends on your application. “If you are just going to move dirt all day with your skid steer, even if it is a big machine, you might not want to buy these features,” Zupancic indicates. “But if you are going to be grinding up a lot of asphalt or concrete with a cold planer, an EH Performance skid-steer package is perfect for that type of application. You can get a return on your investment real quick.”
Expensive, hydraulically driven attachments are well suited for this technology. Travel speed and hydraulic flow can be tailored for maximum productivity. “It does help the return on your investment for attachments,” says Zupancic.