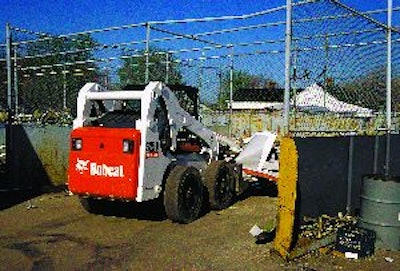
Skid-steer loaders are tough on tires. The sharp turns, difficult working conditions and spinning wheels often associated with these utilitarian machines can shave days off of tire life. Excessive wear, however, can be minimized by selecting the right tires for the application and by following proper operating procedures and preventive maintenance practices.
"Skid steers by nature are designed to wear tires, because the wheels are constantly counter rotating against each other to provide a full turn radius," says Gregg Zupancic, product marketing manager, John Deere Worldwide Construction & Forestry. "An operator can significantly reduce tire wear by limiting the amount of tire counter rotation (tight turns) and not allowing tires to spin when excavating or loading material."
Scott Sloan, product engineering manager, Titan Tire Corp., agrees, noting, "The operator has more effect on the wear and condition of tires than anything else. Operators with a softer touch and those who take wider turns when they can will certainly extend the life of their tires."
Spending dollars spinning tires
Tire life also depends on the application, says Mike Fitzgerald, Bobcat product specialist. "As a rule of thumb, a general contractor who is operating on a combination of dirt, roads and parking lots will likely get between 600 to 800 hours of life out of the tires. A landscape contractor who operates almost entirely on dirt may get between 800 to 1,200 hours," he states. "Owner/operators, because they are very conscientious about costs, may get 1,400 hours out of a set of tires.
"Conversely, a demolition contractor in severe operating conditions may get only 400 hours," he adds.
No matter what the application is, it pays to train operators to make the tires last longer.
"Accelerated wear is mostly caused by operator error and improper use of the machine," says Emily Epperson, company marketing director, TY Cushion Tire. "Spinning the tires is the biggest problem, and the potential repercussions for contractors can be very costly - downtime, the cost of repair or replacement and loss of business."
To reduce such risks, train operators on steps they can take to extend tire life. "When working on asphalt or concrete, it's advisable for operators to make their turns prior to getting on the hard surface, if possible," Fitzgerald states. "Otherwise, sprinkling the surface with dirt or sand will help minimize tire wear. Also, avoiding pushing extra-heavy loads will cut down on spinning."
Extending tire life is akin to putting money in the bank. "A very basic, standard-duty tire will cost under $100, but prices go up from there," he states. "Heavy-duty and severe-duty tires can range anywhere from $150 to $200 or more per tire, and solid rubber tires can cost anywhere from $800 and up."
As Zupancic points out, tire costs represent 15% to 20% of the overall operating cost of a skid-steer unit. "If you see your tires spinning," he says, "you're just spending dollars."
Prevention strategies
Keeping tires properly inflated will help maximize tire life on your skid-steer loader, just as it does on vehicles in your fleet. "The air in the tire is designed to carry the load," says Sloan. "If the tire pressure is too low, the tire will flex more than it should. This puts undue stress on the tire and increases wear.
"Inspect your tires daily, remove any loose debris, and watch for signs of wear," he advises. "With a lug design, for example, as the tire wears, the tread will become shallow in the center. The shallower it becomes, the less traction the skid steer will have."
Proactively replacing tires as needed will keep the skid steer from experiencing downtime, adds Kirk Dilly, Gehl product training specialist. "When inspecting tires, look for signs of cracking (indication of dry rot) or missing chunks and knocked-off tread. Both are signs of tires that have pending failure," he points out.
According to Dilly, larger machines will wear tires faster than their lighter counterparts because of their extra weight. Therefore, owners of larger skid steers need to look at higher quality tire options.
Zupancic also notes, "Removing counterweights when not needed will help reduce wear, and strive to keep tire wear even."
Match tires to the application
Operators can choose from several tire types and configurations to match the application. "For most applications, the standard pneumatic, air-filled dirt tire would be a good selection for general-purpose type of dirt work," says Zupancic. "If working in demolition or a harsh environmental application, adding foam or gel materials to these tires would remove the possibility of flats.
"If working in soft conditions where flotation is needed," he continues, "a wider, less abrasive style may be more suitable. Then there are solid rubber tires and those with cushioning features or holes drilled into the sidewalls to provide solid rubber durability and a ride close to that of an air-filled tire. For snow removal or concrete work along roadways, operators can select hard surface tires that provide higher ground pressures and lower wear characteristics."
Pneumatic tires come in three basic configurations. A standard-duty tire is very basic and designed for low use. Heavy-duty tires are constructed with a special rubber compound that helps to minimize wear. Severe-duty tires have more rubber and depth, which means more wear surface.
"For most applications, a heavy-duty tire provides the best value," says Fitzgerald. "If conditions call for poly filling tires to eliminate flats, be aware that the foam, gel or poly material can 'weld' itself to the rim and make it costly to replace the tire. Recapping the tire may then be appropriate."
Having a flat tire is never a good experience, and depending on the application, it can be very costly.
"You can ask owner/operators how much time and money a flat tire will cost and they may say, 'Oh, about $20 and the time it takes to go to the service station and have it plugged'," Fitzgerald comments. "Larger contractors tell a different story, especially if the downtime involves shutting down an entire crew for half a day. Then you're talking several hundred dollars."
All tires are not alike
"Tires can look the same, but they're not," Sloan points out. "Ply, deck gauge (the amount of rubber that extends between the bottom of the lug into the casing) and sidewall gauge help distinguish one tire from another. Skid depth (the actual depth of the tread) is another important quality. In the skid-steer world, skid depth translates into tread life. If a tire's tread is 20% deeper than another, one could reasonably expect 20% more life out of that tire."
Of course, there are cost trade-offs. "An inexpensive tire with less skid depth, less deck gauge and less sidewall gauge may last 400 hours for a particular application," Sloan states. "A more expensive tire - one with more rubber - may cost 20% to 30% more, but lasts longer. Most owner/operators who make a living with their machines understand the math and are willing to pay the additional cost up front."
Different tire types have their pros and cons, as well. "Regular tires, with dirt lug-type tread, are by far the most popular. They wear and ride fairly well, and they are self-cleaning," notes Dilly. "Solid rubber tires are a good option in applications where pneumatic tires would get punctured (e.g., recycling). However, they don't ride nearly as well because they lack pneumatic suspension qualities."
Zupancic agrees, adding, "A skid steer does not have a suspension system, so the air in the tires is oftentimes the only source of cushioning for the ride. Once the air is removed, the cushioning is gone. A solid rubber tire can make operation a little less comfortable, but the trade-off is durability. It can be three times more expensive than a basic dirt tire, but a solid-rubber tire can also provide three times the return on the initial investment through durability and longevity."
TY Cushion Tire has been developing and producing solid cushion tires for more than 40 years. "Solid tires have many benefits," says Epperson. "Downtime, if any, is minimal. There are no cuts, punctures, blowouts, or damage from normal wear. Solid tires are most effective in extreme applications where these common issues are present."
She continues, "Different tread designs are effective for specific things like mud/dirt disposal, wet conditions or uneven surfaces. The initial purchase price is higher. However, solid tires are a better investment over time because of the extended wear and longer life expectancy."
Adds Dilly, "Severe-duty tires combine the best of both worlds, although they are still susceptible to puncture and do not clean out as well in dirt and mud applications."
Understand the options
Don't ignore tire size and rating, Sloan stresses. "Manufacturers most likely specify a tire because of the size and load capacity of the machine. Substituting a lighter ply tire may save money at the time of purchase, but the tire will have less load capacity, less inflation pressure and will be under more stress than it was designed for in that application," he says. "In other words, it will wear out faster and be more likely to fail on the job."
It's important to understand your options, as well. In addition to a choice between tire types and ratings, operators can also select different treads. "If the skid steer is going to be used more than 50% of the time on asphalt and concrete and 20% to 30% of the time on dirt," notes Sloan, "then operators may be more productive with a tread more suited to concrete and asphalt work. Conversely, if they're going to be in dirt all the time, then an industrial tread would be ideal."
Sloan adds that some contractors who have cross-over applications actually have two sets of tires - one with rock tread and one with lug tread. They are opposed to giving up performance because they don't have the best tires for the application, and would rather take the time to change out the tires.
"When it comes to your skid-steer loaders, not just any set of tires will do," says Epperson. "Certain types of tires are more effective. Using an industry-specific tire made for select applications is best. You must match the tire (tread, size) to the application and usage conditions."