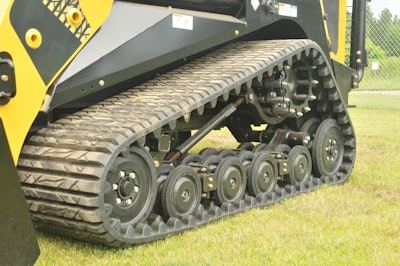
If you have compact track loaders (CTLs) in your fleet, then you know these machines are real workhorses. But they can go a lot further and do a lot more with the right tracks to run on.
When selecting tracks for your compact track loaders, the first step is to consider the application the machine will be most often used for. Lysandre Michaud-Verreault with Camso, maker of OEM and aftermarket tracks, advises choosing a track based on the sort of catastrophic events that could arise under your normal working conditions — in other words, the worst-case scenario — and use that as a baseline. For example, if your machines are most often used in turf applications, you won’t have the same potential for failure as you would if your machines are typically used in demolition settings.
Secondly, think about weather, terrain and other variables that may influence track choice. “Wide tracks with deep treads do better in marshy, snowy and icy conditions than standard tracks because of the increased traction and lower ground pressure,” notes Bill Wake, director of product development, ASV. “Use tracks with little or no tread when turf damage is a concern, such as on golf courses or manicured lawns. Standard tracks are effective for most common applications.”
Style Matters
ASV uses rubber tracks on all of its models, but most other manufacturers’ CTLs use rubber track embedded with metal pieces and steel cable to increase durability. As such, Wake says it’s important to choose the correct style of track for the specific machine. Also check the equipment manual to pick the correct size of track.
Each track manufacturer offers unique features to extend the life and increase the durability of its tracks.Camso
She notes that each track manufacturer offers unique features to extend the life and increase the durability of its tracks. Camso, for example, offers its CTL SD tracks featuring single-cure technology for even tread wear and long, predictable tread life. An optimized zigzag tread pattern maintains traction throughout tread life, while endless high-tensile steel cables help to eliminate unexpected downtime due to cable/track breakage. The Trackguard iron core improves rolling path life for enhanced durability.
The Camso CTL HXD heavy-duty tracks feature an optimized H-type tread pattern and endless high-tensile steel cables to handle severe applications.
ASV offers three styles of rubber tracks with different tread depths. The aggressive style has a deep tread for maximum traction, while the standard is effective for everyday applications. Turf tracks have no tread at all for minimal turf damage in highly manicured areas such as golf courses or lawns.
Check for Quality
According to Wake, the most reliable way to ensure tracks are of high quality is to buy directly from the original equipment manufacturer rather than choosing lower-priced aftermarket tracks.
He advises, “Look for tracks that contain embedded co-polymer cords for extra strength, and that are manufactured with circular press technology and produced using a single-cure process, eliminating cure-point weaknesses in the track that can lead to premature breakage.”
Michaud-Verreault adds that quality is mainly determined by the components of the tracks. “The difference is not visible to the eye — except for the tread pattern — and goes back to rubber compound, carcass thickness, iron core and the alignment of steel cables.,” she states. “What’s most important when selecting a CTL track is to match it with your application and its severity, which will determine the quality level you will need.”
What’s Under There?
In addition to the tracks themselves, there’s the undercarriage to consider. There are two types of undercarriages: rigid and suspension.
Michael Shebetka, product manager, Takeuchi-US, explains that in a rigid-mount frame, the left and right track frames are bolted or welded to the main frame. A suspension undercarriage, on the other hand, uses movable track frames supported by torsion springs or in some cases rollers suspended by a leaf spring.
Undercarriage inspection should be a routine part of your maintenance discipline in order to maximize the life of your machine’s tracks.
It’s important to pick the undercarriage that best suits your daily needs. No matter how well you maintain your machines, any type of undercarriage with moving parts has expensive wear items that will require maintenance and replacement over time.
Operation is a Factor
In addition to the type of work the machine will be doing, the operator plays an important role. Improper or aggressive operation is a major contributor to excessive wear, says Wake.
“To minimize damage, train users on proper operation before they utilize the equipment,” he emphasizes. “Counter-rotations, or sharp changes of direction, are a big cause of premature track wear. This is especially true when driving over highly abrasive material, such as shale, granite or ragged materials commonly found on demolition sites.
“Encourage operators to use three-point turns to avoid cuts in the track often caused by counter-rotations,” he continues. “Operators should also avoid spinning the tracks, especially on abrasive surfaces. Like counter-rotations, spinning can result in cuts in the rubber and unnecessary wear.”
Improper operation and extreme underfoot conditions can result in cuts or chunking of tracks. Image provided by ASV
Improper track tension. Refer to the recommendations in the OEM manual or check with your local dealer.
Operation on hard, rough terrain. This can cause cuts or chunking of tracks and lead to excessive, premature wear. For this type of application, a skid-steer loader might be the best choice.
Riding over curbs. This can also cause cuts and chunking that expose internal steel cables, which can let moisture penetrate and cause the cables to weaken and eventually fail.
Demolition debris underfoot. Skid-steer tires can run right over demolition debris (rebar, concrete, sharp objects, etc.), while the same debris is very hard on tracks.
“We also advise running up and down slopes instead of across, and staying on as flat a surface as possible so the machine does not lean heavily to one side,” says Shebetka. “Leaning puts pressure on the idlers, rollers and sprockets, resulting in premature wear.”
Take Care of Your Sprockets
It’s no surprise the most important variable in getting the most performance and uptime out of your tracks is regular and meticulous maintenance. With this in mind, undercarriage inspection should be a routine part of your maintenance discipline.
“Regularly inspect the track,” Wake recommends. “The average ASV rubber track life is about 2,000 hours but can be as high as 5,000 if maintained well. On the other hand, neglecting a rubber track can result in a wear life as low as 500 hours. To get the longest track life, check track tension and condition daily.”
Many common problems associated with rubber tracks stem from improper track tensioning. “A track that’s too tight can accelerate wear on the track as well as on bearings, wheels and sprockets,” says Wake. “Alternatively, a loose track can result in ratcheting — lugs skipping over sprocket rollers — which accelerates wear or damage to the lugs. A loose track also increases the risk of derailment.
“Make sure the track tension matches what is listed in the equipment manual,” he stresses.
To some degree, ground conditions can dictate the frequency of inspections. “Despite an undercarriage’s all-weather versatility, snow, mud and sand can get into and pack the undercarriage, which increases track tension,” Shebetka says. “In colder environments, material can also freeze inside the track.”
“Florida is a prime example of how a maintenance schedule can vary,” he continues. “Most of the state consists of sugar sand, which becomes airborne around a working machine. It fills up the bottom of the chassis, plugs filters and can prematurely wear out an undercarriage if the tracks are not tensioned properly for this type of ground condition. A majority of the time you want the tracks to fit tight; but in the case of sugar sand, the tracks should be loose.”
When selecting a CTL track, it's important to match it with the application and its severity.
A more thorough inspection of the complete undercarriage and sprockets should be done when it’s time to change out a track, notes Michaud-Verreault.
Camso has been studying track life and the causes of track failures for many years. “When you find premature wear or damage to the track of your compact track loader, it’s often a sign of a worn or failing sprocket,” Michaud-Verreault indicates. “Worn sprockets, in fact, are the major cause of premature track failure. A sprocket, however, can be replaced for a mere fraction of the cost of a new track.”
The sprocket teeth should be the focus of your inspection. “They engage the interior tread of the track, and are carefully crafted to ensure the best fit with the specific make and model of your loader,” Michaud-Verreault explains. “Check the teeth for the appearance of a ‘shark-fin’ profile — the thinning and sharpening of the tooth — at the wear tips. This thinning of the metal, along with any broken teeth, will degrade the fit and will result in excessive wear and tear on the track itself. The shark-fin look tells you it’s time to replace the sprocket.
“Proper care, maintenance and sprocket inspection will more than pay you back in longer track life and reduced unplanned downtime, as well as maximizing efficiency,” she adds.