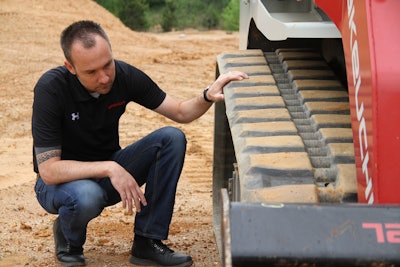
By Joseph Huling, Takeuchi Regional Service Manager
Maintaining the tracks on a compact track loader (CTL) is crucial for all the working parts to continue operating at peak performance. Owners of tracked machines should perform a daily inspection as well as visual checks for damage to the tracks.
The undercarriage will be a big portion of operating and maintenance costs over the life of a machine. Of all the undercarriage components, the track itself is the most likely to fail due to the operating stress or lack of maintenance.
Here is our step-by-step guide to combat fast-track wear and keep your machine on track.
Keep CTL Application in Mind
Before purchasing or renting a machine for the jobsite, it is always important to consider application. For instance, if the operator plans to work on hard, rough terrain, this will cause cuts or chunking of the tracks, which leads to excessive, premature wear. For applications such as this, a skid steer loader is best utilized.
CTLs are generally best utilized on softer ground conditions and sites where ground disturbance can be an issue.
It Starts With Safety
When inspecting a unit’s tracks, be sure to put safety first. Always perform any maintenance while wearing safety glasses, a hard hat, steel-toe boots, and gloves.
For any proper track tension questions, consult the recommendations in the OEM manual or check with a local dealer.
Take Your Measurements
Before performing maintenance to the track, first start by parking in a safe, level area. Once positioned, lower the lift arms and then tilt the bucket forward to raise the front of the machine as far off the ground as it will go. Shut off the CTL and climb out of the cab safely.
Once the operator exits the machine, it is important to measure the clearance between the middle track roller and where the surface of the track makes contact with the roller. The clearance of this machine should be anywhere between 15 to 30 mm.
After measuring, the operator is in position to make any necessary track adjustments.
Adjust Track Tension
Depending on measurements, tracks should be tightened or loosened as needed. Again, stick to 15 to 30 mm.
If the tension is too tight, it can speed up the track wear on sprockets and idlers as well as require more effort to rotate the track.
If the tension is too loose, it can derail the track and cause wear on the components. When the track rolls off, it can stretch beyond the normal threshold, rendering it hard to keep on. Track alignment is also important. If the track is loose, misalignment can cause major issues with the undercarriage components.
To increase track tension:
- Remove the access plate on the track frame
- Using a grease gun, inject grease into the tensioning cylinder through the grease fitting on the grease discharge valve
- Inject grease until the track tightens within the recommended 15 to 30 mm
To decrease track tension:
- During this procedure, the operator should be positioned away from the front of the grease fitting
- Loosen the grease discharge valve one complete turn to allow the track tension to decrease
- Tighten the discharge valve torque to 59-88 Nm
Once finished, be sure to clean up any discharge grease and reinstall the access plate. The operator can then put the CTL back on the surface and get to work with the comfort of knowing the tracks will be in good shape.
As the tracks go, so too does the machine. A simple daily check will get the CTL from point A to point B with ease for years to come.