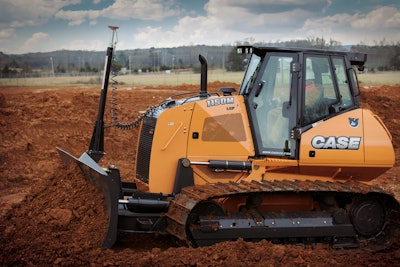
With the advent of electrohydraulics and advanced computing capability, dozer technology has leap forward with intuitive design. This allows the operator to tailor machine response to meet preferences in specific applications. In addition, traction control and load management systems make it easier for operators off all skill levels to increase productivity.
Case Construction recently introduced its M-Series dozers, with an emphasis on increased drawbar pull. But the technological innovations unveiled are probably just as important. “One of the biggest features is how the machine can be programmed to an operator’s liking,” says John Bauer, brand marketing manager at Case. This machine can be tailored to match an operator’s skill level and operating needs through an intuitive machine interface on the console. Shuttle and steering sensitivity can be set to three different modes –smooth, moderate or aggressive – by simply pushing buttons in the cab.
Complete control of the machine’s response to inputs is now at your fingertips. Fine grading on command slows the blade down at any given time. And on all but the two smallest machines, you can also adjust blade sensitivity. The two smallest machines are limited by manual control of the hydraulic valves, while electrohydraulics in the larger machines offer control-customizing flexibility.
“Job application may dictate how you want the machine to respond,” says Eric Nettleton, global product manager for Case dozers. Being able to customize response really aids the operator in being more productive. “We have gone through extensive customer validation, internal validation and through thousands of hours to develop what we think are going to be the most likable settings for shuttle, steering and blade sensitivity.”
Requirements on various sites change and this systems gives you the flexibility to change the dozer controls for the best fit. “If you are on a wide open site and you want to be real aggressive, you can set it,” says Nettleton. “If you are around houses in a residential area you can slow the machine down and adjust it to your liking, which aids productivity.” The machine interface also allows you to decide whether you want a decel pedal or a brake pedal. You can also cycle through machine health parameters on the fly.
A load-management system manages power output. “The computer recognizes the load the machine is under and will adjust the pumps and drive motors appropriately to keep the machine operating at the level that maximizes the output for the conditions,” says Nettleton. This reduces track slip. “You can go from 6 mph into a heavy push and the machine will adjust itself. You will never stall. The machine adjusts the speed range automatically.”
Despite the refined features, controls on the M Series are intuitive. “It is simple and easy to understand without having to pull out the operators’ manual,” says Nettleton. “You can do so much with hydraulic systems, computers and programming that change the performance. It is an easier solution.”
Controls have been grouped rather than having switches all over the machine. “We make it easy for an operator to jump in and be productive in a matter of minutes.” Another item you will notice when you enter the cab is a lack of cumbersome safety gates. With the Case M Series these have been replaced with a simple red button that deactivates the brake from the dash.
The new Case M Series offers technological advances that actually deliver simplified operation, and promise simplified maintenance.
Leibherr advances hydrostatic technology
Hydrostatic transmissions allow precise and infinite control. The speed of the dozer automatically adjusts to the load situation, thus ensuring optimum traction and minimizing track slip in all working conditions.
It is easier to run a hydrostatic machine compared to the torque converter machine because you don’t have to shift gears. “The machine basically does everything for you. You set the engine speed,” explains Klima. “You use your left side travel joystick to control the machine. You use your right side to control the attachments. That’s it. There are no gear changes and no engine speed changes.”
According to the task, the operator can easily select the desired speed and thrust on the joystick. When a new level is selected the travel drive settings adjust automatically and prepare the powertrain for higher performance demands. This has a direct effect on how aggressive the torque and speed on the sprockets gets ramped up and down.
Customers can choose between different controls for the travel drive of the machine. The preferred option is the proportional speed Liebherr joystick with an inching pedal. Even though the inching pedal is not required with the proportional joystick, it’s standard to make the transition from a conventionally driven dozer with a decelerator pedal to the Liebherr dozer easier.
By having this combination the operator can choose whether he wants to operate the machine with just the joystick or the joystick and the pedal. There are three different electronic settings for the aggressiveness of the travel drive.
Alternatively, the buyer can choose a joystick version of the machine that just controls the direction of the machine but not the speed. The speed then has to be controlled by the inching pedal. The top speed of the machine can be electronically limited. This setup is very similar in operation to a conventionally driven machine. However, the operator looses the benefits of the proportional joystick.
Liebherr also offers a power on demand feature called Power Boost. “There are certain situations, like pushing through a turn, where you need even more power,” says Klima. During those situations the machine will give you up to 15% more horsepower and torque out of the engine. This happens automatically, without the operator having to push any buttons.” The Power Boost intelligently adjusts the engine output to the load situation offering exceptional ripping and dozing power.
He adds, “As soon as the operator starts pushing the joystick to the left or right side, the engine controller gets a signal that there is a situation where we have a higher power demand, get ready for it. So the system is not reactive to the load, it is proactive to the load, which means you can get more power pushing through the turn and you have more efficiency. The engine doesn’t get pulled down and then have to recover. It stays at the engine rpm where it should be.”
Get work done faster and easier
One feature that Caterpillar introduced with the K2 family dozers is the power pitch blade. “The power pitch blade now allows the operator to adjust just the blade pitch from the operator’s compartment without having to get off the machine,” says Joel Fritts, small track-type tractor products, Caterpillar.
The blade pitch feature is a very simple and reliable device. “It is a simple hydraulic cylinder,” says Fritts. The operator is able to adjust this hydraulic cylinder from by pressing a button on the right-hand joystick. Whenever you start out your doze cycle you can rack the blade forward. “Rocking the blade forward gives you more penetration into harder material when you are trying to load the blade. After you load the blade and you want to carry the material you can rack it back, which allows you to carry more material and be more productive. At the end of the cycle when you want to dump the material you can press another button and rack the blade forward to help you empty the blade.”
Caterpillar has also introduced traction control on the K2 family. When the operator encounters a condition where there is an excessive amount of track slip, instead of raising the blade to reduce the load on the undercarriage or powertrain, the operator can press a button located in the cab area on the left-hand joystick. “Traction control reduces track slip which helps the operator optimize the blade loading capability,” says Dave Cusac, sales support consultant, Caterpillar..
To help the operator get the job done easier and faster, Caterpillar improved the blade control on the K2 dozer family. “Stable Blade is a feature we developed to enhance the operator’s control of the blade even while traversing rough terrain,” says Cusac. “This feature is designed to compliment the operator’s input into the implement control. When we ask operators how they know when to input a blade movement they tell us they go by the ‘seat of their pants’ feel. What this means is they operate a track type tractor by sensing the fore/aft pitch and side-to-side attitude of the machine.”
In addition, transmission and steering controls can be customized for operator preference. “We provide our operators with fully adjustable steering response and transmission control,” says Cusac. “The decelerator can simply be switched to be used as an engine decelerator or hystat drive control pedal to give the operator the ability to tailor the machine’s characteristics to their preference and to the job at hand. This ability to tailor the machine to each operator’s preferences significantly improves operator efficiency, adding productivity and helping novice operators.”
Komatsu integrates intelligence
Machine intelligence, which integrates GPS automatic grade control has been a design goal for Komatsu dozers. In May 2013 Komatsu introduced the D61i-23 with integrated intelligent machine control that can doze in automatic mode from first pass to last pass and provide additional efficiency up to 13 percent over a conventional aftermarket system. “The GPS controller communicates with a dozer controller to raise and lower the blade to achieve maximum load while limiting track slip,” says Charles Murawski, product manager, bulldozers, Komatsu America Corp.
The final surface is graded to accuracy within +/- 1.2 in. “All cables, masts and antenna have been removed from the blade to eliminate the need to climb onto the blade to install or remove components, usually on a daily basis,” notes Murawski. “Valuable machine control components are mounted internally and are well protected.”
To achieve optimum ground speed control and maneuverability, fine grading dozers incorporate a hydrostatic transmission. “To maximize productivity, the Komatsu hydrostatic transmission offers a unique choice of two different shift modes with the press of a button,” says Murawski. “Variable speed (20-speed) shift mode can be selected for fine grading operations and quick shift speed (3-speed) can be selected for heavy dozing applications. The 3-speed feels like a torque converter dozer that many operators are familiar with for heavy dozing, thereby increasing productivity.”
Komatsu dash 23 hydrostatic dozers limit track slip under heavy load by optimizing the match point of the engine and the hydrostatic transmission. “In addition, when GPS machine control automatic mode is selected in the D61i-23, the dozer blade is automatically lowered or raised to increase or decrease the load on the blade based on track slip,” says Murawski.
The amount of track slip is determined by comparing dozer travel speed by hydrostatic final drive rotation to the actual dozer travel speed by GPS signal. “Then the blade controller makes adjustments as required to reduce track slip,” says Murawski. “Several settings are available on the GPS monitor to match material density and specific surface conditions.”
Operator preferences for nine custom settings can be selected, saved in the monitor, then recalled for future use on Komatsu’s dash 23 dozers. They are:
- Power P-mode or economy E-mode
- Transmission shift mode 20-speed or quick shift 3-speed
- Quick shift 1st gear speed adjust faster, slower, or the same as factory setting
- Quick shift 2nd gear speed adjust faster, slower, or the same as factory setting
- Quick shift 3rd gear speed adjust faster, slower, or the same as factory setting
- Reverse speed faster, slower or the same as forward speed
- Hydrostatic steering normal or fine control
- Blade raise/lower hydraulics normal or fine control
- Foot pedal in engine decelerator mode or brake mode (no engine speed reduction)
“These setting can be saved in the monitor for up to five different operators and recalled with the push of a couple of buttons,” says Murawski. “This saves time and allows the machine to start work sooner.”