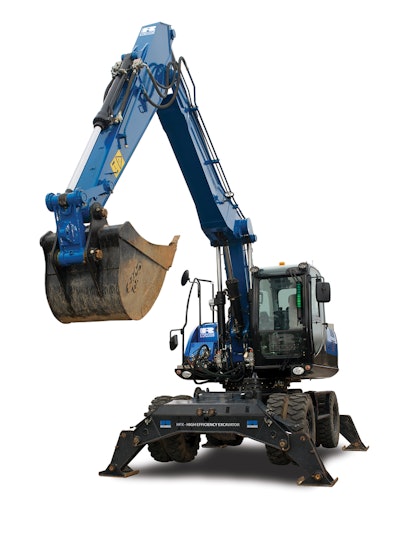
In the off-highway arena, there has been movement toward the electrification and hybridization of equipment.
“For machine operators to be compelled to buy a hybridized or electrified version of a product, it must positively impact their life-cycle cost,” says Ricardo’s Dr. Scott Anderson. So the three basic aspects of life-cycle cost must be considered with respect to hybrids — the impact of the system on acquisition cost, the beneficial impact on operating cost and the useful life.
When you consider the case for on-highway hybrids, the first thing that probably comes to mind is energy recovery. “For off-highway, those opportunities exist, but they are more limited,” says Anderson. For example, you can recover the potential energy when dropping the boom or slewing an excavator.
But the more important application of hybrid technology is the ability to peak load shave and handle transient engine loads, which allows you to size the engine for a steady-state base load. “One option is to run the engine at an even higher engine power level and extract more from the machine for better productivity,” says Anderson. “That also increases the engine load and leads to better fuel efficiency.”
Another option is to use a lower engine rating to get the same job done. “That can be particularly important for applications near U.S. emissions break points as an enabler for a less costly emissions solution near displacement break points in an engine manufacturer’s portfolio,” says Anderson. “Finding opportunities near Tier 4 displacement break points may allow products to be developed that produce the performance of conventional products rated above the break point, but using a hybrid with a smaller engine that fits below the break point. That will help reduce cost and offset the hybrid system cost.”
Quick Transition Unlikely
Don’t expect hybrids to become mainstream overnight. “Off-highway OEMs are moving cautiously on hybrids, even where great technical solutions exist,” says Anderson. “The business case must be sensible. Because customers in this market expect high reliability, hybrid systems require extended validation before OEMs risk putting them into production.”
Today, there are a few hybridized vehicles available. “The first production hybrid applications have deployed predominately electrical technology,” says Anderson. These include the Hitachi hybrid excavator, the Caterpillar D7E dozer and the John Deere 644K wheel loader.
That does not mean hydraulic hybridization doesn’t deserve closer examination. “Because many off-highway machines already have high-pressure hydraulic systems on board, it is natural to consider the use of other technology for hybridization, such as hydraulic energy storage,” notes Anderson. “Applications that have high power, but not particularly high energy storage requirements, are typically in the sweet spot for hydraulic hybrid options.”
One major consideration when it comes to hybrid technology is the useful life of the machine. “The effects of hybrid operating costs are amplified as the useful life of the system is extended,” says Anderson. “It is important to identify an application in which the vehicle is retained for long periods of time.”
You can also drive life-cycle costs by minimizing the initial cost of the technology. “For that reason, Ricardo feels there are applications for which flywheel system technology will be an ideal solution,” says Anderson. “We recently demonstrated a flywheel system on an excavator. The Ricardo demonstrator featured a hermetically sealed carbon fiber rotor driven through a magnetic gear for high efficiency. Using the magnetic gear drive allows us to remove the rotating seals and reduce the losses in the flywheel. It also eliminates the need for a vacuum management system.”
Ricardo expects the flywheel system to be considerably less expensive than the electric hybrid systems. “We should be targeting payback in less than two years,” says Anderson. “The flywheel avoids the significant battery replacement costs that may be needed in some electric hybrids. Because Ricardo believes the flywheel will deliver the best payback in some off-highway applications, we are continuing the development of production intent hardware.”