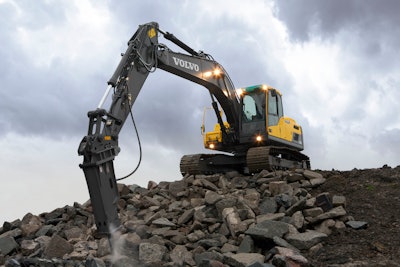
Electrohydraulic (EH) excavator controls allow response rates, flows, pressures and even control preferences to be tailored through in-cab monitors. While beneficial to all excavators, mid-size and larger excavators are leading the way forward.
“There has been a trend toward advanced hydraulic control technology on larger excavators because the cost of parts for the advanced hydraulic control technology was relatively cheaper on the larger models than the compact units when considering the whole product’s cost,” says Sejong Ko, product manager, Volvo Construction Equipment. “Excavators are all tool carriers no matter the size — that means advanced auxiliary control technology makes economic sense in certain size classes, but will do well on other sizes later.”
There is a definite advantage to controlling flow and pressure based on demand. “On the jobsite, excavators should move the boom, arm, tracks and/or swing joint at the same time when an attachment is in use,” says Ko. “With EH control, the machine can calculate and provide the best distribution of hydraulic power between the actuators and attachment. Operators can adjust and set a priority for the attachment.”
“EH controls — particularly the EH attachment controls — allow the operator to run the machine with the controls at his fingertips, either proportionally or ‘on/off’,” says George Lumpkins, national service manager, Kobelco USA.
This choice adapts the excavator to the attachment being used. “Proportional control is particularly important for some attachments, such as the thumb, whereas the ‘on/off’ is more useful for breakers and compactors,” says Jeff Fletcher, service trainer, Kobelco USA.
Stored Settings Reduce Workload
Many adjustments can be made through Doosan’s in-cab monitors. “Probably the biggest one is the ability to control and pre-program five one-way flow attachments and two two-way flow attachments,” says Lee Smith, excavator product specialist. In addition to optimizing flows and pressures for each attachment, you can program the engine speed range for the machine with that attachment. “It is a real time-saving feature for an operator who is switching between a number of different attachments throughout the course of a week.”
Volvo mid-size excavators allow selection of a hammer/shear function, preferred hydraulic pressure (maximum pressure) and primary auxiliary flow and secondary auxiliary flow for attachments to be controlled through the in-cab monitor. “The hammer/shear function (primary auxiliary pressure set between high and low pressure) is to operate attachments requiring relatively high hydraulic flow such as hammers, shears and thumbs,” says Ko. “The secondary auxiliary flow is the auxiliary hydraulic line to operate attachments that require constant flow, which is relatively lower than primary auxiliary flow. This is perfect for attachments such as rotators, mowers and hydraulic magnets. Operators can select one of three response modes for both machine response and secondary auxiliary response — active, normal and soft.” With the response modes, operators can adjust the movement sensitivity.
Many adjustments can be made through Doosan’s in-cab monitors. In addition to optimizing flows and pressures for each attachment, you can program the engine speed range for the machine with that attachment.
This saves attachment installation time, as well. With saved attachment settings, hooking up the attachment and hoses is now the bulk of the work. “After the attachment and hoses are hooked up, you can go into that monitor, select your attachment and go to operation,” says Smith.
Many excavator manufacturers, including Volvo and Kobelco, offer up to 20 different settings in the monitors for increased efficiency. “The benefits are numerous for customers who need to switch attachments frequently,” says Volvo’s Ko. “Special application customers, such as those who perform demolition, like to preset hydraulic pressure and flow for their multiple attachments. In addition, some customers don’t need to switch attachments, but still like this function because the in-cab monitor setting allows operators to set up pressure and flow in greater detail.”
“Kobelco excavators can control auxiliary flow for both one-way and two-way attachments,” says Lumpkins. “On mid-size excavators, you can set 10 bidirectional attachment pressure and flow settings, as well as 10 single-directional attachment pressure and flow settings.” Without advanced in-cab controls, the flows and pressures would have to be manually adjusted.
Customized Controls Simplify Operation
There are many ways manufacturers capitalize on EH control capabilities. “For us, it has been the ability to combine features and functions of the joysticks with the monitor,” says Aaron Kleingartner, marketing manager, Doosan.
Doosan excavators feature the ability to rotate the portion of the joystick that contains the buttons and sliders. The machine comes standard with buttons on the left-hand side of the joystick and the slider on the top. “The slider moves from left to right. So if you were running a tilting bucket, that side-to-side slider would be intuitive to the operator,” Kleingartner explains.
The joystick section can also be rotated. If you are running a clamp or a thumb, this allows the slider to move up and down on the joystick. “It is going to move in the same direction as the clamp is going to open or close,” says Kleingartner. “That also turns your button to the side, but it is a little more intuitive with our operators.”
The ability to store settings and customize controls proves beneficial to both operators and owners. “It is a benefit to the operator sitting in the cab that they can operate how they prefer, and it is a benefit to the owner who has made an investment in that machine that they are getting the life out of the machine and the attachment,” says Kleingartner.
Continuous Flow Control Options Tailor Application
Doosan excavators feature the ability to rotate the portion of the joystick that contains the buttons and sliders. This changes the direction of the slider and makes operation more natural for the operator.
Volvo excavators also adjust the response mode for the attachment, allowing a choice between soft, normal or active response.
Doosan excavators provide the ability to modify or select the way the operator would like the detent button to operate. For instance, when operating a breaker, some operators want the breaker to engage only when a button is held; others want the breaker engaged when a button is pushed and for it to continue to cycle until it is pushed again.
“If operators are fairly new to running a breaker, they may want it to only engage when they are holding the button,” says Smith. “Those who are more experienced in operating that machine may want the breaker to stay engaged and turn it on and off just with the push of a button. They don’t want to hold the button the whole time they are operating.”
He adds, “Other functions that we can change through the monitor are the ability to operate two-way hydraulics either through a button on the joystick or a pedal on the floor. There are operators who definitely have a preference when running thumb or clamp attachments.”
Monitors Offer Insight
Of course, the onboard monitors do much more than control auxiliary hydraulics. “Productivity can be increased by monitoring traveling hours, idling hours, digging hours and machine work load,” says Lumpkins. “Productivity can also be increased by monitoring maintenance intervals. General maintenance items can be scheduled so that they don’t interrupt production.
“Since Kobelco excavators have three different work modes, productivity can be maintained for the task being performed while also decreasing operating cost,” he continues. “All of this information can be viewed remotely through a computer, tablet or smartphone using our KOMEXS system.”
The monitors on Doosan excavators can be used to track how long the machine has been operating in one-way or two-way mode. “The benefit ties back to the primary use of the machine, giving the owner/operator a picture of the total hours and the usage,” says Kleingartner. “If you track it even further back with the fuel tracking on our machines, it can allow the owner/operator the ability to better bid projects. If you know a machine has been working 50 hours in one-way mode, you can track that fuel usage. When you bid, you will know what your fuel costs are going forward.”
You can track how many hours the excavators were used in each of the various work modes. “This gives you the ability to understand the machine itself, and also gives an owner the ability to understand the different operators, what their preferences are and how they like to operate those machines,” says Kleingartner.
Control Technology Goes Compact
Many compact excavators now benefit from the same technologies adopted for mid-size and larger models.
“The technology previously seen on large excavators — such as lift overload monitors, depth control systems and auxiliary flow rate controls — is filtering through to the compact market,” says Thomas Clapton, product sales engineer - compact excavator global growth, JCB. “Much of this technology migration has occurred in machines around 8,800 lbs. and above, where operators require enhanced efficiency and the versatility to work with a wide range of hydraulic attachments. There is a natural point at which the cost of advanced hydraulic features stops being economical, especially in machines smaller than 4,400 lbs.”
Much of the technology migration from larger excavators has occurred in machines of around 8,800 lb and above, where operators require enhanced efficiency and the versatility to work with a wide range of hydraulic attachments.
In-cab monitors are also increasing the capabilities of smaller machines. “The new generation of JCB compact excavators provide the operators with full control of all hydraulic functions — including auxiliary controls, hydraulic quick hitch and auto venting — via in-cab monitors,” says Clapton. “In addition, the operator can use the main display monitor to set hydraulic flow rates on both the high/low-flow double and single auxiliary circuits.”
With in-cab monitors, operators can now swap attachments without a need for time-consuming calibration.
“Operators of large excavators appreciate the convenience and readily accept the addition of these new features in compact excavators,” says Jeff Jacobsmeyer, Kubota product manager for excavators, wheel loaders and TLBs. “EH controls have made the machines more friendly and efficient for operators. For example, a simple thumb switch is now used where a foot pedal or lever once was. Adjustments for flows are done electronically from the cab without having to use tools or flow meters to set the correct amount needed.”
Cost is a critical consideration when adding such features to smaller models. “Manufacturers do their best to make this technology available and affordable for the smaller compact units,” says Jacobsmeyer. “As technology changes, sometimes it becomes less expensive for manufacturers to add these features in smaller machines.”
On the Kubota compact excavator line, operators have the ability to "dial in" the auxiliary flow needed for particular attachments.
One difference on the company’s machines is that the pressure stays constant. The adjustment is also more precise than just a High, Medium or Low setting. “The AUX flow setting is variable to assure the best results for the attachment needs, and the flow can be controlled separately for both one-way and two-way operations,” says Jacobsmeyer.
Kubota also offers five stored presets on many of its models. Dash icons are used as an indicator for the attachment that is desired. “When the operators install a breaker, they can simply select the breaker icon and the preset memory is ready to supply the proper flow for maximum efficiency to the attachment,” Jacobsmeyer points out. “Switch to another attachment, maybe an auger, select the proper icon and it is ready to go to work.”
Some attachments see greater benefit from fine control adjustments. “Two-way controlled cylinder operations may benefit the most,” Jacobsmeyer comments. “The return stroke of a cylinder is faster because of less displacement. With the flow control for separate operations, the operation for open and closed can be perfectly matched. For example, the speed of a thumb can be programmed to open and close at the same speed and precision.”