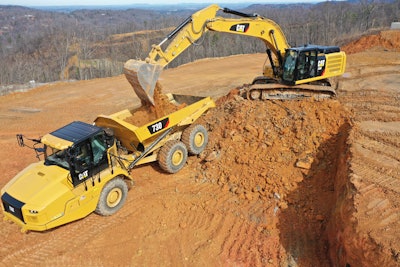
C. Laney and Sons Construction is well-versed when it comes to rigorous jobsite conditions. It performs general construction, infrastructure, road building, site work, and related projects, often at high altitudes and severe slopes in the Great Smokey Mountains.
Speaking at a Caterpillar press event last November, Charles "Chuck" Laney, president and CEO, described one project where crews were rebuilding a fire-damaged facility, including demoing all of the concrete and removing the steel and iron and infrastructure. The slopes were 45° or greater in most cases. “We actually have slopes that are 1:1 alongside of the road,” he notes.
“Our sites are very adverse. They’re very demanding on the operator, they’re very demanding on the equipment. It’s easy to get hurt if you don’t pay attention,” he continues. “So, you need the best equipment and you need the best technology that will enable you to produce the best product and do it in a safe manner.”
Getting in the Dirt
Chuck started C. Laney and Sons Construction in 1980 with his with Rosemary. Their three sons, James, Frank and Luke, now make up the rest of the management team for the family-owned business based in eastern Tennessee. Luke is VP of operations and primarily works on bids and securing projects. However, he started as an equipment operator, working in the field when he wasn’t attending school.
The company provides comprehensive general contracting and design-build services to corporate, institutional and developer clients. “We do general site work and we actually provide a complete product. We do infrastructure, road building and we also build buildings,” says Chuck. “The ability to have the equipment to facilitate our projects so we don’t have to wait on any excavation contractors has been a big asset to us over the years. It’s built our customer base very well.” He adds that an average project can be $25 million on up.
“We are a general contractor primarily,” agrees Luke, “but we do infrastructure and site work to get the complete job. We started that about 14 to 15 years ago.”The contractor maintains a small fleet of site work equipment, which allows it to self-perform dirt work on its building projects.C. Laney and Sons
The company maintains a relatively small fleet of site work equipment. “We have anything from a Cat 299 skid steer all the way up to a 336 excavator, but we don’t have a ton of them,” says Luke. “We do have some good operators and it allows us to do dirt work ourselves.”
C. Laney and Sons used rental over the years to help it build up its dirt and site work capabilities, but has also purchased equipment, including Caterpillar’s 323 Next Generation excavator. As a rule, C. Laney and Sons’ equipment is three years old or newer. “We want to be up front with new equipment, new technology, and we want our customers to be proud of our jobsite,” says Chuck. “We don’t want our machine to look like it fell off the truck.”
Having top of the line equipment also instills a certain pride of “ownership” in the operators. “We try to make the equipment that operator’s machine… They really take care of it and take pride in it,” says Luke. “That’s a big thing for our operators.” It helps ensure machines are well maintained and less subject to abuse.
Tech Saves Major $$s on Dirt Work
As of last November, C. Laney and Sons had been using its Cat 323 for eight months. Luke notes that the machine is a good size for the company due to its versatility. “We can use it for utilities… It’s also efficient for loading trucks,” he explained. “It’s a small enough machine that we can move it easily, which is important where we’re at – we’re in a very mountainous terrain so we may not be able to get a 336 in to move dirt where we need to.”
Three Next Generation Cat Excavators Deliver More Choices in 20-ton Size Class
The new machine has proven more fuel efficient vs. its predecessor. C. Laney and Sons has seen roughly half a gallon an hour in fuel savings with the new 323 vs. its 323F – around a 15% to 20% savings even given the rugged applications experienced. But that isn’t what impresses Chuck the most.
C. Laney and Sons has seen around a 15% to 20% fuel savings with the new 323, even given the rugged applications experienced.C. Laney and Sons
For example, if the company puts in a mile of water line and the operator over digs the ditch 6 in. or a foot continually, it means an excess of spoils have been removed and must be disposed of, plus there is more backfilling required. “I could spend maybe $25,000 extra in a week for stone backfill because I over dug the ditch continually. With this new equipment, I can tell the machine not to let [the operator] do that,” Chuck points out. Operators can also program it themselves. “The operator quits over-digging the ditch, and I’ve made more money for myself and my customer. As a contractor, our biggest job is to make sure the owner gets what they pay for. That’s our goal.”
[VIDEO] Family-run Construction Firm Sees Next-Generation Benefits of Caterpillar 323 Excavator
The company also uses the 2D system quite a bit when setting block walls. “It’s very flexible for our operators. The wall system we use is very flexible, as well,” Luke says. Operators no longer have to follow stakes. They simply reach out with the excavator arm, touch a bench to set the system, cut and repeat the process as needed to reach the required elevation. “All of that makes the 2D great.”
The contractor has used slope grade control in many different ways, and not necessarily how they thought it would be used. “We use it if we’re digging sewer lines for rough grade so we don’t have to have a man in the ditch with a grade rod,” says Luke. “It’s one less guy, and it’s safer also. That’s a big deal for us, especially in the mountains, where we get some that are pretty deep. The sewer lines can be anywhere from 16 to 20 ft. deep at times.”
Chuck adds, “The machine is telling us what the grade is. You’ve eliminated [the need for a grade checker in the ditch], and he can be doing something else – maybe even teaching him to run a machine.” The ability to avoid over digging on, say, a 20-ft.-deep trench also adds up to significant savings. “We might have cut a $100,000 off of a project…”
Cutting Downtime and Maintenance Costs
Stowers Equipment, the local Caterpillar dealer, had recently sent technicians out to the contractor’s location to install the latest tech upgrades onto the 323. With the on-site update, the machine gained certain features introduced on the latest Next Generation models. “You couldn’t have done that with a different type of machine,” Chuck comments.
Latest Caterpillar Next Generation Excavators Match Productivity & Cost Targets
The update included a Lift Assist function. “I can see a lot of applications for that, especially where we’re setting manholes,” says Luke. In particular, he cites when operators attempt to boom out while moving the manholes and risk tipping the machine. “Now they know to stop before they get there.” The feature should also prove useful when moving 2,500-lb. blocks for retaining walls.
There are ergonomic benefits to the new excavator, as well. Chuck notes that older machines often forced operators to crane their neck to look around the machine, or reach behind to access certain controls. Now, the touchpad lets you control functions with the push of a button. He specifically points to how easy it is to use the touchpad to control the radio or HVAC system. “I’m 66-years-old, 67 in a few days, and all these things you would think I’d be afraid of – but I love it,” he says. “Even the way the window opens is so much better… It’s so much smoother than an older machine, and that’s just a basic thing.”
“[Technology built into the 323] helps in so many ways that we probably didn’t even think of when we bought the machine. There’s a lot of things that we’ve discovered," says Luke Laney, VP of operations.C. Laney and Sons
Take the e-fence feature, which provides automatic swing stop. While typically used to set a “fence” for the front of the machine, C. Laney is using it to protect the rear of the machine. According to Chuck, when working on a mountain slope with large trees all around, there is a tendency for the machine to swing faster down slope. If the counterweight connects with a tree, it can mean $7,000 to replace a side panel, or upwards of $17,000 or more if you wrap a frame door around a tree.
“With that fence in there, it helps protect that piece of equipment,” he points out. “For safety, it also helps prevent you from hitting a person, [equipment or vehicle] behind you. Just the damage to the equipment alone, that fence is worth the money right there.”
Chuck feels the telematics on the Cat equipment has been another great asset. “We don’t suffer from downtime,” he states. “When I started out, I thought I had to fix [all the equipment] myself. I crawled up in there, pulled the parts off and ordered [parts] and repaired them. We quickly learned over the years that downtime was the killer of profit.”
Now, the telematics system will contact Stowers Equipment directly if there is a service problem and the dealer will send a tech out to service the equipment, whether it’s to change filters or oil or to resolve a larger issue. “They have the historical data to tell us how much wear has been on that equipment. And we found out that we did not miss a single penny of that investment,” Chuck says. “We actually gained more money by doing that in our operation… We don’t have that downtime that kills us.”